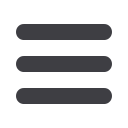
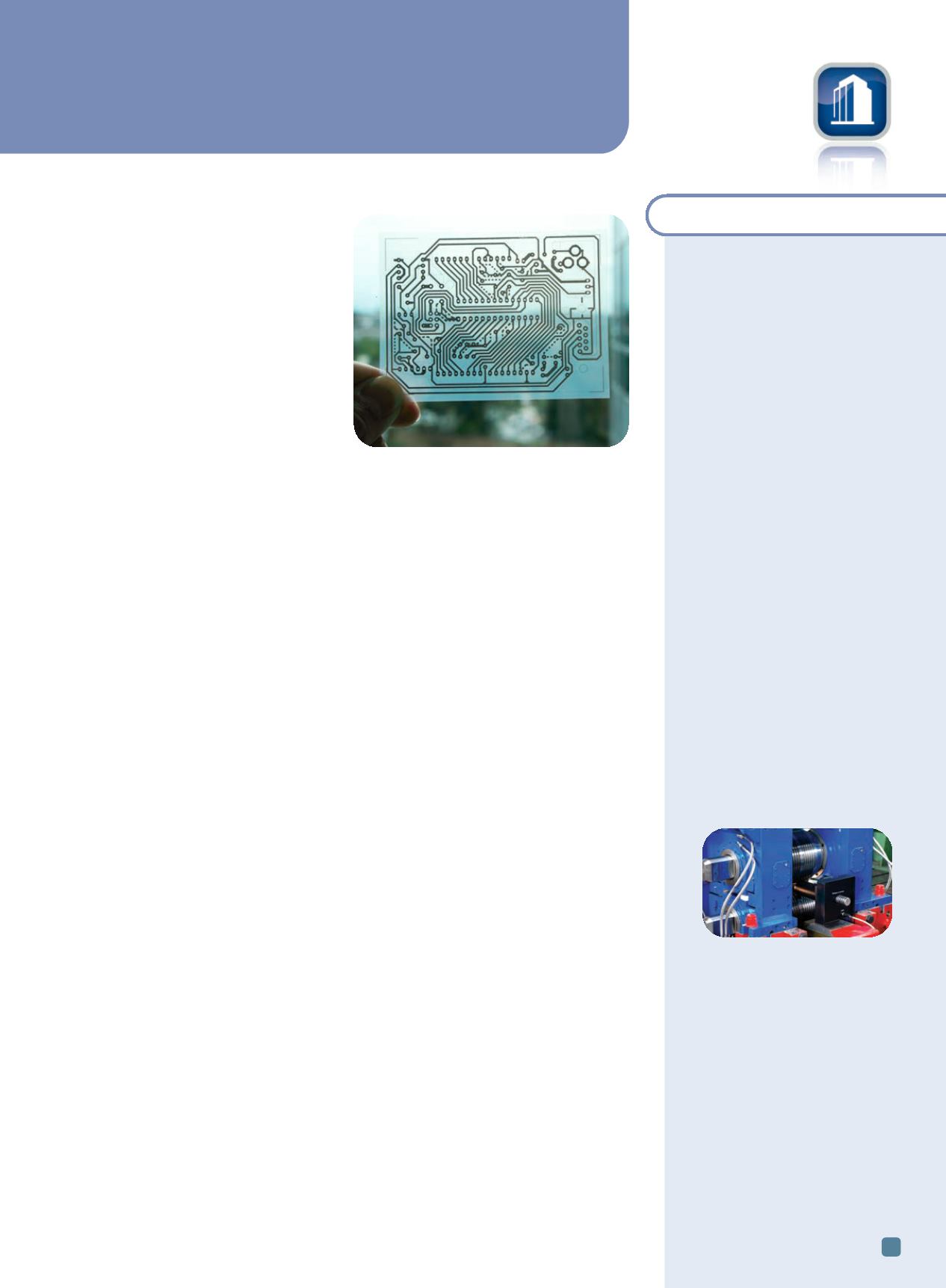
ADVANCED MATERIALS & PROCESSES •
JANUARY 2014
11
P
ROCESS
T
ECHNOLOGY
news
industry
briefs
Lincoln Electric Holdings Inc.,
Cleveland, acquired an ownership
interest in
Burlington Automation
Corp.,
a manufacturer of 3D
robotic plasma cutting systems.
