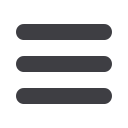
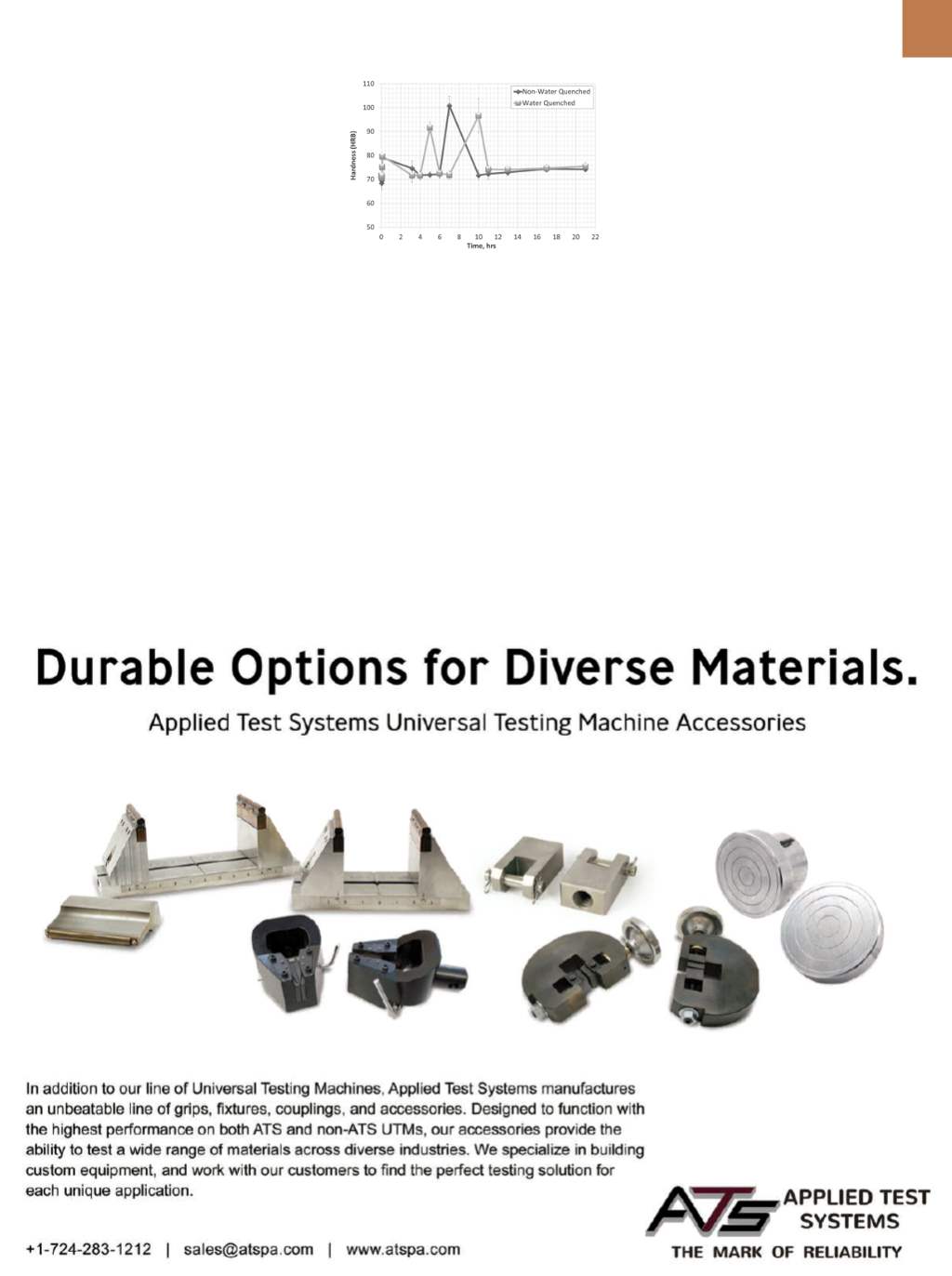
A D V A N C E D
M A T E R I A L S
&
P R O C E S S E S |
M A Y / J U N E
2 0 1 7
2 3
is preferred because it can be easily
controlled using programmed cycles of
the casting machine. Generally, a DiASil
cylinder block is de-molded at about
380°C, which is approximately 100°C
below the alloy solidus temperature
(end of the solidification process). This
de-molding temperature is high enough
to bring about the microstructural and
related mechanical properties chang-
es needed when the casting is subse-
quently quenched in water. Increasing
the de-molding temperature enhances
the casting response to the aging pro-
cess upon water quenching, but could
create the risk of ejecting the casting
from the mold when it is not completely
solid.
Water quenching after de-molding
is typically used to cool castings for eas-
ier handling prior to the next manufac-
turing step, which could include heat
treatment, machining, and inspection.
Subsequent operations are sometimes
carried out in a separate facility requir-
ing transportation of castings. Besides
water, quenching oils, emulsions, and
compressed air can be used to cool the
casting. Choosing the best cooling me-
dium depends on overall process re-
quirements including casting geometry,
residual stress considerations, and sub-
sequent processing steps. Quenching
can also be used to retain some degree
of solid solution resulting fromnonequi-
librium solidification, to prevent the dif-
fusion of alloying elements. This super-
saturated solid solution improves the
precipitation process through artificial
aging. Increasing the quenching rate
and avoiding quenching delays enhanc-
es the aging response. Average casting
quenching cooling rate inwater is about
40°C/s, and is sufficient to observe an
improvement in casting hardness
[1]
. Fig-
ure 6 shows the effect of water quench-
ing on test casting coupon hardness
for various temper conditions; hard-
ness is increased by an average of up to
5% for water quenched castings.
Effect of time delay between cast-
ing and tempering operations.
The time
a casting is held at room temperature
prior to heat treatment depends on the
specific manufacturing cycle. For ex-
ample, heat treatment done in-house
as a continuous operation enables pre-
cise definition of cycles. For castings
heat treated at a different facility, the
duration of holding castings at room
Fig. 8 —
Variation in macrohardness for the
test casting in the T1 as-cast condition as
a function of natural aging time (days), i.e.,
delay between the completion of casting
process and beginning of T5 temper for
non-water quenched aer casting de-mold-
ing and water quenched aer casting
de-molding
[1]
.