
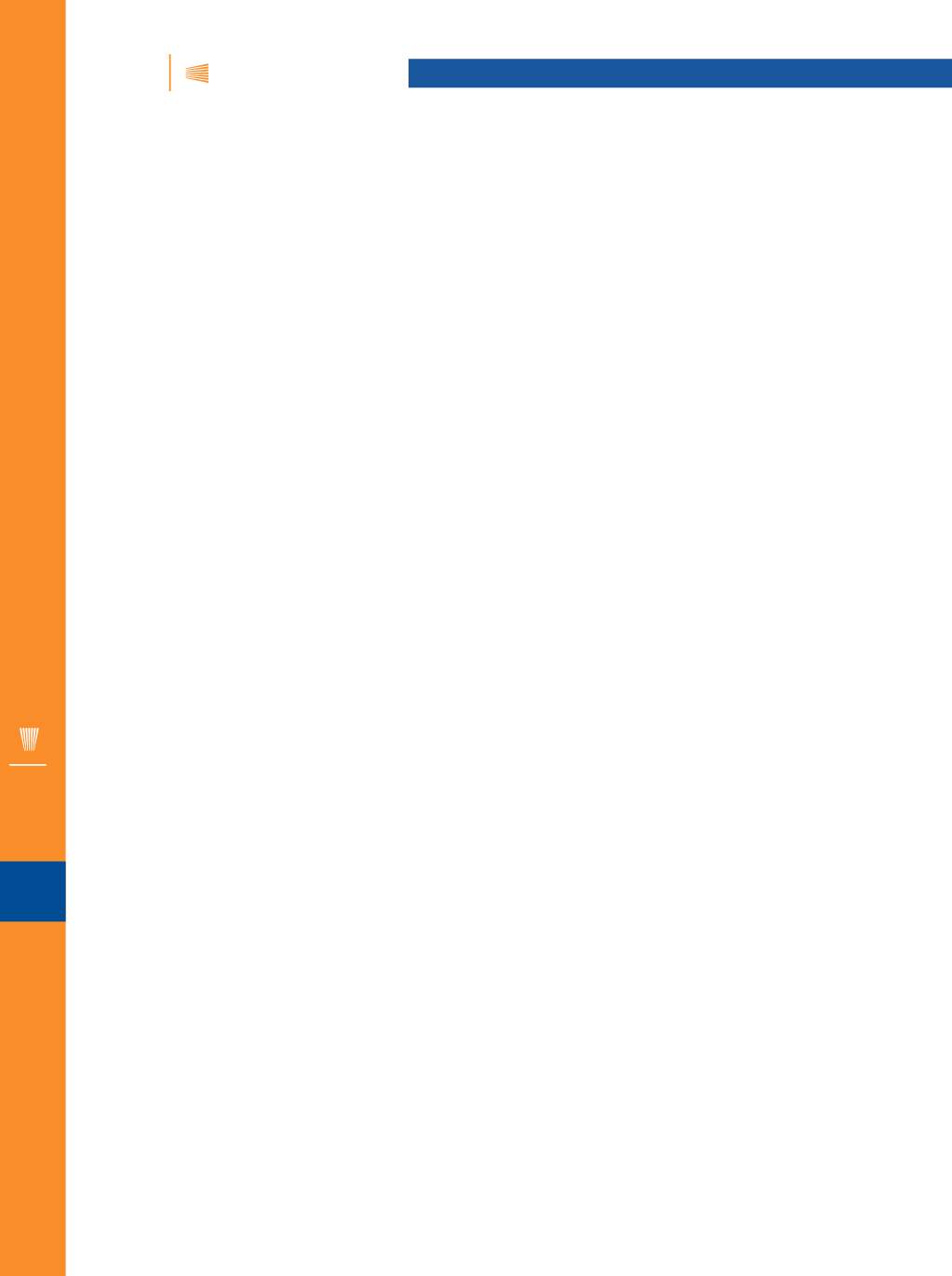
iTSSe
TSS
A D V A N C E D M A T E R I A L S & P R O C E S S E S | N O V E M B E R / D E C E M B E R 2 0 1 6
4 0
iTSSe
TSS
FEATURE ARTICLE
8
C
eramic and metallic thick film (>5 µm) processing
typically requires high temperatures or reactive en-
vironments that limit integration of film/substrate
materials with drastically different melting points or ther-
mal properties. In many spray processes, particle melting/
solidification and splatting lead to highly defective micro-
structures, containing splat boundaries, porosity, oxide in-
clusions, and nonstoichiometric oxide formation. Moreover,
melting/solidification associated with thermal spray can
lead to loss of volatile elements, change in original crystal
structure, and altered properties. The aerosol deposition
(AD) process is being used to create readily integrated, high
density ceramic and metallic thick films on a variety of sub-
strates at room temperature.
