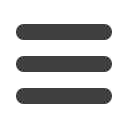
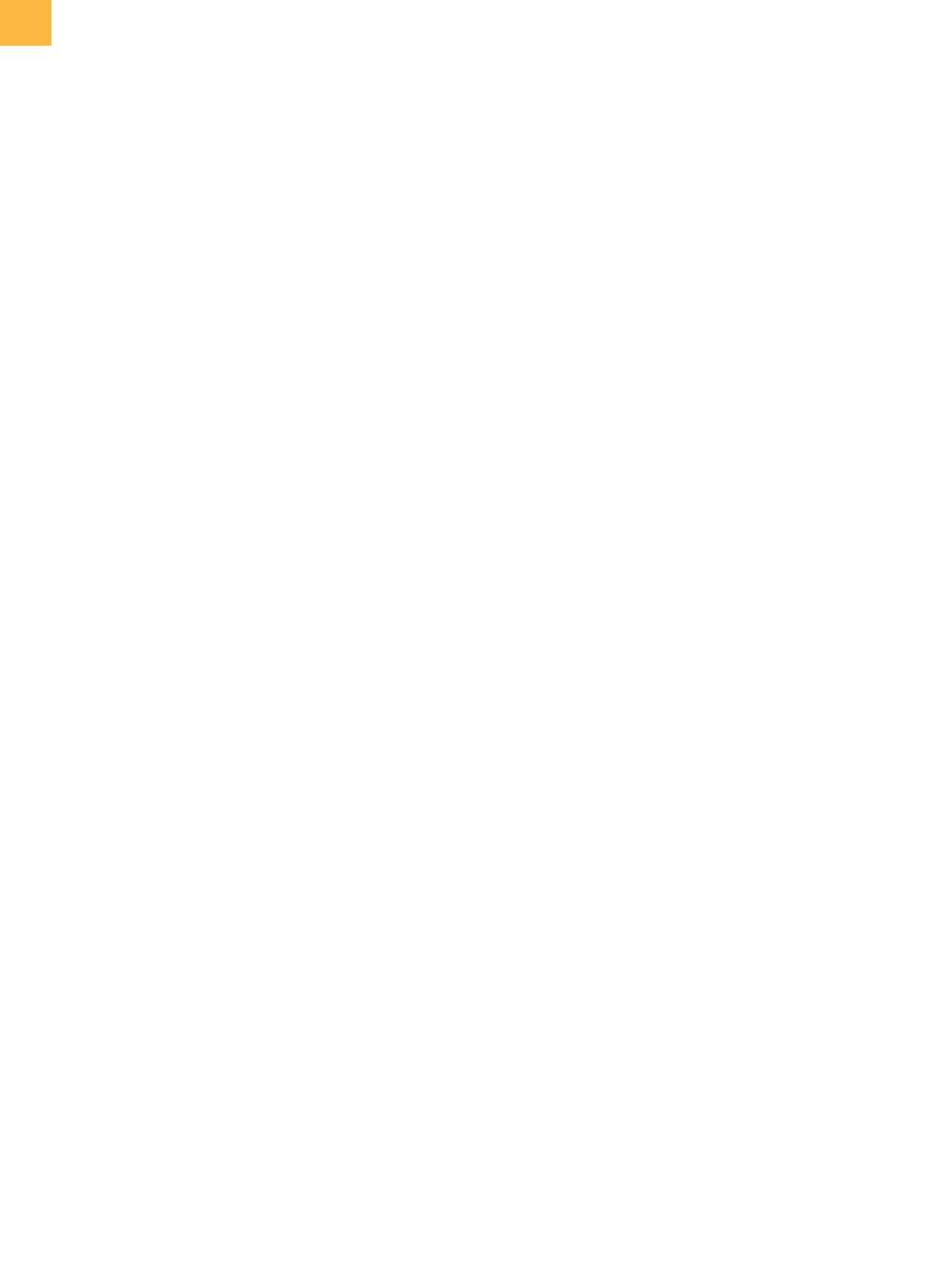
edfas.org
ELECTRONIC DEVICE FAILURE ANALYSIS | VOLUME 18 NO. 3
10
TAKE A CLOSER LOOK AT ELECTRICALLY-ENHANCED
LADA: SETUP
S.H. Goh, B.L. Yeoh, G.F. You, Y.H. Chan, Zhao Lin, and Jeffrey Lam
Globalfoundries, Technology Development, Product/Test and Yield Engineering, Singapore
and
C.M. Chua, Semicaps Pte Ltd., Singapore
SzuHuat.Goh@globalfoundries.comINTRODUCTION
On sub-28 nm process technology, silicon patterning
conformance to design, especially front-end-of-line, has
run up against the limits of physics, bringing about a para-
digm shift from defect-limited hard failures to increasing
occurrences of design-margin soft failures as a result of
the shrinking process window. Therefore, the role of soft
defect localization (SDL) techniques in yield engineering
has become more important. It is common to speak of
SDL and laser-assisteddevice alteration (LADA) when such
failures need to be investigated.
