
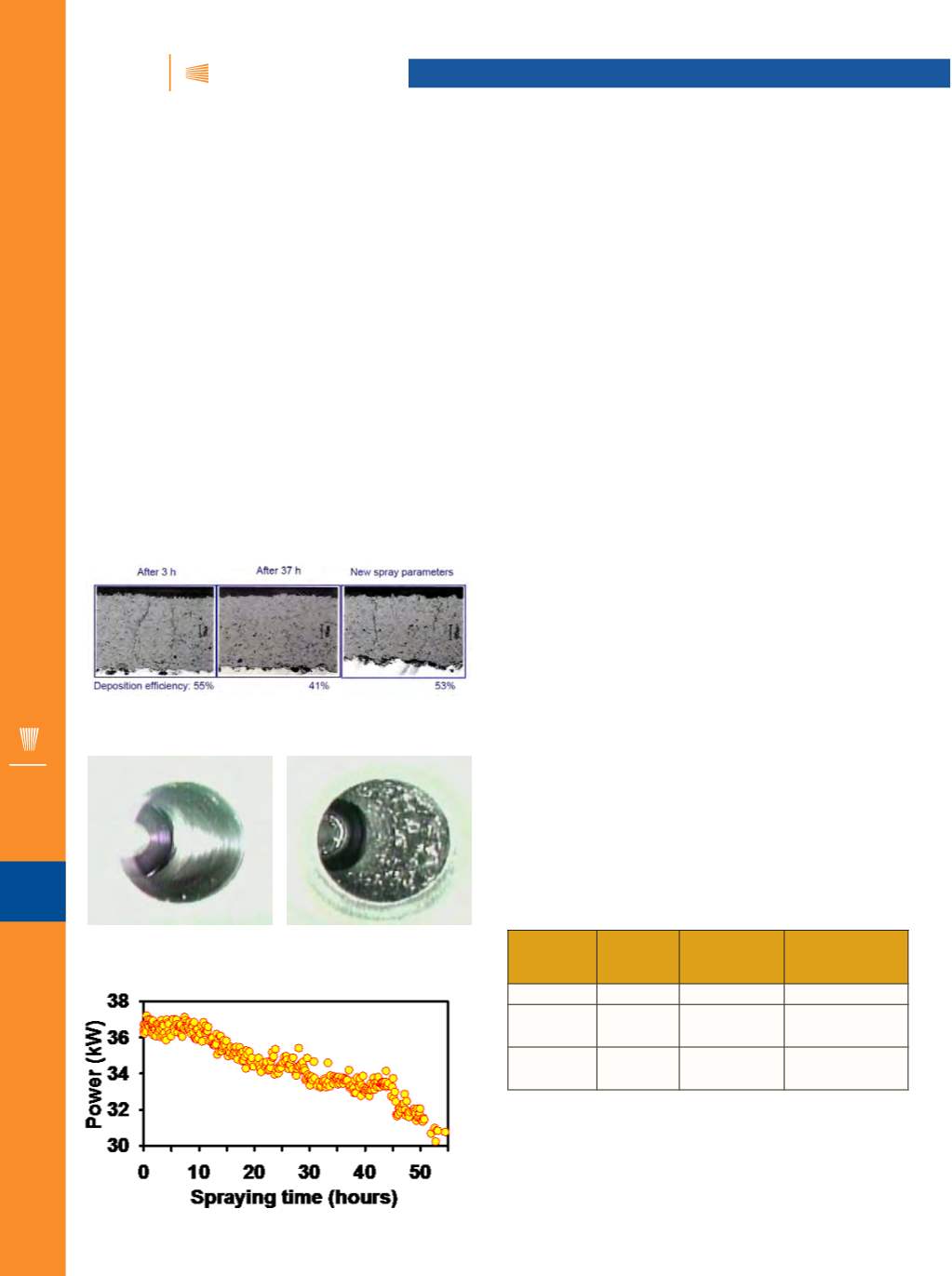
iTSSe
TSS
A D V A N C E D M A T E R I A L S & P R O C E S S E S | N O V E M B E R / D E C E M B E R 2 0 1 6
4 4
iTSSe
TSS
CASE STUDY
12
REASON TO CONSIDER RESURFACING
Keeping a particle’s characteristics constant over time
yields coatings with very similar properties. An experiment
was conducted where 8%-YSZ is sprayed for 37 hours starting
with a brand new set of electrons. The torch is stopped and re-
started every hour. Visual inspection of the inside of the nozzle
is carried out every hour and gun power is measured. Finally,
particle characteristics are monitored using an online spray
diagnostic tool from Tecnar, Canada. After 37 hours, the elec-
trodes are worn, gun power has decreased, and the initial mi-
crostructure of the coating (TBC) has disappeared. However,
after the 37 hours, spray parameters were modified to retrieve
the initial particle properties as well as corresponding coating
characteristics such as porosity, vertical crack network, and
deposition efficiency (DE).
VALUE OF INSPECTION
Nearly three decades ago, thermal spray researchers
recognized the need for advanced diagnostic tools able to pro-
vide spray material characteristics just before impingement
on the part, independently of upstream parameter controls.
This need was focused mostly around fundamental under-
standing of the spray process, validation of thermo- and flu-
id-dynamic models, development of advanced materials, and
development and optimization of spray equipment. Produc-
tion managers, on the other hand, had different objectives
in mind—namely improving coating reproducibility (P
pks
and
C
pks
), extending electrode lifetime, reducing test coupons, im-
proving DE, better forecasting of coating thickness, and spray-
ing correctly the first time.
OPTION
It is well known that lot-to-lot variations exist for com-
mercially available powders, and that powders supposed to
be a direct replacement sometimes yield very different coat-
ings. Below is an example where the same powder (reference)
has been used for more than a decade. For various reasons,
an alternate supplier is sought. Two other suppliers propose a
direct replacement to the reference powder. The three mate-
rials are sprayed the same morning, with the same torch and
hopper, in the same spray booth, and by the same operator.
Coupons are produced and, for each spray run, particle char-
acteristics aremeasured using an online spray diagnostic tool.
BENEFITS
Results clearly show that Alternate-1 succeeded in pro-
viding a direct replacement powder, which was confirmed by
the coating microstructure. Alternate-2 provided a material
significantly different from the sensor standpoint, which was
also confirmed by coating microstructure.
~iTSSe
Powder
Average
velocity
(m/s)
Average
temperature
(°C)
Microstructure
Original
613
1549
Reference
Alternate-1
616
1535
Same as
reference
Alternate-2
652
1819
Different (denser
coating)
Formore information:
Luc Pouliot is executive vice president,
Tecnar, 1321 Hocquart St., Saint-Bruno-de-Montarville, QC,
Canada, J3V 6B5, 450.461.1221 ext. 235,
lpouliot@tecnar.com,
www.tecnar.com.
Images courtesy of Christian Moreau/National Research
Council of Canada.
ONLINE DIAGNOSTIC TOOLS IMPROVE
THERMAL SPRAY PROCESS
Fig. 1 —
Effect of electrode wear on coating characteristics.
Fig. 2a —
New electrode.
Fig. 2b —
Worn electrode.
Fig. 3 —
Evolution of plasma power over time.