
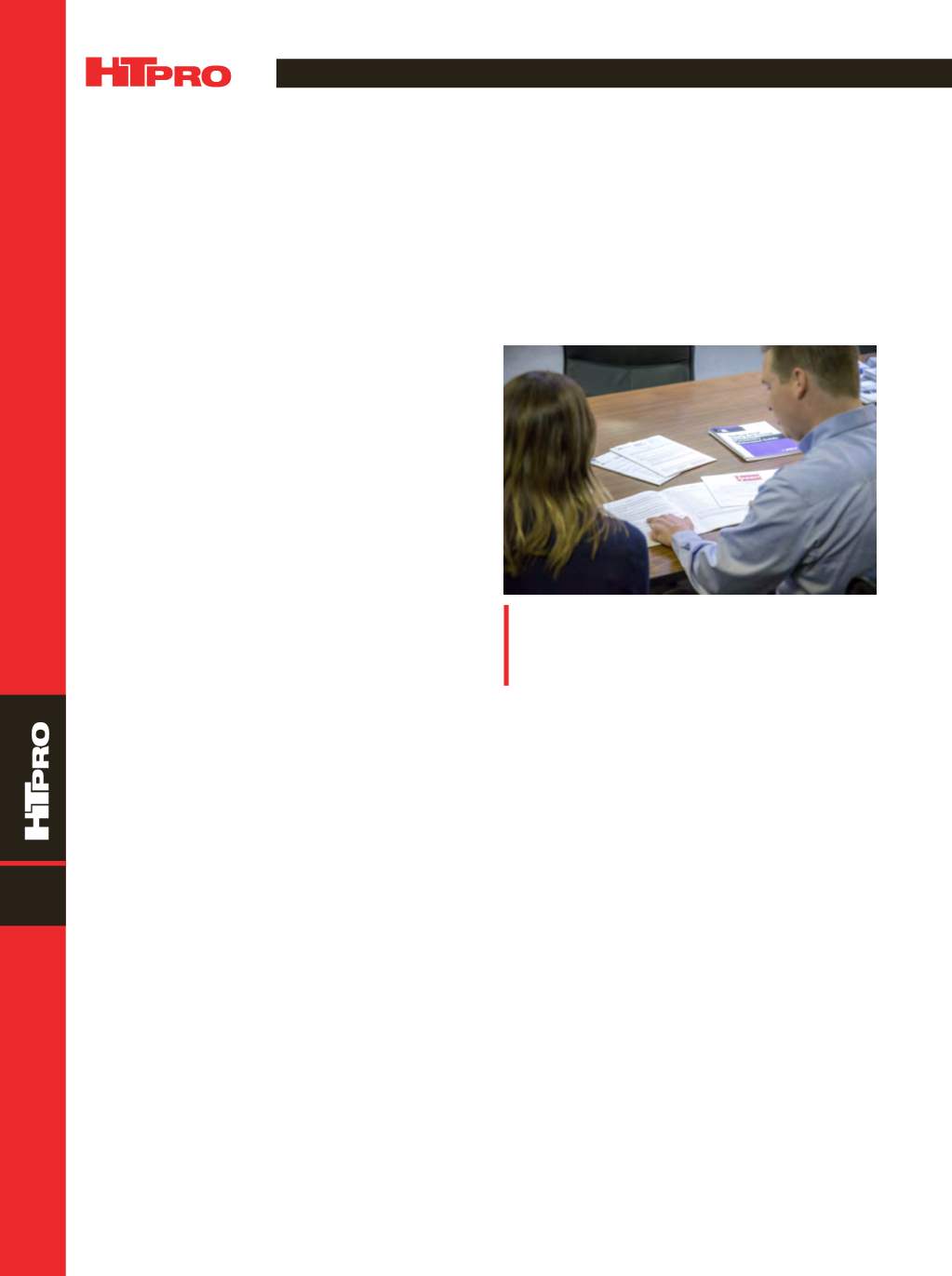
A D V A N C E D M A T E R I A L S & P R O C E S S E S | N O V E M B E R / D E C E M B E R 2 0 1 6
5 6
FEATURE
6
A
erospace Material Specification (AMS) standards
and the Nadcap accreditation process play key
roles in ensuring that manufacturers performing
heat treating and other special processes adhere to con-
sistent, high-quality standards for producing aerospace
products. While preparing for a Nadcap audit can seem
daunting, a series of articles has been developed that dis-
cusses some of the recommended resources for prepar-
ing for and executing a successful audit. The first part of
this series (June 2016,
HTPro
) looked at preparing for and
scheduling an audit. The second part (September 2016,
HTPro
) addressed the internal audit process, nonconfor-
mances, and completing the internal audit. This final arti-
cle looks at the official audit process, auditor interactions,
and completing the official audit.
EXECUTINGA SUCCESSFUL OFFICIAL AUDIT
After performing an internal audit and submitting the
necessary documentation, the official audit is the next step
in the Nadcap accreditation process. The official audit is an
independent, objective activity designed to verify that you
are operating under a specified state of control
[1]
. Having
control over your processes and equipment—essentially
every aspect involved inmanufacturing aerospace compo-
nents—places you in the best position to consistently meet
and adhere to industry quality standards for all aerospace
products.
Close control of your processes is important as cer-
tain processes, such as heat treatment and brazing, are
considered special processes (i.e., processes where it is not
possible to completely verify that the final product meets
the specified requirements). Therefore, these processes
must be validated in advance to ensure products are free
of defects and meet the aerospace industry’s high quality
standards. The only way to guarantee quality results is to
guarantee the process and demonstrate control through a
Nadcap audit.
In addition to preparing for the audit process and
performing an internal audit, a few best practices are rec-
ommended for executing a successful audit; these include
verifying the desired scope of accreditation, scheduling
key personnel, and informing the auditor in advance of any
schedule considerations.
Verifying the scope of accreditation:
When starting the
official audit, one of the first things you typically do with
the auditor is verify that the scope of accreditation sub-
mitted when scheduling the audit has not changed. The
standards and specifications you selected to be audited
against are what the auditor will go over in detail during
the audit process. It is also important to note that you can-
not remove or add any accreditations once the auditor has
finished verifying the scope.
Scheduling personnel:
According to some compa-
nies that have undergone a Nadcap audit, it is import-
ant to have personnel who performed the internal audit
available during the official audit process. Key personnel
typically include those most knowledgeable about day-to-
day processes, as well as those who regularly operate the
equipment. It is also important to inform all personnel of
the audit process and confirm that they understand their
role in making the audit successful as the auditor may
choose to talk with one of them during the official audit.
Informing the auditor of schedule considerations:
Scheduling is crucial during the official audit. In most
OBTAINING NADCAP ACCREDITATION: HELPFUL GUIDELINES
FOR PASSING YOUR AUDIT, PART III
Learn how to simplify the process of obtaining Nadcap accreditation for your heat treating
facility by paying heed to some of the challenges others have experienced.
Nathan Durham,
Ipsen USA, Cherry Valley, Ill.
During the Process segment of the Nadcap audit, the
auditor will spend a significant portion of time reviewing
specification checklists and both historical and live jobs.
Images courtesy of Ipsen.