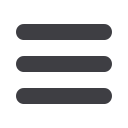
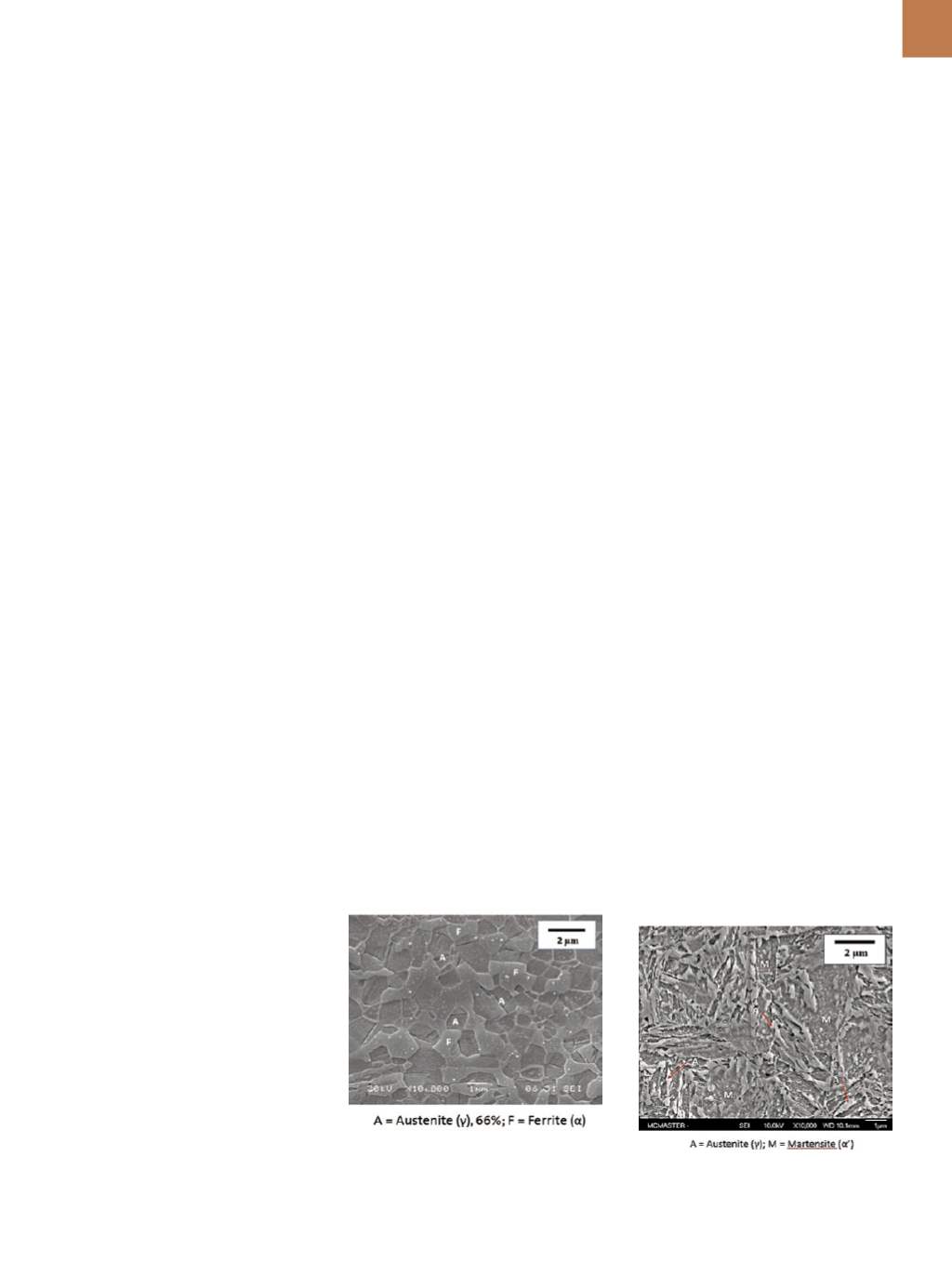
A D V A N C E D
M A T E R I A L S
&
P R O C E S S E S |
M A Y / J U N E
2 0 1 7
2 5
T
he U.S. Automotive Materials
Partnership (USAMP), an indus-
try alliance representing Chrysler,
General Motors, and Ford, has long
been immersed in the collaborative
development of lightweight metals for
manufacturing cars and trucks. Now,
the Southfield, Michigan-based orga-
nization is about to release the results
of one of its most ambitious efforts yet,
the development and validation of an
integrated computational materials en-
gineering (ICME) model optimized for
third-generation advanced high-strength
steels (3GAHSS). These high-tech mate-
rials have the potential to make vehicles
lighter, safer, and more fuel efficient and
reduce wear and tear on bridges and
highways as well, but design and manu-
facturing complexities stand in the way.
USAMP, a wholly owned subsidi-
ary of the U.S. Council for Automotive
Research (USCAR), has been working
on the 3GAHSS project since 2013 with
help from Pacific Northwest Nation-
al Laboratory, Brown University, The
Ohio State University, the University
of Illinois, Colorado School of Mines,
Clemson University, AK Steel, Argonne
National Laboratory, and the Auto/
Steel Partnership (A/SP). So far, the
project team has developed two new
high-performance alloys and has suc-
cessfully scaled up its steelmaking
AUTOMOTIVE INDUSTRY
PARTNERSHIP PAVES THE
WAY FOR ADVANCED
HIGH-STRENGTH STEELS
Scientists and engineers working on behalf of the U.S. automotive industry are
nearing completion of a multiyear e ort to accelerate the incorporation of advanced
high-strength steels in American-made cars and trucks.
process from small heats made in
the lab to large heats produced using
factory-style equipment. Due to the
scale-up, the team now has sufficient
quantities of both new alloys to support
extensive testing and continued efforts
to calibrate and validate models.
Based on initial tests, one of the
new alloys, a medium manganese
(10 wt%) steel, has an ultimate tensile
strength of 1200 MPa with 37% ten-
sile elongation. These marks exceed
DOE targets for
high-strength, excep-
tional-ductility
steel. The other alloy,
a 3% manganese steel, has a tensile
strength of 1538 MPa with 19% elonga-
tion, proving to be stronger but slightly
less ductile than what DOE classifies
as
exceptional-strength, high-ductility
steel. Microstructures of both alloys are
shown in Figs. 1 and 2.
MATERIALS GENOME
INITIATIVE
ICME and the methodology behind
it closely align with the vision of the
U.S. Materials Genome Initiative (MGI),
which seeks to accelerate the discovery
and application of new materials by
seamlessly integrating theory, experi-
ment, and data models. In the course of
its work, the USAMP team set and com-
pleted several objectives on common
ground with the goals of the MGI.
First, it brought relevant stake-
holders together to develop new alloys
TECHNICAL SPOTLIGHT
Fig. 1
– High-elongation 3GAHSS sample;
mediummanganese (10 wt%) transforma-
tion induced plasticity (TRIP) steel. Courtesy
of Matt Enloe and McMaster University.
Fig. 2
– Strong and ductile 3GAHSS alloy
sample (QP1500). Courtesy of Matt Enloe
and McMaster University.