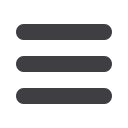
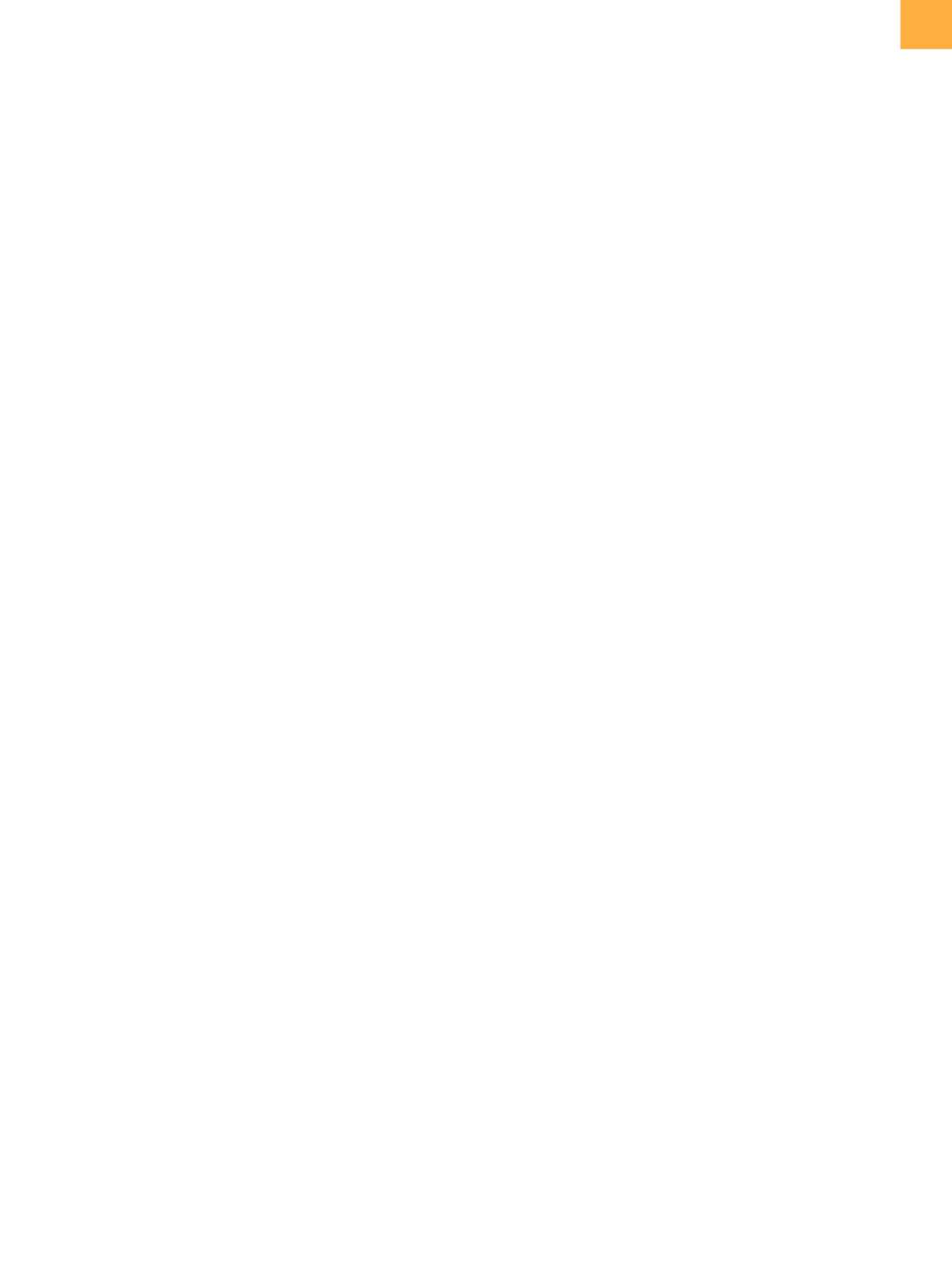
edfas.org
31
ELECTRONIC DEVICE FAILURE ANALYSIS | VOLUME 18 NO. 4
microscopy face challenges to identify the correct defect
area with the sample still fully functional. In addition,
sample-preparation techniques such asmechanical cross
sectioning and top-down sample delayering are reaching
their limitationswhere preparation artifacts can no longer
be neglected.
