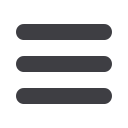
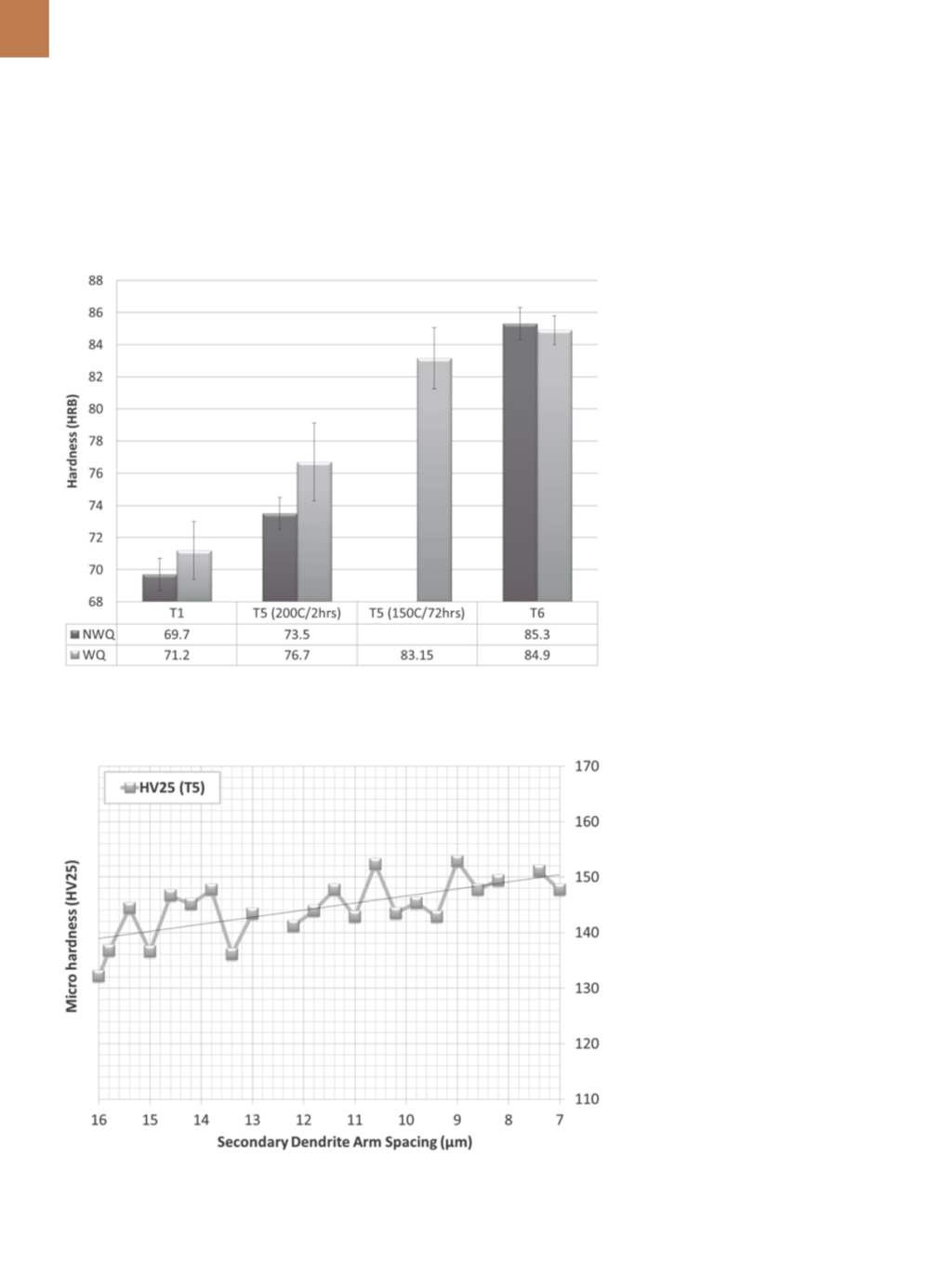
A D V A N C E D M A T E R I A L S & P R O C E S S E S | M A Y / J U N E 2 0 1 7
2 2
this effect. This process requires addi-
tional equipment with a corresponding
higher manufacturing cost. Even with
reduced heat treatment cycle times,
the T6 temper is more costly than the
T5 temper. Advantages of the T5 temper
include reduced capital equipment cost
due to eliminating the solutionizing
treatment. The lower overall cycle time
of the T5 temper (Fig. 5) reduces man-
ufacturing cost while still achieving the
required engine block hardness.
T5 temper optimization
is being
studied to find ways to increase hard-
ness and reduce processing time. Artifi-
cial aging at 150°C for 72 hours, carried
out after casting, de-molding, and wa-
ter quenching, resulted in a maximum
hardness of approximately 83.1
r
1.9
HRB, while aging at 200°C resulted in a
peak hardness of 76
r
2.4 after 2 hours
[1]
(Fig. 6). Such a hardness range allows
some flexibility to reduce temper du-
ration while maintaining the hardness
required to meet the critical tribologi-
cal characteristics of the cylinder bore
surface
[2]
.
Casting solidification rate.
During
HPDC, die cavity liquid metal filling
time is extremely lengthy, but could be
as short as 50-100 ms
[4]
. Consequently,
accurately determining the alloy so-
lidification rate is difficult and impos-
es technical challenges. This is mainly
due to the inability to collect adequate,
unbiased temperature signals, i.e., sig-
nals that represent true thermal event
history coming from the solidifying
melt with minimum thermal inertia im-
posed by the casting die’s large thermal
mass. Direct placement of thermocou-
ples in the HPDC die cavity is not a reli-
able method, and could result in sensor
damage because the cavity is filled with
superheated metal under high veloci-
ties and pressures. The estimated cast-
ing solidification rate could be as high
as ~103°C/s, but the specific value de-
pends on alloy composition, mold/part
geometry, and process parameters
[5]
.
Studies show that the fine micro-
structures (seconary dendrite arm
spacing, or SDAS, between 5 and 30 m)
achieved in HPDC enable a significant
reduction in heat treatment process-
ing time for T6 as well as T5 tempered
parts. A further increase in T5 temper
hardness is possible via microstruc-
ture refinement. Figure 7 shows the
increase in T5 hardness for samples
with smaller SDAS size: 150 HV25 for
7 m compared with 138 HV25 for
16 m.
Casting de-molding temperature.
Casting de-molding is typically carried
out below the solidus temperature to
ensure that the casting is 100% solid
before ejection from the die. Typical-
ly, an exact temperature is not used in
industrial process control because it is
difficult to determine for cooling rates
seen in the permanent mold casting
process. Instead, the time correspond-
ing to the casting de-molding operation
Fig. 6 —
Casting hardness in the T1, T5, and T6 (510°C/0.5h and artificial aging at 200°C/2h)
conditions. The dierences between water quenched (WQ) and non-water quenched (NWQ)
conditions are statistically significant except for the T6 temper
[1]
.
Fig. 7 —
Increase in microindentation hardness (HV25) as a result of microstructure refinement
for SDAS from 16 to 7 ¦m for the test casting T5 tempered at 150°C for 48 h. These data indicate
that more refined structures oer higher hardness aer tempering
> @
.