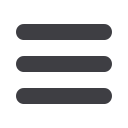
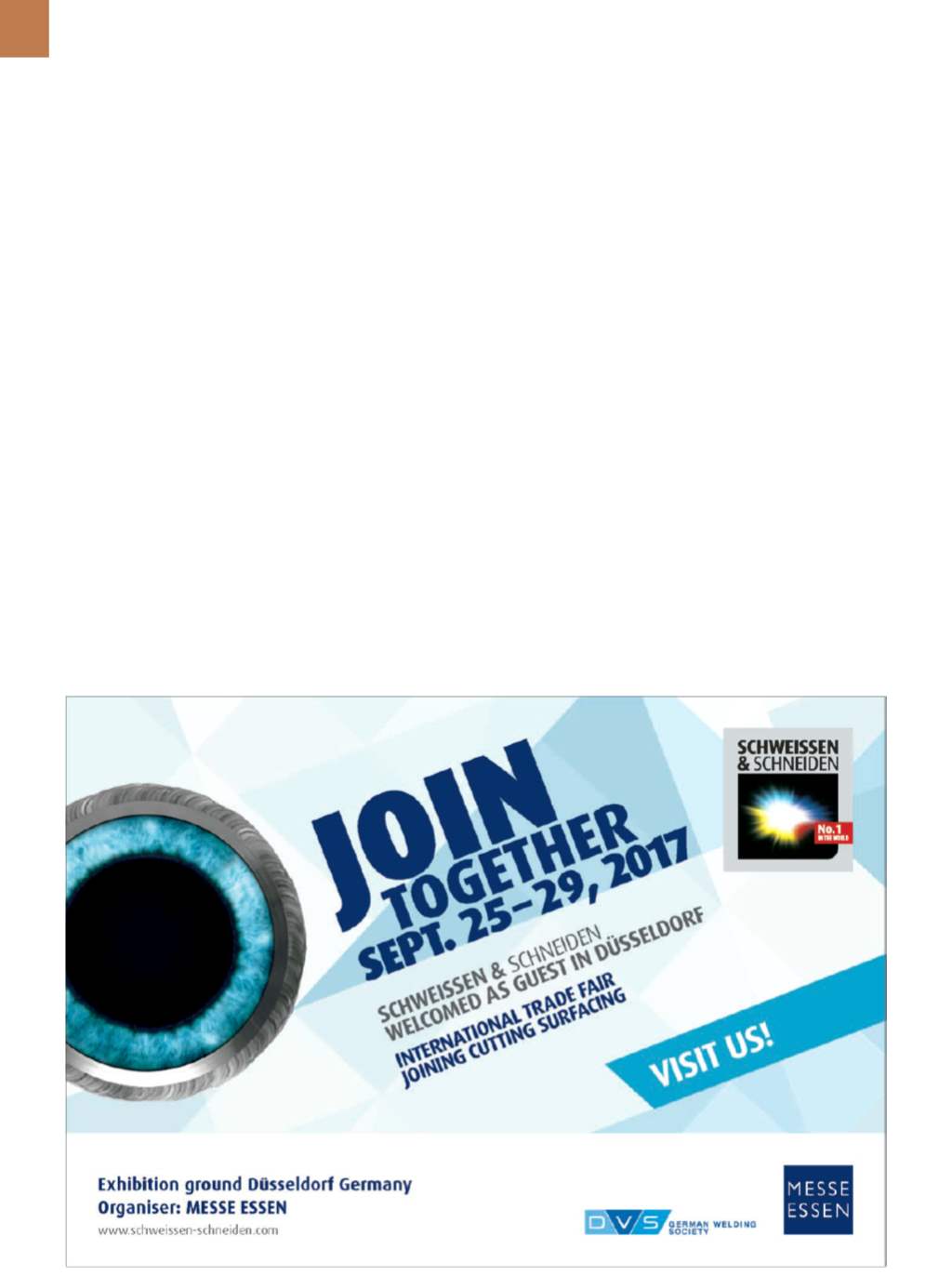
A D V A N C E D M A T E R I A L S & P R O C E S S E S | M A Y / J U N E 2 0 1 7
2 4
temperature can vary
[1]
. This could re-
sult in castings having different initial
hardness prior to the beginning of heat
treatment. Studies show that cast-
ing hardness varies depending on the
length of time at room temperature af-
ter completion of the casting process.
Figure 8 shows hardness values for
water and non-water quenched condi-
tions. Based on these data, the recom-
mended approach is to allow casting
hardness to return to its approximate
initial values; i.e., hold for 11 days
(keeping in mind that the fully stable
condition could take years to occur), or
move to another operation before cast-
ing hardness increases as a result of
natural aging. As shown in Fig. 8, hard-
ness of non-water quenched castings
increases after approximately six days,
and after four days for water-quenched
castings
[1]
.
SUMMARY
Researchers at CanmetMaterials
are exploring ways to maximize HPDC
mechanical properties while reducing
manufacturing time for automotive
powertrain components. Results show
that it is possible to increase hardness
of hypereutectic Al-Si alloys by optimiz-
ing the water quenching rate and du-
ration of room temperature hold, and
producing castings with finer micro-
structures. For the alloy in this study,
hardness can be increased up to 10%,
but detailed optimization studies are
required for specific casting part geom-
etry and alloy chemical composition.
For the engine block application, higher
hardness together with primary Si mor-
phology ensure that the required tri-
bological characteristics of the engine
bore surface
[1]
are achieved.
~AM&P
Formore information:
WojciechKaspr-
zak is director of operations, Canmet-
Materials,183LongwoodRd.South,Ham-
ilton, Ontario, L8P 0A5, 905.645.0697,
wojciech.kasprzak@canada.ca, www.canmetmaterials.nrcan.gc.ca.
*DiASil is a trademark of
Yamaha Motor
Co. Ltd.,
Shizuoka, Japan.
Acknowledgment
Research was conducted as part of a
contract carried out under the Materi-
als for Energy End Use in Transportation
Program of Natural Resources Canada.
The authors thank Gabriel Birsan, M.Sc.,
P.Eng., and Babak Shalchi Amirkhiz of
CanmetMaterials for experimental and
metallurgical analysis support.
References
1. W. Kasprzak, et al., Hardness Control
of Al-Si HPDC Casting Alloy via Micro-
structure Refinement and Tempering
Parameters,
Matls. & Design
, Vol 103,
p 365-376, 2016.
2. H. Yamagata,
The Science and
Technology of Materials in Automotive
Engines
, Cambridge: Woodhead Pub-
lishing, 2005.
3. W. Kasprzak, et al., Energy Efficient
Tempers for Aluminum Motorcycle
Cylinder Blocks,
Adv. Matls. & Proc.,
p 24-27, March 2010.
4. F. Bonollo, N. Gramegna, and
G. Timelli, High-Pressure Die-Casting:
Contradictions and Challenges,
JOM
,
Vol 67, No. 5, p 901-908, 2015.
5. H. Yamagata, et al., The Effect of Av-
erage Cooling Rates on the Microstruc-
ture of the Al-20% Si High Pressure
Die Casting Alloy used for Monolithic
Cylinder Blocks,
J. Matls. Proc. Tech.
,
Vol 203, No. 1-3, p 333-341, 2008.