LADA uses a continuous-wave 1064 nm photo-
current-inducing laser to temporarily alter transistor
characteristics through the silicon substrate. The outcome
is a flip in the tester pass-fail state. The position of the
scanning laser is correlated to the state transition and reg-
istered for signal image acquisition.
[1]
Such an approach is
well known to be effective for localization of speed path
degradation
[2]
and subtle process defects.
[3]
The applica-
tion of LADA extends beyond such spatial localizationwith
the innovation of time-resolved LADA (TR-LADA), which is
capable of extracting temporal information from the fail-
ures by using a 1064 nm pulsed laser to “probe” different
test cycles in each test loop.
[4]
It offers new insights, such
as failure mode identification
[5]
and knowledge of propa-
gation delays.
[6]
In some cases, an improved LADA signal
spatial resolution has also been observed.
[7]
The current
state-of-the-art inTR-LADA is basedon a 50 ps pulse-width
laser that enables the interrogation on a single test cycle.
As a matter of fact, both LADA and TR-LADA signals can
be attributed to either potential sites of existing issues or
devices with low threshold to laser stimulation, the latter
also known as artifacts. There is no means to intuitively
differentiate between the two by merely monitoring the
transition of test pass-fail states. This is the main moti-
vation behind the innovation of electrically-enhanced
LADA (EeLADA).
[8,9]
It works by the concept of eliminating
these artifacts by extracting fail information fromall LADA
events in terms of failing pins/cycles and comparing them
against the actual fail information derived from testing
the bad unit.
[7]
In this way, only the LADA signals relevant
to the actual failure will be displayed. This methodology
also presents an advancement that overcomes LADA’s
traditional limitation on soft failures and creates newpos-
sibilities for hard failure defect localization. The concept
of EeLADA can be realized in a number of ways, and two
such approaches will be discussed.
WHAT IS ELECTRICALLY-ENHANCED
LADA?
Figure 1 shows a block diagram illustrating the EeLADA
concept. In general, although the setup refers to a wafer-
level configuration, it applies to package level as well.
Unlike a typical synchronous LADA setupwhere the tester
generates a trigger in the event of a flip in the test state,
EeLADA integrates an additional comparator module to
determine the trigger pulse generation. The integrated
circuit (IC) device under test is activated by the tester,
which refers to the test pattern for the biasing conditions.
A test pattern is defined by a three-dimensional matrix
of test vectors that correspond to specific pin names and
cycle numbers. The test vectors may represent inputs or
outputs. Inputs serve as driving signals into the IC, and
outputs, also called compare test vectors, provide the
expected states to determine a test pass-fail.
Prior to debug on EeLADA, the bad IC is tested, and
a standard failure log containing details of the compare
fail vectors and the respective fail pin/cycles is obtained.
This is referred to as the reference failure log, as shown
in Fig. 1, and is called the reference failure signature. The
comparatormodule receives this fail log and commits it to
memory. As the tester activates the soft failing IC and the
EDFAAO (2016) 3:10-16
1537-0755/$19.00 ©ASM International
®