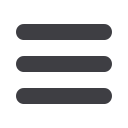
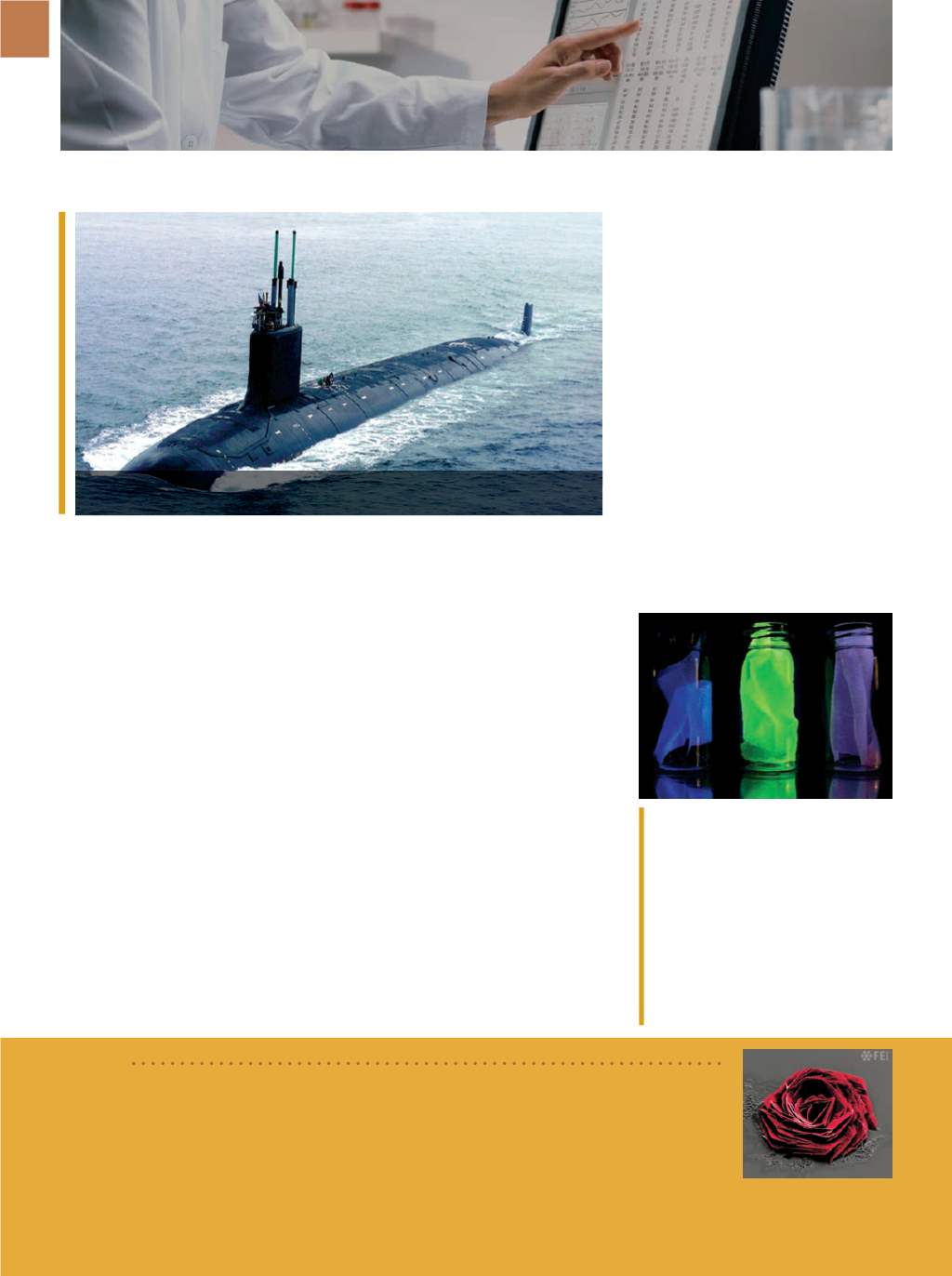
A D V A N C E D M A T E R I A L S & P R O C E S S E S | M A Y / J U N E 2 0 1 7
1 0
was attached to silk fibers contained
in an epoxy-based composite. When
force was applied to the composite, the
RS was activated, and a red laser and
microscope were used to take images
of the miniscule fissures revealed in
the glowing fibers. Conventional opti-
cal imaging techniques, which cannot
record images smaller than 200-400 nm,
are incapable of capturing fiber-poly-
mer interfaces, some of which are only
10-100 nm thick.
The sensors could be used to
speed up product testing and optimize
composites for different applications,
according to researcher Jeffrey Gilman.
“If you attempt a design change, you
can figure out if the change you made
CHEERS TO NEW WELD
INSPECTION METHOD
Lawrence
Livermore
National
Laboratory (LLNL), Calif., and the U.S.
Navy Metalworking Center, Johnstown,
Pa., are investigating a nondestructive
method to inspect welds on nucle-
ar-powered submarines. The technol-
ogy uses acoustical structural excitation
along with ultra-wide-band radar tech-
nology to “hear” defects through the
submarine’s coating. LLNL materials
and engineering section leader Karl
Fisher equates the method to tapping
wine glasses—an intact glass will “ding”
while a cracked glass only plunks. “In
theory, the defect will radiate differ-
ently and have a different mechanical
response, and we could scan it and
find out where,” he explains. The tech-
nology has been used to locate impro-
vised explosive devices underground,
and while it isn’t guaranteed to work on
TESTING | CHARACTERIZATION
The grand prize winner of the 2016
Thermo Fisher Scientific
Electron Microscopy image con-
test is Andrea Jacassi from the
Italian Institute of Technology
for “Cysteine Rose.” The image
was captured using the Helios NanoLab 650 DualBeam focused ion beam/scanning electron
microscope, produced by
FEI,
Hillsboro, Ore., a recent acquisition of Thermo Fisher, Waltham,
Mass. thermofisher.com.submarines, it could help narrow down
the search area for weld defects. Cur-
rently, hull inspections require removal
and reinstallation of the submarine
coating. Reducing the need for this
process could shrink costs by as much
as $1.2 million per hull per inspection
cycle, or $6 million over a five-year
period.
llnl.gov.
SHEDDING LIGHT ON
COMPOSITE INTERFACES
Researchers at the National In-
stitute of Standards and Technology
(NIST), Gaithersburg, Md., embedded a
nanoscale probe into lightweight fiber-
reinforced polymer composite, exposing
damage at the interfaces between the
fiber and polymer—reportedly for the
first time. The probe, known as a mech-
anophore, was created from rhodamine
spirolactam (RS), a dye that fluoresces
under applied force. The RS molecule
Examples of the silk used in experiments
to detect damage in composites, shown
under black light. Le , ordinary fibroin
of the
Bombyx mori
silk worm. Observed
fluorescence is the result of molecules al-
ready present in the fiber’s protein struc-
ture. Middle, mechanophore-labeled silk
fiber fluoresces in response to damage or
stress. Right, control sample without the
mechanophore. Courtesy of C. Davis and
J. Woodcock/NIST.
A crystal of cysteine produced by drying a highly concentrated
solution of cysteine on a silicon nitrite substrate. Courtesy of FEI.
BRIEF
LLNL researchers are joining forces with the U.S. Navy Metalworking Center to study
ways to reduce the high cost of inspecting welds on nuclear-powered submarines.