
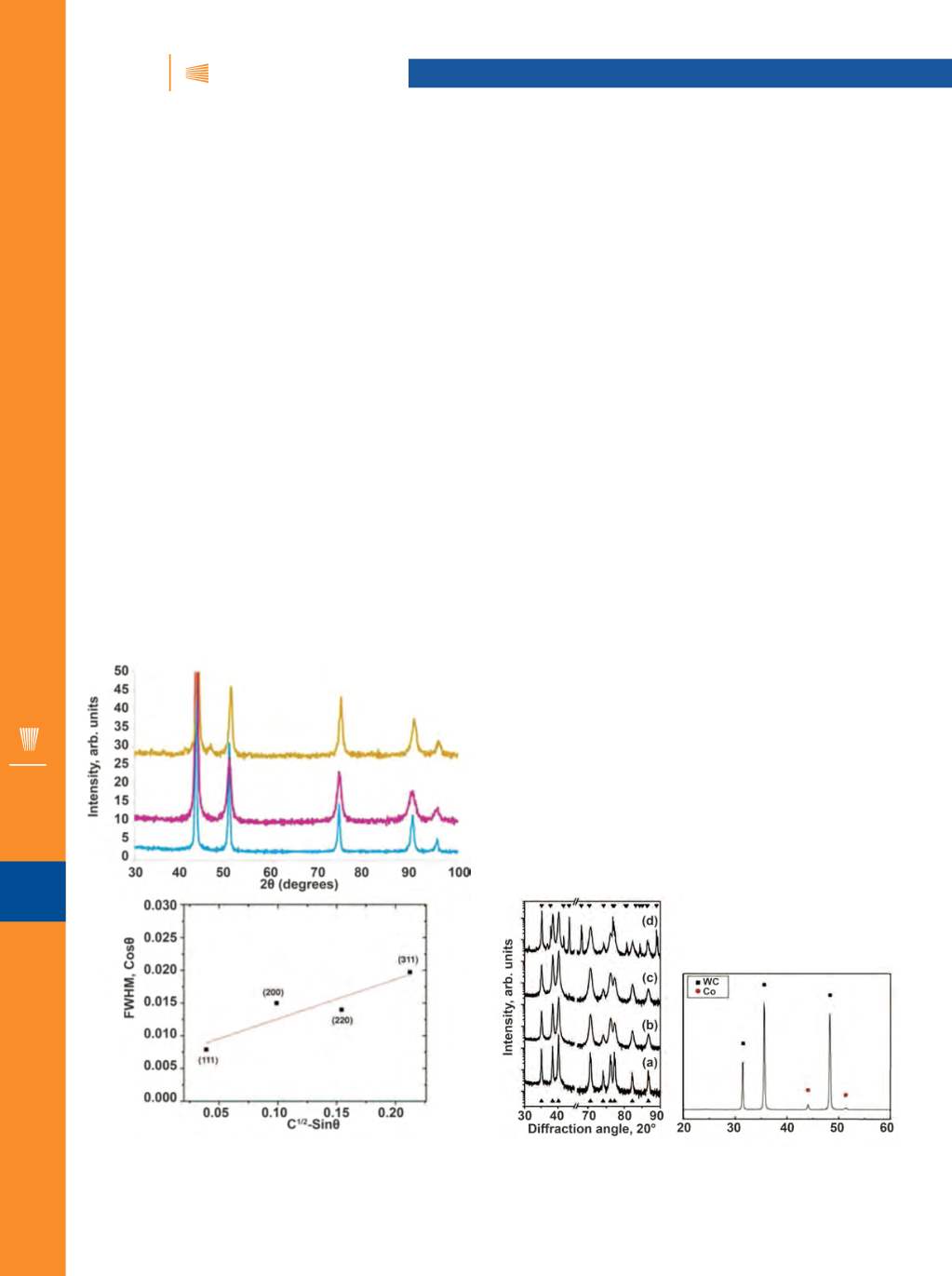
iTSSe
TSS
A D V A N C E D M A T E R I A L S & P R O C E S S E S | N O V E M B E R / D E C E M B E R 2 0 1 6
3 8
iTSSe
TSS
FEATURE ARTICLE
6
X
-ray diffraction (XRD) is a versatile tool for preliminary
characterization of phases in cold spray coatings. A
collimated beam of x-rays with a wavelength of 0.5 to
2 Å is diffracted by the crystalline phases in the specimen ac-
cording to Bragg’s law. The diffraction pattern identifies the
material’s structural properties, such as structure, lattice pa-
rameter, strain (which is measured with great accuracy from
the diffraction peaks), epitaxy, and size and orientation of the
crystallites. The probing depth is a fewmicrometers to tens of
micrometers, depending on the absorption coefficient of the
material for the particular wavelength of the x-ray probe.
Cold spray coating analysis starts with powder charac-
terization, followed by as-sprayed and heat treated coatings.
COLD SPRAY: ADVANCED CHARACTERIZATION
METHODS—X-RAY DIFFRACTION
This article series explores the indispensable role of characterization
in the development of cold spray coatings and illustrates some of
the common processes used during coatings development.
Dheepa Srinivasan, GE Power, GE India Technology Center, Bangalore
Fig. 1 —
(a) X-ray diffractograms comparing IN625 (nickel-base
superalloy) powders and cold spray IN625 coating show broaden-
ing of diffraction peaks in the coating, indicative of macroscopic
strain. (b) Hall-Williamson plot taken frompeak broadening data to
calculate the extent of strain. FWHM, full width at half maximum.
Fig. 2 —
X-ray diffraction patterns from (a) cold spray titanium coat-
ing after removal of progressive layers from the coating compared
with
α
titanium, indicating no phase transformation in the coating,
and (b) cold spray WC-Co without decarburization after cold spray.
(a)
(b)
Due to the severe plastic deformation that takes place during
high-pressure cold spray, the characteristic diffraction pat-
tern in the as-sprayed condition usually has broad peaks, as
shown in Fig. 1(a) for an IN625 coating. Peak broadening in the
as-sprayed coating compared to the powders can be due to
two factors—particle size broadening and broadening due to
strain (nonuniform). The full width at half maxima (FWHM) of
the diffraction peak is estimated from the Scherrer formula for
particle size broadening:
d
= 0.9λ/βcosθ
where
d
is particle size,
λ
is the x-ray’s wavelength,
β
is FWHM
of the x-ray peak (in radians), and
θ
is peak angle. Typically, the
Scherrer formula is based on the assumption that peak broad-
ening is caused by crystallite size. The nonuniform strain-in-
duced broadening effect of the FWHM is obtained by the
Williamson-Hall (WH) plot, which is derived by the equation:
ε = βcosθ −
A
/2sinθ
where
A
is expressed as
C
λ
/
d
,
C
is the correction factor (
∼
1),
and
d
is particle size. Figure 1(b) shows the WH plot for an
IN625 coating, with a grain size of 35 nm. XRD can identify coat-
ing phases and distinguish any changes to the phase equilib-
ria during cold spray. Figure 2(a) illustrates cold spray titanium
(a)
(b)