
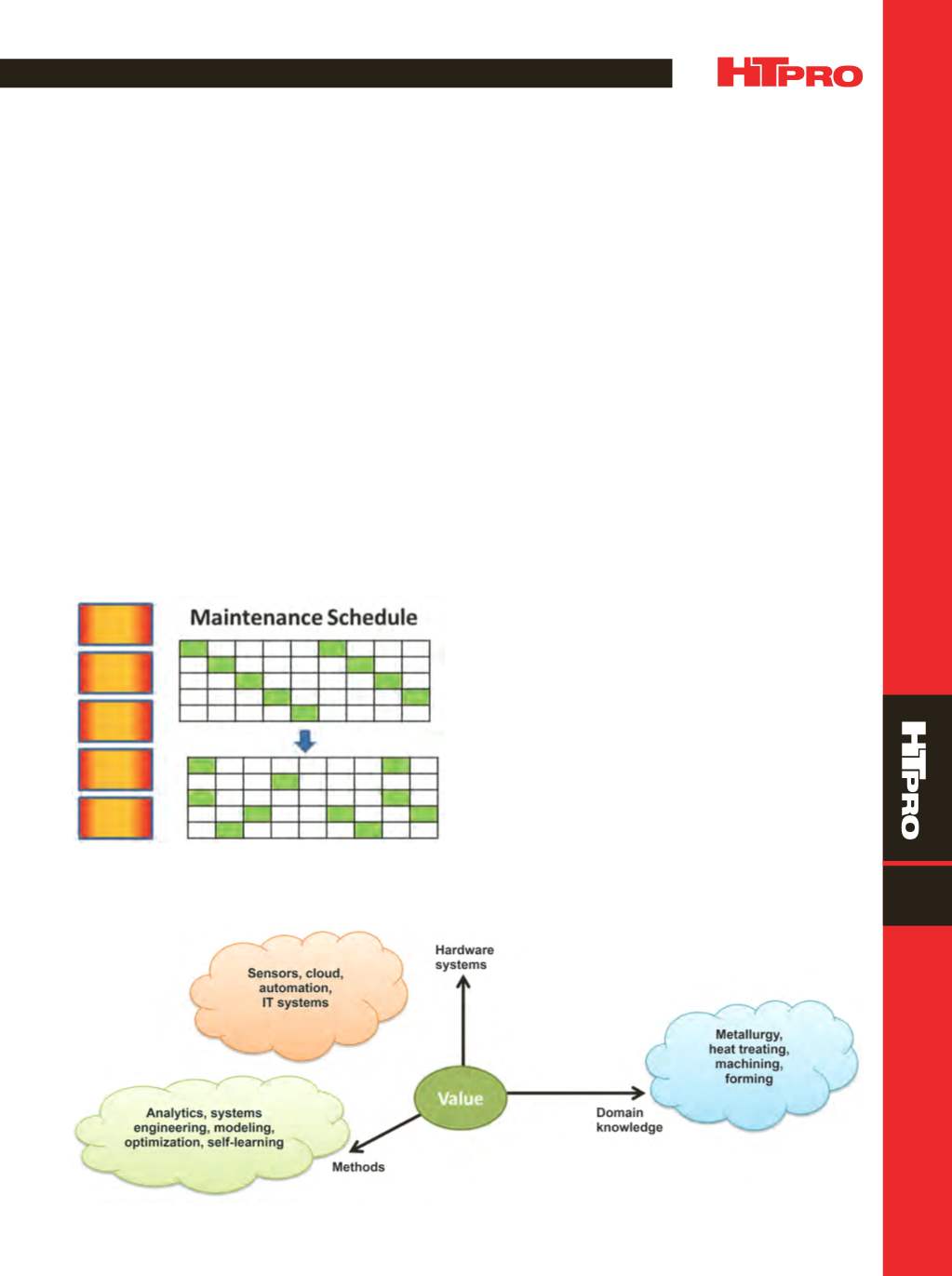
A D V A N C E D
M A T E R I A L S
&
P R O C E S S E S |
N O V E M B E R / D E C E M B E R
2 0 1 6
6 1
FEATURE
11
undergoing maintenance after a fixed time (Fig. 7). This
often results in suboptimal operation, with furnaces under-
going maintenance too early or too late. In the Industry 4.0
framework, sensing capability for furnace temperature-time
response is needed, such as the heat-up response cycle after
a charge is loaded, together with skin temperature moni-
toring. Connectivity and analytics capability would help to
identify influencing parameters, such as charge and basket
weight, to provide intelligence capability for burner health.
This would trigger furnace and burner maintenance require-
ments to create value in terms of proactivemaintenancewith
efficient operation and energy reduction. The Industry 4.0
framework also provides architecture to connect the mainte-
nance staff through appropriate alert systems, either through
a computer systemor mobility and wearable solutions.
CONCLUSION
Industry 4.0 is in the early technology evolution stage
with tremendous business expectations and significant
research grants available to pursue the technology. Few orga-
nizations have taken the lead in identifying cases for using and
applying this technology, while the IT infrastructure is nearly
ready to be implemented. The challenge lies in identifying val-
ue-driven use cases, which could impact efficiency and prod-
uct cost and quality. In the area of heat treating, an additional
challenge will be finding talent with a deep understanding of
physical metallurgy and the industrial heat treating domain,
in addition to the ability to convert this understanding into
analytics, algorithms, and self-learning intelligence that lever-
age IT systems. The immediate need for the future of this
emerging technology is development of such interdisciplinary
engineering skillsets (Fig. 8), which couldbe the biggest obsta-
cle to successful scale-up of this technology.
~HTPro
For more information:
SatyamS. Sahay is a John Deere Fel-
low, materials engineering, John Deere Technology Center
India, John Deere India Pvt. Ltd., Tower XIV, Cybercity, Mag-
arpatta City, Pune 411 013, India,
satyamsahay@yahoo.com.
Fig. 7 —
Time-based, staggered furnace maintenance schedule,
which has a significant impact on efficiency if transformed into a
furnace health-based schedule.
Fig. 8 —
Interdisciplinary skills needed to successfully leverage Industry 4.0 in the context of heat treating.
health, machining steps prior to carburizing could be fine-
tuned to anticipate distortion and better manage distortion
in the final product. Furthermore, depending on the location
of the part in the carburizing step, finishing operations could
bemade part specific, thereby having highly predictable dis-
tortion in the product. In the Industry 4.0 framework, sensing
capability is required for:
•
Composition information
•
The health of both furnace and oil-quench tank
•
Part location
•
Connectivity and analytics capability to predict hard-
enability and distortion
•
Intelligence capability to fine-tune recipes based on
instantaneous inputs
•
Operating conditions
•
Deriving location-specific finishing conditions to
create value in terms of mitigating distortion in preci-
sion components
Furnace maintenance:
In a heat treating shop with a
battery of furnaces, the maintenance schedule is designed
predominately on a time interval, with specific furnaces