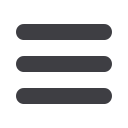

A D V A N C E D
M A T E R I A L S
&
P R O C E S S E S |
M A Y / J U N E
2 0 1 7
1 3
UNDERWATER ADHESIVE
FLEXES ITS MUSSELS
Researchers at Purdue Univer-
sity, West Lafayette, Ind., developed
a polymer adhesive for wet bonding
that could be one of the strongest of
its kind to date. The biomimetic glue,
called poly(catechol-styrene), borrows
the chemistry of the adhesive mussels
use to cling to objects underwater. After
investigating which aspects of mussel
adhesion are most important in a wet
and salty environment, researchers de-
termined that the only critical element
is a catechol-containing polymer. Cat-
echols are a component of the amino
acid DOPA, which is contained in mus-
sel adhesive proteins. According to the
team, catechols appear to “drill down”
through water to bind onto surfaces
themselves, instead of interacting with
water as most adhesives do.
In a series of bond tests conduct-
ed in tanks of artificial seawater, the
bio-based glue performed better than
10 commercial adhesives when used to
bond polished aluminum. Compared
to the five strongest commercial glues
included in the study, the new adhe-
sive performed better when bonding
wood, Teflon, and polished aluminum.
In fact, it was the only adhesive tested
that worked with wood and it far out-
performed the other adhesives when
used to join Teflon. Future research will
test the adhesive under real-world con-
ditions.
purdue.edu.
MASS-PRODUCED GRAPHENE
STARTS WITH A BANG
Physicists from Kansas State Uni-
versity (K-State), Manhattan, acciden-
tally invented a safe, simple, and afford-
able method to mass-produce graph-
ene: Fill a chamber with acetylene or
ethylene gas and oxygen, create a con-
tained detonation with a vehicle spark
plug, and collect the graphene that
forms. The serendipitous discovery
occurred while the team was devel-
oping carbon soot aerosol gels. When
they created a detonation in an alumi-
num chamber filled with acetylene gas
and oxygen, the aerosol gels formed
by the resulting soot turned out to be
graphene. The new process has since
been patented.
Other methods of creating gra-
phene are low yield, energy intensive,
and even dangerous, involving the
lengthy “cooking” of graphite with
chemicals—such as sulfuric acid, sodi-
um nitrate, potassium permanganate,
or hydrazine—or the heating of hydro-
carbons to 1000°C in the presence of
catalysts. The new process produces
graphene by the gram, rather than mil-
ligram, and energy consumption is min-
imal. One gram of graphene can be pro-
duced using only the energy required to
ignite a single spark.
k-state.edu.
HTS International
and the DOE’s
Oak Ridge National Laboratory,
both in
Tennessee, signed a memorandum of understanding to explore collabora-
tions in advanced manufacturing research. HTS is a supplier to the injec-
tion molding and die casting industries, using its metal fusion technology
to make steel production components with conformal cooling.
htsintl.com , ornl.gov.PROCESS TECHNOLOGY
From le , K-State researchers Justin
Wright, Chris Sorensen, and Arjun Nepal,
with a container of graphene. Sorensen
and Nepal patented a method to create
graphene through a controlled detonation.
These coolant lines allow parts to cool faster,
boosting productivity for molding and casting
manufacturers. Courtesy of ORNL.
BRIEF
Le, a mussel uses its natural adhesive to stick to aluminum. Right, two pieces of
aluminum are bonded using the polymer modeled aer the animal’s adhesive.
Chemical structures of the mussel protein and synthetic polymer are shown.