
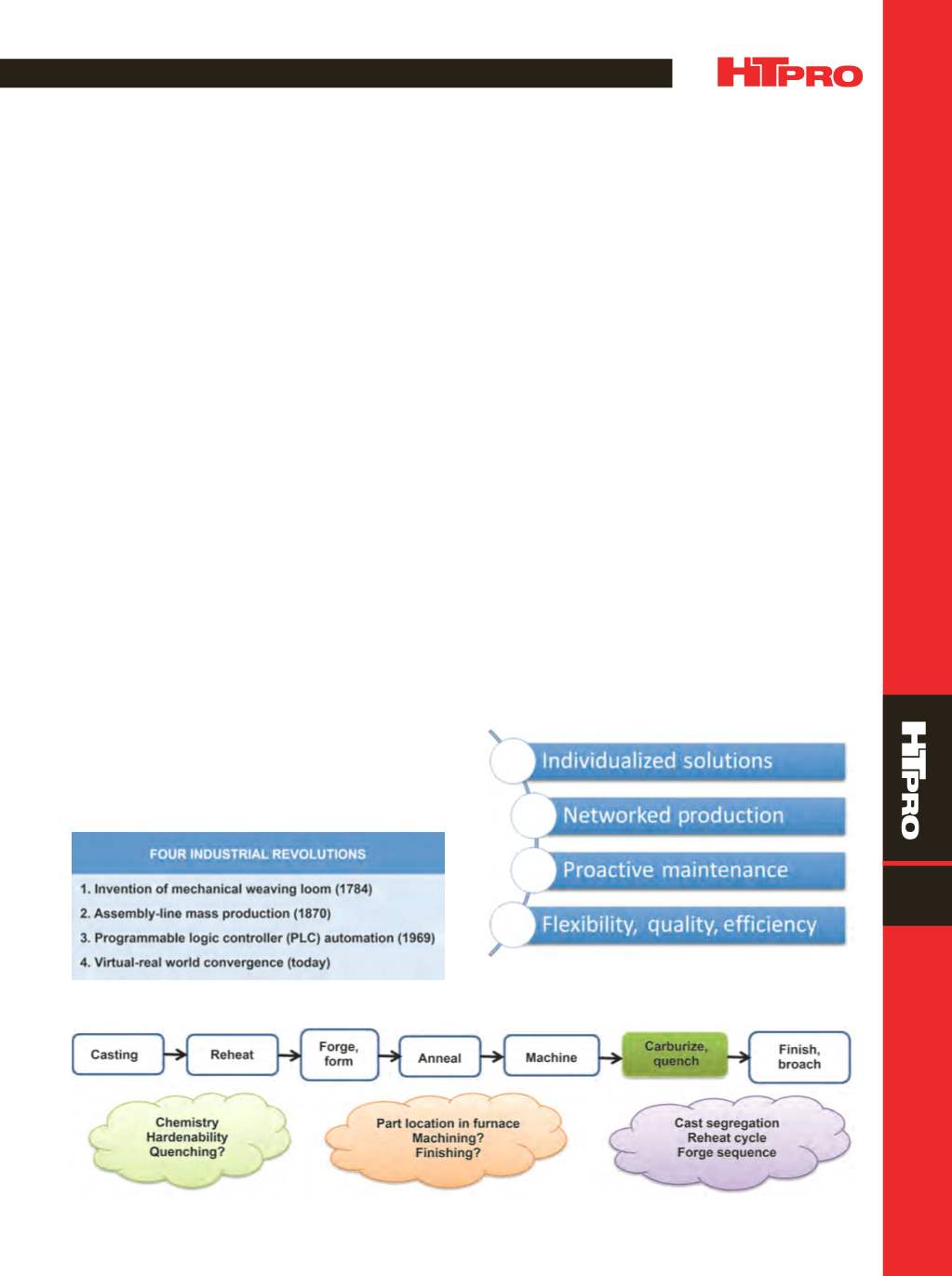
A D V A N C E D
M A T E R I A L S
&
P R O C E S S E S |
N O V E M B E R / D E C E M B E R
2 0 1 6
5 9
FEATURE
9
INDUSTRY 4.0 MEETS HEAT TREATING
Industry 4.0 is in the early technology evolution stage with tremendous business expectations.
Satyam S. Sahay, FASM,*
John Deere Technology Center India, Pune
I
ndustry 4.0, or Internet of Things (IoT), is an emerging
technology trend in the manufacturing arena, and is
widely considered the fourth industrial revolution (Fig. 1).
IoT, where convergence of the virtual and real world is envi-
sioned, is characterized by:
•
Physical and virtual connectivity across product
development cycles
•
Multifunctional synergies, including engineering,
manufacturing, quality, and customer support
•
Higher level of intelligence from connected data-
bases, products, and process models, which could
lead to more informed and autonomous decisions
with self-learning intelligence developed within the
organization
Key business drivers for this revolution include a higher
level of efficiency and quality achieved through individual-
ized solutions at the component or machine level, better
leverage of networked production across the supply chain,
and proactive equipment maintenance (Fig. 2). In addition,
significant emphasis will be placed on organizational knowl-
edge development over time.
The emergence of Industry 4.0 will significantly impact
heat treating operations aswell. Themost significant change
will be a change in the current mindset, i.e., changing from
the current silo view of the heat treating process to con-
sidering it part of the connected production operation. A
connected gear-making process is illustrated in Fig. 3. Data
collected from heat treating operations, which is typically
used for quality audit purposes, would be leveraged to pro-
vide part-level data sharing for improved pre- and post-op-
erations. Transfer of specific data, for example, chemical
composition data from the steel mill and the casting, could
provide better control of reheating, annealing, and carburiz-
ing operations, which in turn would help mitigate and man-
age distortion in these precision components.
Further, identifying the location of specific components
in batch type operations would help to better design recipes
for machining and finishing operations. Such individualized
solutions at the part level would bring a transformational
change to quality control at the product level. One of the big-
gestchangesintheheattreatingoperationwouldbewithrec-
ipe management, which is now
heuristically driven
—mainly
by trial and error. The significant amount of production and
quality data together with their mathematical models would
help to develop self-learning and self-evolving heat treating
recipes, suitable for current production and quality needs
with due consideration of the current furnace health and
Fig. 1 —
Four industrial revolutions in human civilization.
Fig. 2 —
Key business drivers for Industry 4.0, or Internet of Things
(IoT), the fourth industrial revolution.
Fig. 3 —
Integration of heat treating operations into the process chain for gear-making.
*Member of ASM International