
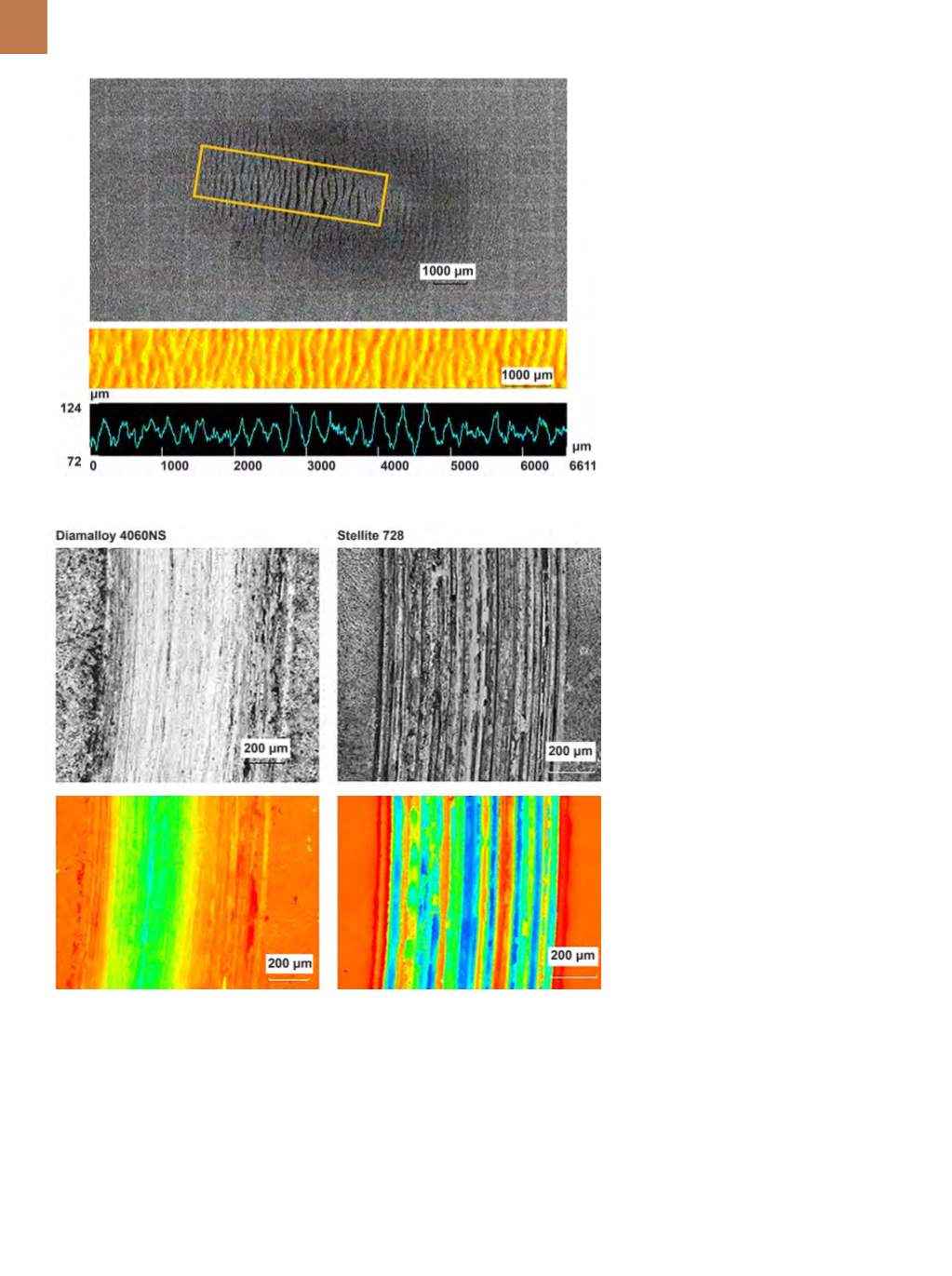
A D V A N C E D M A T E R I A L S & P R O C E S S E S | N O V E M B E R / D E C E M B E R 2 0 1 6
2 4
profilometry techniques that generally
provide a single 2D trace, which pro-
vides a linear profile or maximumdepth
of damage. Alternatively, a laser micro-
scope can rapidly provide a detailed 3D
topography map of the entire specimen
and enable valuable and quantifiable
parameters to be determined. Exam-
ples of these parameters include maxi-
mumand average depth of damage and
total volume lost, as well as various sur-
face textures such as adhesion.
In solid particle erosion, 3D scan-
ning via laser microscopy was used to
quantify the above parameters in sup-
port of development of the ASTM G211
high-temperature erosion test stan-
dard
[2]
. In addition, the level of detail
from laser microscopy can illuminate
topographical features that may be
relevant to the success or failure of a
material or related to the test equip-
ment’s inconsistencies. Analysis of the
sample in Fig. 4 shows surface pertur-
bations forming a series of ripples. In
this case, comparisons between the 3D
laser images and 2D contact methods
found that traditional 2D methods can
under or overestimate actual metal ero-
sion rates by more than 20%.
In elevated temperature sliding
wear for advanced cycle power gen-
eration, various hardfacing materials
behave differently as illustrated in
Fig. 5. Here, the Diamalloy 4060NS
HVOF spray coating shows a consis-
tent low wear rate while the Stellite 728
experimental GTAW cobalt alloy shows
significant gouging and adhesion under
the same test conditions. The 3D height
maps produced from laser microscopy
can be used to reliably quantify these
differences. In fact, research using
these techniques has shown that cur-
rent ASTM standards that only rely on
optical comparisons can be explained
in quantifiable terms
[3]
.
EVALUATING EROSION
DAMAGE
Erosion damage in steam turbine
valve stems presents a reliability chal-
lenge to utilities. Steam-grown oxides
appearing on the inside surfaces of
high-temperature boiler tubes and
pipes occasionally exfoliate and are
entrapped in the steam system. In the
Fig. 4 —
High resolution 3D color height map used to characterize a high-temperature erosion
test coupon.
Fig. 5 —
Quantifiable differences in high temperature wear behavior of potential high-temperature
wear resistant coatings/claddings for valves after high-temperature laboratory wear testing.
LASER MICROSCOPY FOR
HARDFACING ALLOYS
Tribology is the science of interac-
tions between two bodies. In general,
these interactions damage one or both
components. Characterizing the rate of
how this damage accumulates is criti-
cal for providing materials comparisons
under expected service conditions. EPRI
has been studying advanced hardfacing
alloys for high-temperature valves and
alternative materials and coatings for
erosion resistance.
The value of laser microscopy in
tribological examinations is that the
microscope can quickly provide infor-
mation above and beyond traditional