ANALYSIS OF CURRENT PACKAGE
FA FLOWS, CHALLENGES, AND
REQUIREMENTS
While complex packaging is desired from a product
point of view, it also induces additional risks and challeng-
es regarding manufacturing yield, device performance,
and life-time reliability. Considering these facts, a new
threshold of requirements for successful FA is introduced:
• Using copper as the main material for TSVs and
micropillar realization induces a coefficient of thermal
expansion (CTE) mismatch to silicon material. As a
result, thermal and mechanical tension can lead to
crack introduction.
FA request:
Sample preparation is requested to avoid
smearing effects during mechanical cross sectioning.
• Using thinned-die technology (e.g., interposer), espe-
cially on large package products, raises the influence
of warpage and die-bowing effects. Similar to CTE
mismatches, these can introduce crack propagation
and layer delamination.
FA request:
Handling of thin but large sample sizes;
compensation for stress relaxation during sample
deprocessing.
• Shrinking interconnect dimensions lead to a require-
ment to lower critical void size and concentration.
FA request:
Artifact-free sample preparation and
cross sectioning; early failure detection with shrinking
defect size.
Analyzing these requirements, the need to maintain
overall device functionality and therefore nondestructive
testingand fault isolationbecomesapriority. Furthermore,
after successful defect isolation, a precise and local target-
preparation method is desired that allows root-cause
imaging in any layer inside the package stack. Although
these requirements are not fully new to the FA industry,
current state-of-the-art methods face their physical
limitations:
• Optical-based methods, such as photon emission
microscopy, optical beam-induced resistance change,
or laser scanning microscopy, are often used for fault
isolation but face limitations due to the complex
package setups that block optical access for fully pack-
aged devices.
• Confocal scanning acoustic microscopy is often used
for delamination or crack detection within package
products. However, due to the increasing layer and
material amount combined with shrinking intercon-
nect size, early defect detection becomes more and
more difficult.
• Time-domain reflectometry is capable of isolating spe-
cifically the defect depthwithin the package. However,
due to its pulse length in the megahertz range, it
cannot keep up with the shrinking interconnect size; a
z
-resolution limit is increasingly hindering successful
defect isolation.
• Mechanical cross sectioning is a state-of-the-art, fast,
and effective way to achieve root-cause analysis.
Within the introduction of copper-based interconnects
and shrinking feature size, a shift toward focused ion
beam (FIB) techniques is recognizable. As for package
FA, standard FIB tools suffer from inadequate beam
currents, which results in long cross-sectioning times
in the tens-of-hours range.
EMERGING PACKAGE FA METHODS FOR
2-D/2.5-D/3-D PRODUCT ANALYSIS
To overcome the limitations mentioned in this article
and to meet FA requirements, several techniques have
been either further or newly developed:
• Lock-in thermography
(LIT) is a thermal defect localiza-
tionmethod that canbe applied for short localization in
3-D. Its resolution and sensitivity aswell as the capabil-
ity to isolate defectswithin specific 2.5-D/3-Dpackages
havebeensuccessfullydemonstratedandpublished.
[4,5]
• Superconducting quantum interference device (SQUID)
or magnetic current imaging
has been further devel-
oped to isolate both shorts and opens and has been
an often-applied board-level FA tool. Current devel-
opments aim to adapt this concept toward CSP-sized
samples.
[6]
• 3-D x-ray
has been widely adapted for semiconductor
needs, and it provides high resolution and sensitivity.
With the optimizationof sources anddetectormaterial,
a significant decrease in measurement time has been
noticed. 3-D x-ray microscopy (XRM) offers a solution
for structural analysis in complex 3-D integrated circuits
because it can nondestructively penetrate through
stacked materials and visualize internal structures
with high resolution, even for intact 200 and 300 mm
(continued on page 34)