
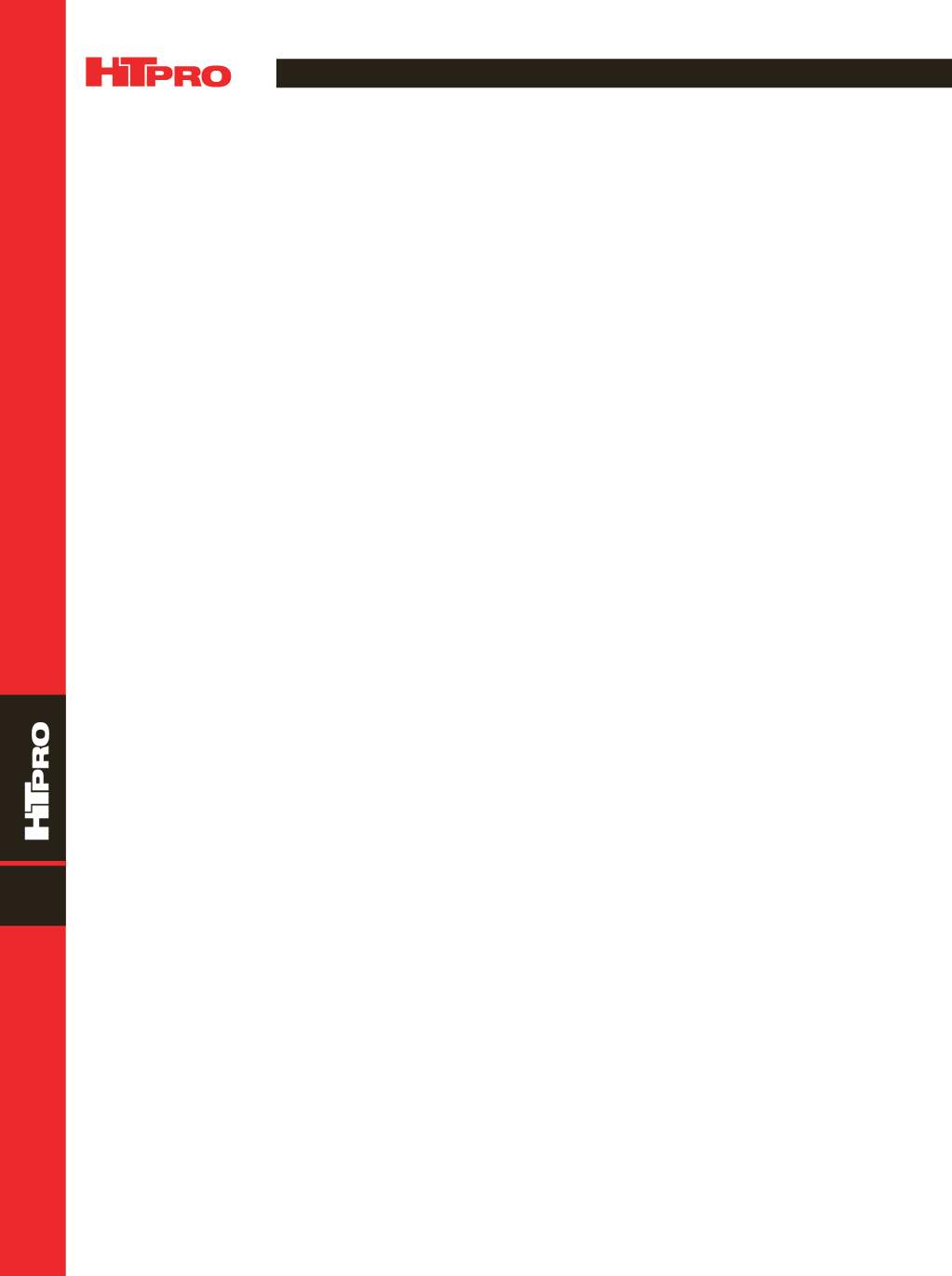
A D V A N C E D M A T E R I A L S & P R O C E S S E S | N O V E M B E R / D E C E M B E R 2 0 1 6
5 8
FEATURE
8
•
Root cause of the nonconformance
•
Product impact of all nonconformances
•
Corrective action taken
•
Date of corrective action implementation
•
Action taken to prevent future reoccurrences
•
Objective evidence
Performing root-cause analysis
. The process of per-
forming root-cause analysis for the official audit is identi-
cal to the steps applied during the internal audit. However,
a recommended best practice is to take advantage of the
root-cause training PRI offers; this training will help you
better understand how to identify them as related findings
can sometimes be grouped together, depending on the
ultimate root cause. Having a similar root cause does not
necessarily mean the number of findings will be reduced,
but knowing how to perform root-cause analysis is an
essential part of the official audit process.
Applying corrective actions.
This
is the next step after
performing root-cause analysis. In making a corrective
action, you should define the resolution made to address
the issue and cite the timing of implementation. For exam-
ple, if you determined that the root cause of a finding for
improperly located load thermocouples is a lack of oper-
ator training, the corrective action would be to provide
operator training at a specific frequency. You should also
include the training schedule that has been followed since
the corrective action was implemented.
When going through these steps after the audit, it
is also important to note that you have 21 calendar days
from the end of the official audit to submit your initial
response concerning any findings. You then have seven
calendar days to submit each subsequent response with
four total responses allowed. Thirty extra days are allotted
if more time is needed. However, using these extra days
can affect your merit, and using more than the 30 extra
days (or more than the allotted four responses) could lead
to an audit failure
[2]
.
Identifying successful practices from the accredita-
tion process, as well as areas that could use refinement,
ultimately helps contribute to your success on future
audits. Continually refining your processes and methods
enables you to enhance the quality and safety of the com-
ponents you process.
CONCLUSIONS
Auditors are tasked with evaluating a specific set of
standards and noting any findings that do not adhere to
set specifications. They play a key role in ensuring sup-
pliers successfully adhere to the high quality standards
of the aerospace industry. It is important to remember
that Primes have established global quality standards to
ensure aircraft and traveler safety. The Nadcap accredi-
tation process not only helps ensure the safety of all who
use these products, but also helps companies continually
refine and improve their processes. Whether it is your first
or 10th Nadcap audit, continually refining and developing
your audit process will contribute to a positive and suc-
cessful experience each time.
~HTPro
For more information:
Nathan Durham is an electrical
solutions manager at Ipsen. For technical information,
contact
technical@ipsenusa.comor 844.464.7736 (select
1), Ipsen USA, 984 Ipsen Rd., Cherry Valley, IL 61016,
ipsenusa.com.
References
1. American Society for Quality, asq.org/
learn-about-quality/auditing.
2. P. Evans and E. Jacklin, Nadcap Supplier Tutorial,
Performance Review Institute, p 37, 2013.