Based in Hamilton, Ontario, the
company serves the structural
steel, construction, oil and gas,
and general fabrication markets in
North America, with its main
products sold under the PythonX
brand. Lincoln Electric also will
acquire
Robolution GmbH,
a
European provider of robotic arc
welding systems. Based outside of
Frankfurt, Germany, the company
serves leading automotive OEMs
and Tier 1 suppliers.
www.lincolnelectric.com.
Siemens Metals Technologies,
Austria, won an order to supply
Chinese steel manufacturer
Qingdao Special Iron & Steel Co.
Ltd.
with a flat bar rolling mill. The
new mill has a production capacity
of 600,000 metric tons a year and
manufactures flat bars with widths
of between 60-160 mm and
thicknesses from 6-60 mm for
applications in the automotive and
construction industries.
Commissioning is scheduled for
early 2015.
www.siemens.com/metals.Sizing train from Siemens.
Novelis Inc.,
Atlanta,
commissioned a $200 million
expansion of its rolling operations
in Oswego, N.Y., increasing the
company’s North American
capacity for producing automotive
aluminum sheet by 240,000 tons,
five times their existing capacity in
the region. The Oswego facility is
an integrated recycling, hot rolling,
and cold rolling complex producing
aluminum sheet for the beverage
can, automotive, and building and
construction industries.
www.novelis.com.
Novel method cranks out inkjet-based circuits
Researchers from Georgia Tech, the
University of Tokyo, and Microsoft Re-
search developed a new method to rapidly
and inexpensively make electrical circuits
by printing them with commodity inkjet
printers and off-the-shelf materials. For
roughly $300 in equipment costs, anyone
can produce working electrical circuits in
the 60 seconds it takes to print them. The
technique, called “instant inkjet circuits,” al-
lows the printing of arbitrary-shaped con-
ductors onto rigid or flexible materials and
could advance the prototyping skills of
non-technical enthusiasts.
“We believe there is an opportunity to
introduce a new approach to rapidly proto-
typing fully custom-printed circuits,” says Gregory Abowd, Regents Professor in the School
of Interactive Computing at Georgia Tech and an investigator in the study. “Unlike exist-
ing methods for printing conductive patterns, conductivity in our technique emerges within
a few seconds and without the need for special equipment.”
Recent advances in chemically bonding metal particles allows researchers to use silver
nanoparticle ink to print the circuits and avoid thermal bonding, or sintering, a time-con-
suming and potentially damaging technique. Printing circuits on resin-coated paper, PET
film, and glossy photo paper works best. The team also made a list of materials to avoid,
such as canvas cloths and magnet sheets. To make the technique possible, researchers op-
timized commercially available tools and materials including printers, adhesive tape, and
the silver ink. Designing the circuit itself was accomplished with desktop drawing soft-
ware, and even a photocopy of a drawing can produce a working circuit. Once printed, the
circuits can be attached to electronic components using conductive double-sided tape or
silver epoxy adhesive, allowing full-scale prototyping in hours.
For more information:
Gregory Abowd,
gregory.abowd@cc.gatech.edu,
www.cc.gatech.edu.
Single-step auto parts manufacturing via thixoforming
Following years of research, the technology involving thixoforming—the shaping of
metals in a semi-solid state—is beginning to yield results. CIC marGUNE, the Cooperative
Research Centre for High-performance Manufacturing, Spain, is exploring the possibility
of modifying the current process for manufacturing automotive parts, using thixoforming
technology instead. Research is being conducted in collaboration with nearby CIE-Legazpi
and Mondragon University to simplify the current process of manufacturing auto parts,
which typically consists of three or four steps.
“The aim is to produce the final part in a single step, which would bypass the whole
process in between,” says Mikel Intxausti of CIE-Legazpi.
As yet, there are no manufacturers using this process, which is why Mondragon Univer-
sity engineer Jokin Lozares is working with a clear goal in mind—taking thixoforming tech-
nology from the lab to industry. On a laboratory scale, researchers have already managed to
reduce to a single step what in industry now requires three or four different procedures. Dur-
ing thixoforming, material is kept between a liquid and solid state and is shaped in that semi-
solid state, which offers certain advantages in comparison to conventional forging.
“To produce the same part, thixoforming technology uses about 20% less material than
forging, because no surplus material is obtained in the new process, and the final part with
the desired geometry is directly achieved,” explains Lozares. “A process that now requires
three or four steps is cut to a single step, allowing infinitely more complex geometries to
be achieved.”
www.margune.org.
A single-sided wiring pattern for an Arduino
microcontroller is printed on a sheet of coated
PET film. Courtesy of Georgia Tech.