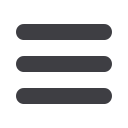
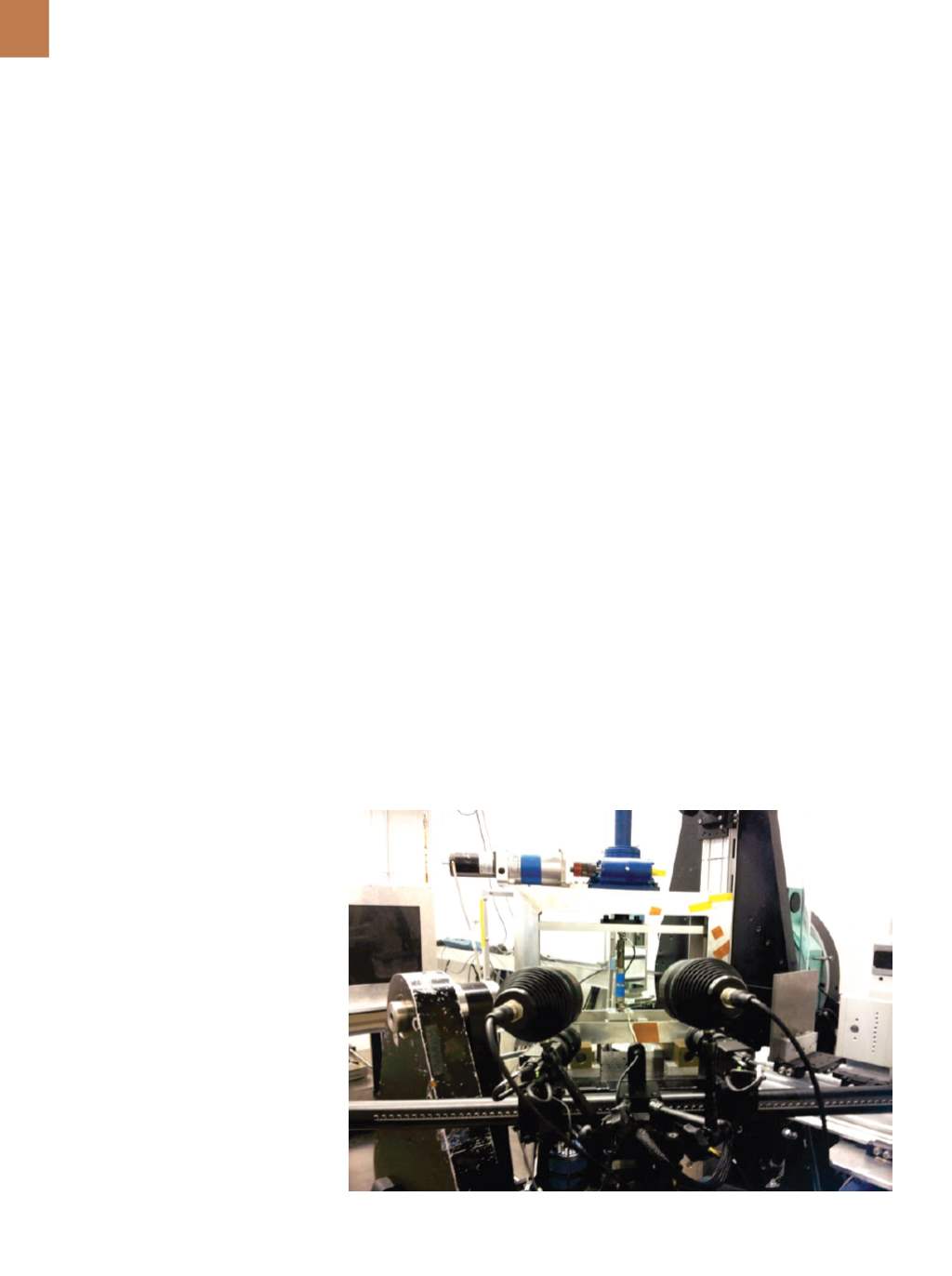
A D V A N C E D M A T E R I A L S & P R O C E S S E S | M A Y / J U N E 2 0 1 7
2 6
this has made modeling a challenge be-
cause the material phase composition
and resulting mechanical properties
change when being formed into com-
ponents or during vehicle impact.
