
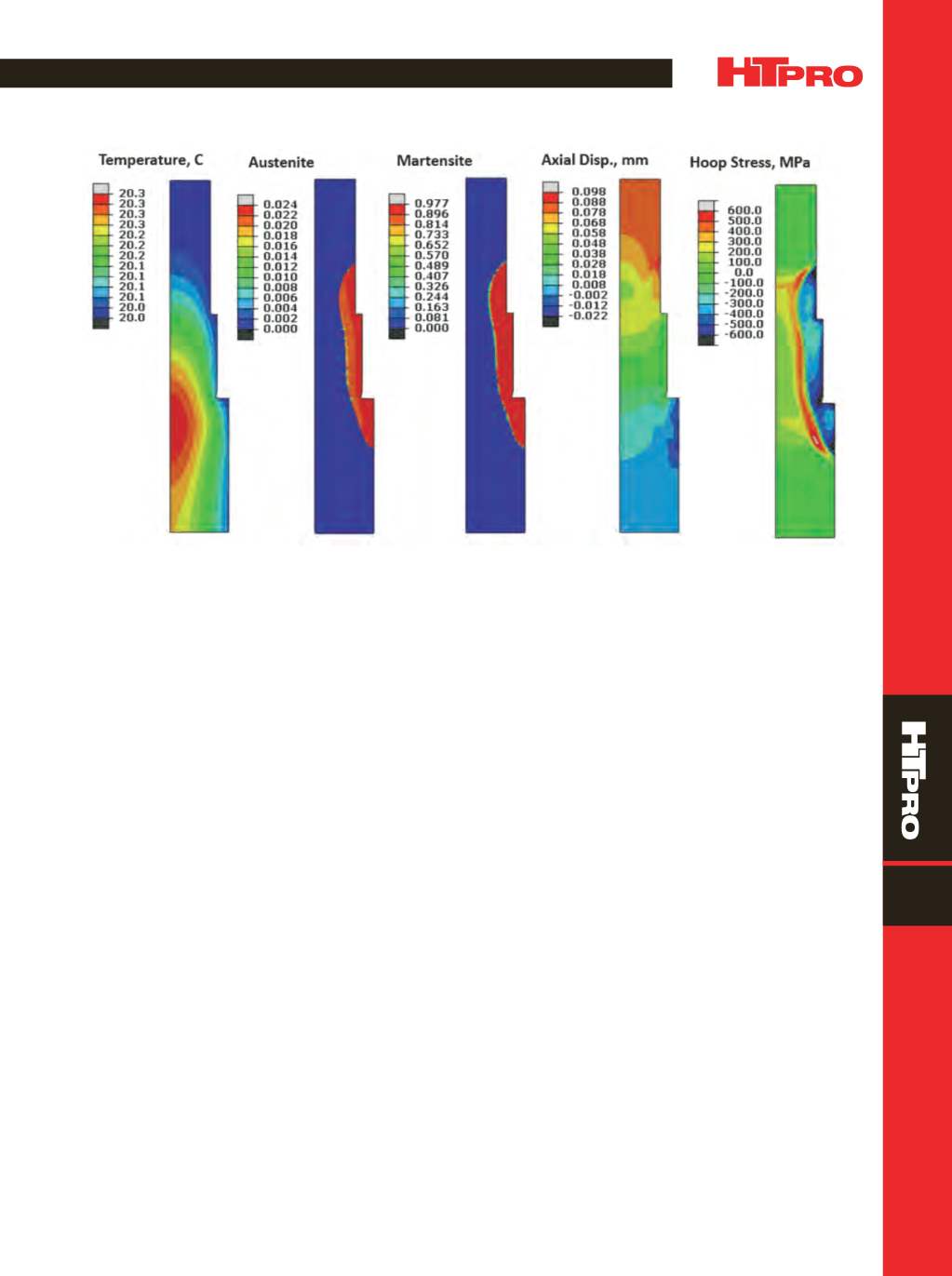
A D V A N C E D
M A T E R I A L S
&
P R O C E S S E S |
N O V E M B E R / D E C E M B E R
2 0 1 6
6 7
FEATURE
17
Compressive residual stresses are preferred on the surface.
However, to balance surface compression, tensile stresses
exist under the case or at the core, which may lead to fail-
ures if the material at those locations exhibits metallurgical
ormicrostructural irregularities (e.g., material is not clean) or
if the applied load is too high. Process optimization based on
computer modeling is a critical factor to optimize the stress
and hardness distribution in specific applications.
CONCLUSION
Years of experience, leveraged by advancements in
high performance computers, have improved the cost effec-
tiveness of applying computer simulation during the design
and development stages for induction hardening processes.
This shortens the learning curve, reducing development
time and enabling accurate inductor design and process
optimization.
~HTPro
References
1.
Induction Heating and Heat Treating
, Vol 4C,
ASM Hand-
book
, V. Rudnev and G. Totten, eds., ASM Intl., 2014.
2. D. Bammann, et al., Development of a Carburizing and
Quenching Simulation Tool: A Material Model for Carbu-
rizing Steels Undergoing Phase Transformations,
Proc.
2nd Intl. Conf. on Quenching and Control of Distortion
,
p 367-375, 1996.
3. Z. Li, B. Ferguson, and A. Freborg, Data Needs for
Modeling Heat Treatment of Steel Parts,
Proc. MS&T
Conf.
, p 219-226, 2004.
For more information:
Zhichao (Charlie) Li, Dante Solu-
tions Inc., Cleveland, OH 44130,
(440) 234-8477,
charlie.li@
dante-solutions.com,
www.dante-solutions.com.
Fig. 9 —
(a) Temperature, (b) austenite phase, (c) martensite phase, (d) axial displacement, and (e) hoop stress distributions at the
end of quenching.
(b)
(a)
(c)
(d)
(e)