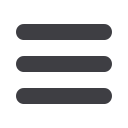
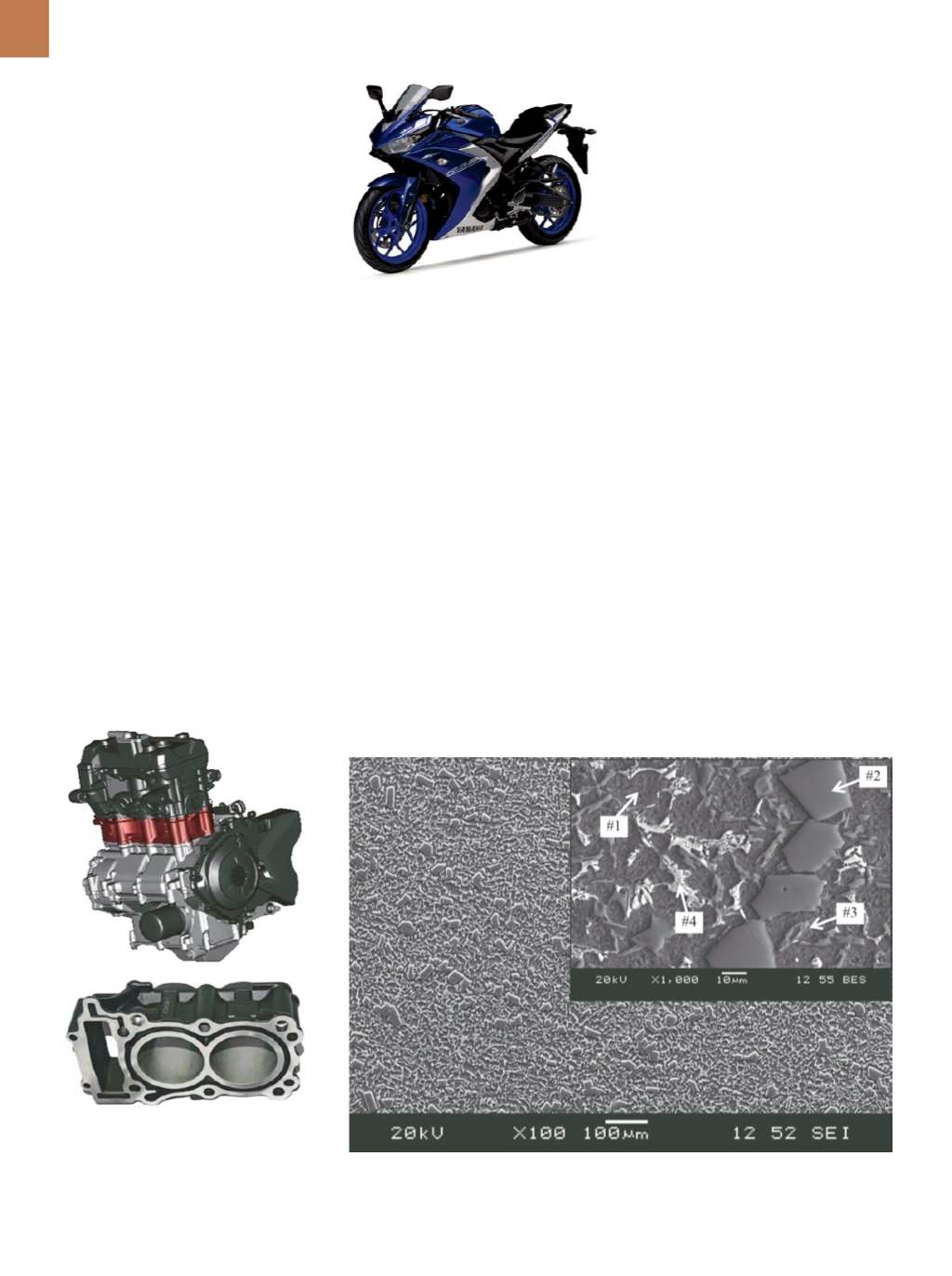
A D V A N C E D M A T E R I A L S & P R O C E S S E S | M A Y / J U N E 2 0 1 7
1 8
Fig. 1 —
Water-cooled 250 cm
3
motorcycle
cylinder block made of hypereutectic Al-Si
alloy (DiASil) using the HPDC process: (a) as-
sembled engine overview; (b) engine block
casting. Courtesy of Yamaha Motor Co.