To effectively model the behav-
ior of 3GAHSS alloys, the project team
developed a new lab procedure for
dynamically measuring retained aus-
tenite volume fraction as a function
of strain path and deformation mode,
e.g., tension, bending, or plane strain.
Test setup is shown in Fig. 3. The new
procedure, essentially an optical strain
measurement, employs high energy
synchrotron x-ray diffraction coupled
with digital image correlation. It offers
an unprecedented view of the materi-
als science behind the austenite trans-
formation and the extent to which it
impacts strength and ductility using
a test sample that closely simulates
stamped automotive components. The
USAMP team engaged with scientists at
Argonne National Laboratory who used
their Advanced Photon Source—one of
the most powerful materials science di-
agnostic tools in the world—to acquire
critical data for the volume fraction
measurement.
USAMP’s ICMEmodel derivesmuch
of its predictive power from this infor-
mation. The model’s ability to make
forming predictions is one example.
from which experimental data were
generated and then used to calibrate
and validate length-scale models.
These models were subsequently in-
tegrated into larger scale constitutive
models developed to optimize forming
operations and improve performance
codes related to plasticity and fracture
behavior. Second, it investigated mi-
crostructural processes at length scales
that could be simulated to provide in-
formation for higher order models, thus
reducing the amount of experimenta-
tion required. Third, it tested predic-
tions from ICME models with a specially
designed T-shaped component which,
by virtue of its shape, subjects sample
materials to a variety of strain paths
and deformation modes.
Last but not least, the team es-
tablished a data model for archiving
and curating project data so others can
tap into it to accelerate future work us-
ing computational techniques. Reuse
of data is imperative for achieving the
goals of the MGI and serves as a bridge
between the known and unknown,
where tomorrow’s innovations lie. Such
innovations require a well-developed
data model because new steels are of-
ten synthesized by combining constitu-
ents and phases from existing steels.
TEAMWORK
Making data available for reuse
also helps facilitate the MGI spirit of col-
laboration, without which the 3GAHSS
project would not have succeeded. In
fact, the project followed some of the
basic tenets of “collaboration science,”
a separate area of study that has gained
prominence in recent years. Collabo-
ration science focuses on how to get
people from diverse technical back-
grounds—with different performance
metrics—to work together in such a way
that they freely share data prior to pub-
lication. Most of the collaborators in
the 3GAHSS project did not know each
other before the project began. This re-
quired the project management team
to establish a high level of trust among
participants early on.
AK Steel, one of the key contrib-
utors to the 3GAHSS work, was rep-
resented by some of its most skilled
collaborators, members of its research
and innovation team. This group
worked closely with the Colorado
School of Mines and other team mem-
bers to design and produce prototype
alloys made in AK Steel’s research lab
in Middletown, Ohio. The USAMP proj-
ect team also worked closely with AK
Steel’s application lab in Dearborn,
Mich., co-designing a unique stamping
die and using it to make T-shaped test
samples, representative of a critical
section of an automotive body B-pillar,
in order to demonstrate the potential of
experimental alloys.
Beyond meeting or exceeding
DOE targets, the collaboratively de-
veloped alloys were instrumental in
the development and calibration of a
functional 3GAHSS ICME model incor-
porating material and forming details.
The team worked with several DOE labs
to produce, test, and characterize the
alloys for this portion of the research.
And with DOE’s help, it developed 3D
representative volume elements of the
microstructures, a critical component
in the ICME models.
CRITICAL MEASUREMENT
Third-generation advanced high-
strength steel alloys are complex mul-
tiphase materials with a metastable
phase (austenite) that transforms to
martensite when deformed. In the past,
Fig. 3
– Dynamic setup for USAMP experiments at Argonne National Lab.