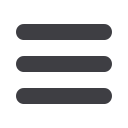
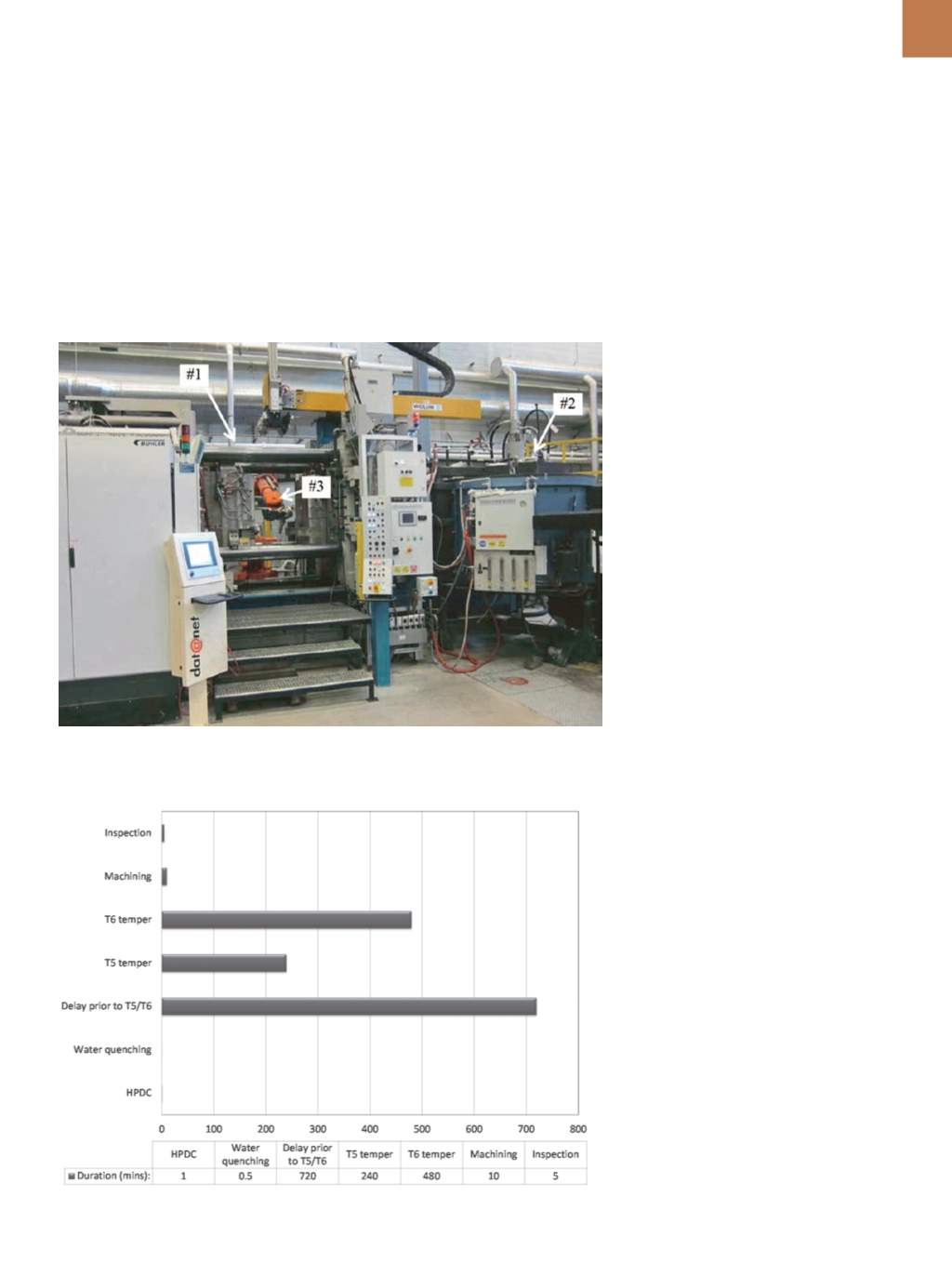
A D V A N C E D
M A T E R I A L S
&
P R O C E S S E S |
M A Y / J U N E
2 0 1 7
1 9
cavity using a robotic system and fol-
lowed by an automated water quench-
ing operation. The casting is then ready
for post-processing operations includ-
ingT5andT6 tempers. Temper selection
depends on component requirements
and economic considerations. Machin-
ing operations for near-net-shape HPDC
parts are typically performed after heat
treatment and require the casting to be
dimensionally stable
[2]
. Figure 5 shows
production process steps.
Hardness is a key quality accep-
tance criterion for engine blocks be-
cause it relates to the cylinder’s tri-
bological characteristics. Therefore,
in the case of a DiASil cylinder block
(Fig. 1b), the targeted hardness of
!
73
HRB is used as an indicator of heat
treatment effectiveness. Heat treament
is the most time consuming production
step and therefore the most cost-inten-
sive operation (Fig. 5). Thus, there is a
need to shorten heat treatment time
without compromising hardness, re-
ducing overall manufacturing time and
reducing costs. This represents an op-
portunity for cost savings.
OPTIMIZING PROCESS
PARAMETERS
The overall production cycle (i.e.,
from casting through heat treatment)
rather than individual operations must
be considered to effectively maximize
hardness and reduce processing time
[1]
.
Process variables that are not typical-
ly optimized or controlled in industrial
practice have measurable individual
effects, potentially offering additional
benefits on their superimposed effect
[1]
.
Using T5 instead of T6 temper.
The
short T6 temper consisting of solution-
izing, quenching, and aging is used for
engine block applications to improve
mechanical properties and casting ho-
mogeneity. The duration of the solution
treatment in existing heat treatment
standards is often longer than that re-
quired to achieve the desired level of
microstructure refinement. For the
castings in this study, proper optimi-
zation of the T6 solution treatment re-
quired only 30 minutes at 510°C, which
resulted in similar or higher hardness
than was achieved by solutionizing at
490°C for 4 hours
[3]
. Hardness of up to
85 HRB was achieved for T6 tempered
conditions (Fig. 6), with an overall pro-
cess duration of approximately 480
minutes (Fig. 5). A more refined micro-
structure achieved during HPDC pro-
cessing yields higher hardness of the
D
-Al metal matrix.
Castings can experience blistering
during the solutionizing treatment. Blis-
tering is a casting defect caused by an
increase in gas pressure in subsurface
porosity during solutionzing. Increased
pressure results in deformation of the
thin metal layer surrounding the pore
close to the casting surface. A vacuum
process is used to reduce gas content in
the die cavity during the HPDC opera-
tion to avoid blistering during T6 solu-
tionizing. The resulting gas level in the
finished casting is approximately 5 cm
3
/
100 g. Application of vacuum in the
range of approximately 1 to 30 mbar
measured in the die cavity eliminates
Fig. 4 —
CanmetMaterials 1200-ton high pressure die casting system used for R&D studies:
(1) clamp area with die; (2) furnace with automatedmelt transfer system; and (3) robot for parts
extraction. Courtesy of CanmetMaterials.
Fig. 5 —
Duration (minutes) of manufacturing operations for a motorcycle cylinder block.