AEROSOL DEPOSITION PROCESS
In the AD process, thick films are produced by accel-
erating submicron tomicron sized particles onto a substrate in
a low-vacuum environment chamber. AD is able to conformal-
ly deposit dense, thick films up to ~100 µm, which bridges the
gap between coatings fabricated with thin film technologies
and traditional thermal spray technologies. AD takes advan-
tage of the low pressure within the vacuum by allowing spray
particles tomaintain velocity and consolidate in the solid state
into a film on impact with the substrate and subsequent film.
When the carrier gas for the aerosol powder hits the substrate,
the gas compresses and creates adensifiedgas layer above the
substrate, similar to the bow shock in cold spray. However, in
AD the bow shock/particle interaction is reduced in the vacu-
um, allowing small particles with lowmomentum to penetrate
the bow shock layer and impact the substrate with sufficient
kinetic energy for deposition.
AD takes advantage of the small particle size and the abil-
ity of ceramic and metallic particles to plastically deform at a
small length scale and bond as coatings. At Sandia National
Laboratories, fundamental experiments were performed to
understand how submicron ceramic particles deform and
bond to the substrate in the AD process. Ultimately, the knowl-
edge gained is being used in R&D work, yielding new potential
applications.
AD PROCESS RESULTS
Previous work has proven that submicron ceramic parti-
cles undergo dislocation nucleation/slip, plastic deformation,
fracture, and consolidation in the AD process at room tem-
perature. Submicron ceramic particles with diameters >100
nm capable of plastic deformation should be selected as feed-
stock for the aerosol deposition process. Submicron alumina
particles can deformplastically via dislocation nucleation and
slip, as well as fracture without fragmentation, under qua-
si-static compressive loading. Research also shows that im-
pact at high velocity can cause submicron alumina particles to
deform, change shape without fragmentation, and adhere to
the substrate as an anchor layer.
Bonding between an individual splat and substrate is
present near the middle of the splat whereas gaps remain
around splat edges. Subsequent particles impacting on the
splatted anchor layer produce a
tamping effect.
Gaps around
the splatted particles and substrate are closed and bonding
between the anchor layer and substrate is complete. Conse-
quently, film buildup relies on the tamping effect to deform,
fracture, and mechanically bond the arriving particles to the
already deposited particles. An example of AD Al
2
O
3
single
splats and coatings is shown in Fig. 1. Splat boundaries within
the coatings are undistinguishable from other grain boundar-
ies. The consolidated coating is polycrystalline with 15-30 nm
nanocrystals.
The fundamental knowledge on deformation and bond-
ing gained from the previous work provides a strong founda-
tion to mature the aerosol deposition process for fabricating
ceramic, metallic, and composite films on metallic, glass, and
plastic substrates at room temperature. Potential applications
of aerosol deposition being investigated include direct applied
multilayered ceramic capacitors, electrically conductive elec-
trodes, thermally and chemically resistant barrier coatings,
and electrically insulating films. Examples of AD material inte-
gration are shown in Fig. 2.
APPLICATION OF BaTiO
3
DIELECTRICS
The application of BaTiO
3
dielectrics for high tempera-
ture stable capacitors to enable high power electrical switch-
ing devices is explored. The high sintering temperature of
BaTiO
3
(T>1000°C) often prevents successful integration with
AEROSOL METHOD FOR ROOM TEMPERATURE
THICK-FILM DEPOSITION
Aerosol deposition offers an alternative to conventional thin
film processes when mesoscale coatings are needed.
Pylin Sarobol,* Andrew Vackel, Jesse Adamczyk,* Thomas Holmes, Mark Rodriguez, James Griego,
Mia Blea, and Harlan Brown-Shaklee, Sandia National Laboratories, Albuquerque, N.M.
*Member of ASM International