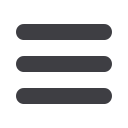
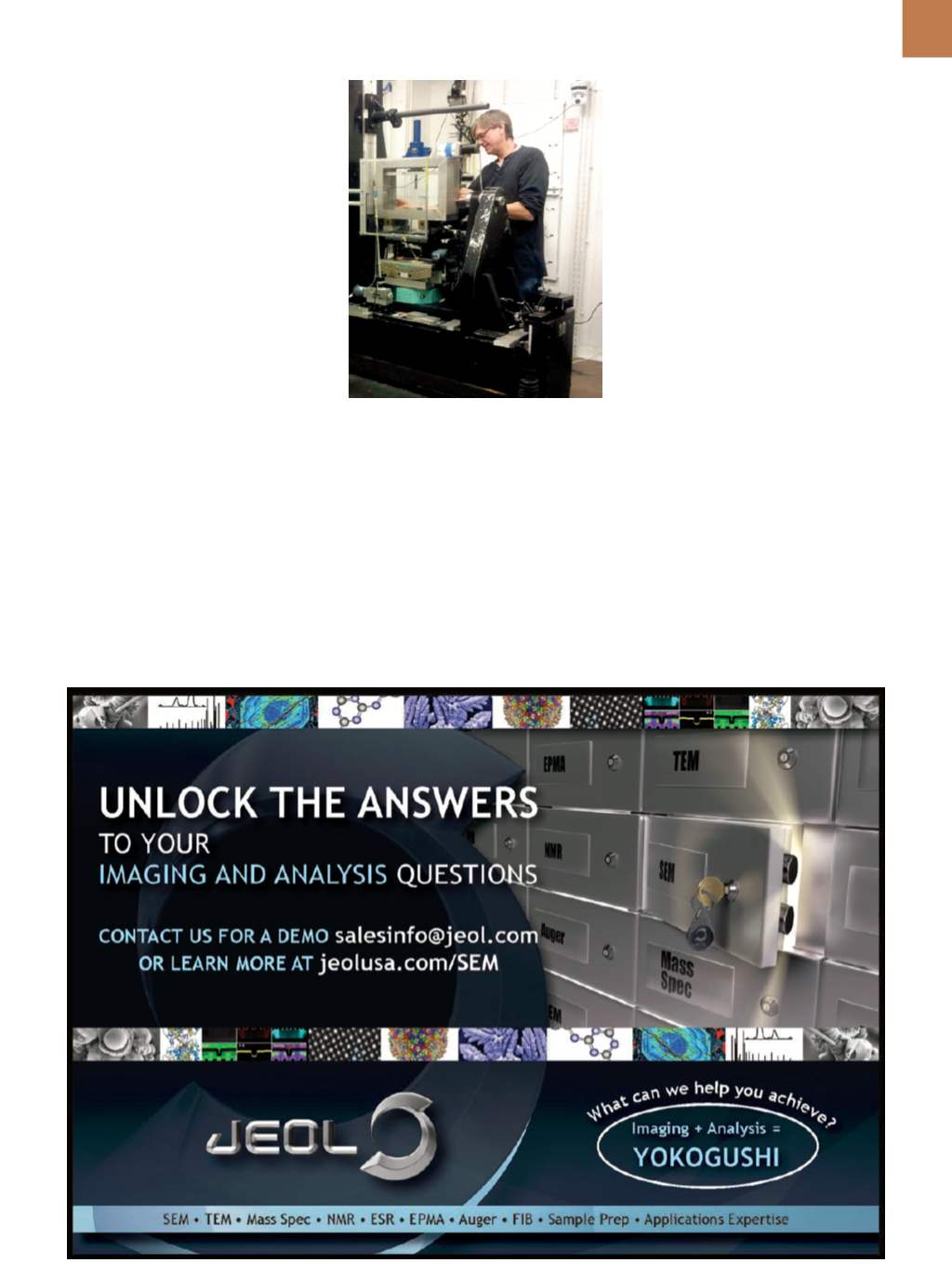
A D V A N C E D
M A T E R I A L S
&
P R O C E S S E S |
M A Y / J U N E
2 0 1 7
2 7
niques get closer to the data that we
need,” says Hector. “Different length
scales calibrate the constitutive models
for plastic flow, transformation kinetics,
and fracture that are ultimately used in
commercial finite element codes for
forming and vehicle performance. We
developed the capability of using the
medium manganese steel and tested
it with vehicle simulations. Accurate
computer representations of 3GAHSS
microstructures are critical for this pro-
cess to work. When further refined, oth-
ers will be able to use the model to do
simulations, build structures, and run
tests.”
~AM&P
For more information:
Susan Bairley
is communications manager for the
United States Council for Automotive
Research LLC, 1000 Town Center, Suite
300, Southfield, MI 48075, 248.223.9023,
sbairley@uscar.org.Acknowledgment
The USAMP 3GAHSS project is managed
in collaboration with A/SP and its mem-
ber companies and was funded in part
by a competitively solicited $6 million
award from the U.S. DOE in 2013.
These predictions, relating stress,
strain, and strain rate, are particularly
valuable because they can be used in
materials forming and vehicle perfor-
mance codes, giving them tremendous
reach. Volume fraction data also infuses
the ICME model with an ability to pre-
dict changes in microstructure arising
from manufacturing forming processes
and in response to structural vehicle
performance.
WEIGHT SAVINGS
As the project teamwinds down its
work, perhaps the crowning prediction
is the estimated weight savings that
can be achieved with the new alloys. To
that end, the team developed a base-
line automotive side structure that sug-
gests the two new 3GAHSS alloys have
significant potential to reduce vehicle
mass without sacrificing performance.
According to Lou Hector Jr., tech-
nical program lead and General Motors
technical fellow, modeling results indi-
cate that the new alloys can achieve a
weight savings in the neighborhood of
20-30% without affecting stiffness or
impact performance. One caveat, how-
ever, is that the team did not address
joining. In the coming months, it in-
tends to focus on validating the 3GAHSS
ICME model through forming trials and
improving model accuracy.
“The ICME process is evolving as
computer hardware gets faster, com-
puter codes get more efficient andmore
comprehensive, and experimental tech-
Fig. 4
– Lou Hector setting up static
measurements in the lab.