L
ightweight Al-Si base alloys are key
engineering materials for use in cast
automotive powertrain appli-
cations due to their combination of
structural and service characteristics.
Specifically, hypereutectic Al-Si alloys
containing >12 wt% Si are materials of
choice for use in applications such as
engine blocks
[1]
. A monolithic (linerless)
engine block design is cost effective
because it eliminates the need to use
press-fit or cast-in cylinder sleeves (het-
erogeneous design), or Cr-Ni base coat-
ing (quasimonolithic design) in which
thermal spray is deposited on the bore
surface
[2]
. The monolithic design is used
in small one-cylinder motorcycles
[3]
,
and more recently for manufactur-
ing two-cylinder, water-cooled engine
blocks (Fig. 1). Such engines meet size
and performance specifications and are
used in mid-size motorcycles yielding
36 hp @ 12,000 rpm from 250 cm
3
dis-
placement (Fig. 2).
Monolithic engine blocks made
of DiASil* (die cast aluminum silicon)
hypereutectic Al-Si alloy (Al, 17%Si,
4.5%Cu, and 0.5%Mg) meet modern
engine requirements including cooling
performance, light weight and com-
pact design, and low manufacturing
cost. Alloy wear resistance and thermal
conductivity are the main factors affect-
ing oil consumption and engine cool-
ing characteristics. Oil consumption
for monolithic blocks measured on a
10,000-km running test at approximate-
ly 7000-9000 rpm is improved by up to
50% compared with that for heteroge-
neous blocks.
The alloy’s tribological properties
are mainly controlled by the primary Si
size, distribution, exposure height from
the aluminum matrix, and overall alloy
hardness
[1]
. Figure 3 shows the repre-
sentative microstructure of an etched
material sample, which removed a rel-
atively soft
D
-Al matrix and resulted in
exposed primary Si, Al-Si eutectic, and
Cu-Mg base phases. The etched surface
closely represents an actual cylinder
bore following honing. After honing,
the primary Si crystals are exposed as
high as 0.5 m. Removal of the metal
matrix exposing primary Si crystals pro-
motes elastohydrodynamic lubrication
(EHL), which is required to withstand
the reciprocal movement of the engine
piston
[2]
.
A monolithic block can be pro-
duced by various techniques includ-
ing sand casting, lost foam, and the
semipermanent process. High pres-
sure die casting (HPDC) offers high
production rates and satisfactory qual-
ity at a competitive price. An HPDC
system used for R&D studies at Can-
metMaterials laboratory is shown in
Fig. 4. In the HPDC process, liquid met-
al is transferred into a shot sleeve from
a holding furnace and injected into the
water-cooled die where it rapidly so-
lidifies under hydraulic pressure. The
actual pressure depends on specific
equipment configurations and could be
as high as 120 MPa, with a melt flow ve-
locity between 30 and 60 m/s (100 and
200 km/h) at the gates
[4]
. When the met-
al temperature drops below the soli-
dus, the casting is ejected from the die
Fig. 2 —
Mid-size motorcycle powered by a
lightweight 250 cm
3
water-cooled two-cylin-
der engine. Courtesy of Yamaha Motor Co.
Fig. 3 —
Hypereutectic Al-Si alloy (DiASil) microstructure aer chemical etching. Inset, because
the
D
-Al matrix (1) was removed, this resulted in exposure of primary Si (2), Al-Si eutectic (3), and
Cu/Mg base phases (4).
a)
b)