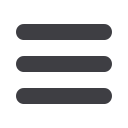
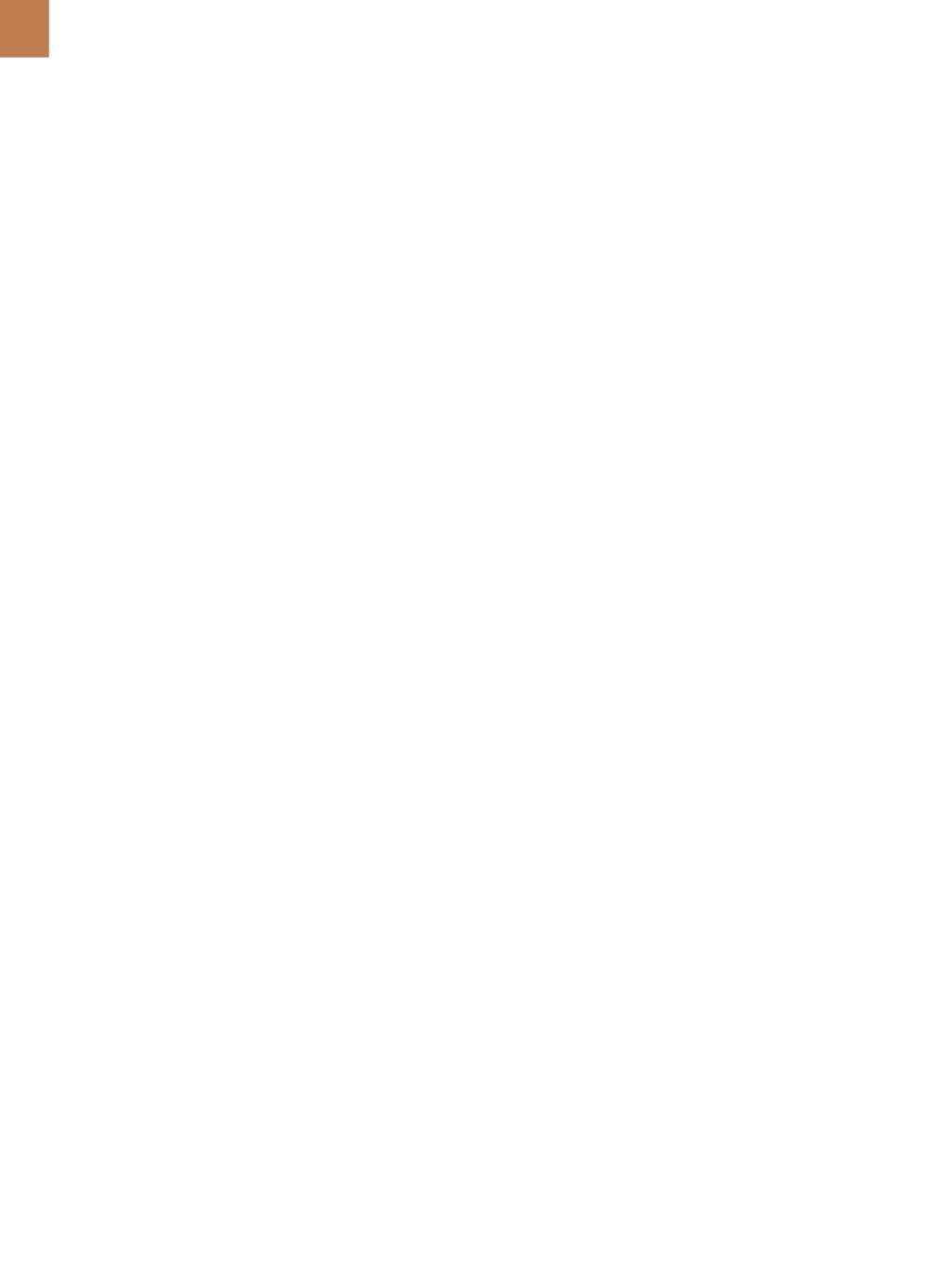
A D V A N C E D M A T E R I A L S & P R O C E S S E S | M A Y / J U N E 2 0 1 7
2 8
A
rcheological investigations into
the origins of glassmaking have
been aided in recent years by a
flood of new information obtained from
scanning electron microscopes and
x-ray spectrometers. These indispens-
able tools have helped researchers re-
solve conflicts and ambiguities that
had persisted for decades by revealing
new details in the microstructure and
chemical composition of ancient glass
items, some dating back to 4000 B.C.
[1]
In much the same way, advanced im-
aging and spectrographic technology
is proving to be a valuable asset in the
production of cell phone cover glass,
which is as critical to the world’s future
as ancient glass artifacts are to the past.
COVER STORY
Cell phone cover glass plays an
important role in the lives of more than
six billion people. It also supports the
booming smartphone industry and
contributes in many ways to today’s
economy. Each year, specialty glass-
makers produce and ship more than
one billion cell phone covers, pushing
the limits of materials science, man-
ufacturing methods, and inspection
techniques as they strive to make their
products stronger, lighter, sleeker, and
more resilient—without raising prices.
Cover glass, like most cell phone
components, is a highly engineered
VISUALIZING CELL PHONE
COVER GLASS USING
ADVANCED TESTING
TECHNIQUES
Scanning electron microscopy and energy dispersive x-ray spectroscopy
open new windows into glassmaking processes.
John Konopka,* Thermo Fisher Scientific, Madison, Wis.
*Member of ASM International
product manufactured to exacting
specifications. It consists of a high pu-
rity glass substrate topped with mul-
tiple surface enhancing layers. The
substrates are chemically strengthened
by placing them in a bath of molten salt,
causing large ions from the solution to
switch places with smaller ions on the
glass surface. Once the glass cools and
the lattice structure contracts, the larg-
er ions create a state of compression
that has a strengthening effect on the
host material. Several layers of proper-
ty altering materials are then deposited
on the treated substrates, making the
final product more resistant to scratch-
es, reflections, and other hazards in-
cluding microbial growth.
To determine if the various man-
ufacturing steps went according to
plan—or to investigate suspected ab-
normalities—glassmakers
frequently
employ a combination of scanning elec-
tron microscopy (SEM) and energy dis-
persive x-ray spectroscopy (EDS). When
used together, these analytical tools
make it possible to visualize materials
down to the nanometer level and evalu-
ate chemical composition towithin tens
of nanometers. Such precision is essen-
tial for optimizing today’s glassmaking
processes and for identifying inclusions
and other defects that may hold clues
in cases where cover glass fails.
E-BEAMS AND X-RAYS
Scanning electron microscopy, as
its name implies, works by scanning
an electron beam over a target area.
As the beam sweeps over the test sam-
ple, scattered electrons are collected
at equidistant points on an imaginary
grid and the resulting signal is convert-
ed to a high-resolution image. Incident
electrons from the beam can also excite
atoms along the beam path, causing
them to emit x-rays that contain atom-
ic information. X-ray emission energies
correlate to atomic structure and are
unique to each element. Scanning elec-
tron microscopes equipped to measure
this dispersive energy can thus reveal
the chemical composition of test sam-
ples as well.
Solid-state detectors for ener-
gy dispersive x-ray spectroscopy have
been available for nearly 50 years. The
earliest versions, which appeared in the
late 1960s, are based on a silicon-lithi-
um sensing mechanism that converts
photon energy, through quantum col-
lisions, to free electron charge. Si(Li)
detectors excel at high-energy wave-
lengths, but they require liquid nitro-
gen cooling to suppress leakage current
that would otherwise interfere with
measurements.
Roughly 20 years after the debut
of the first solid-state x-ray detectors,