
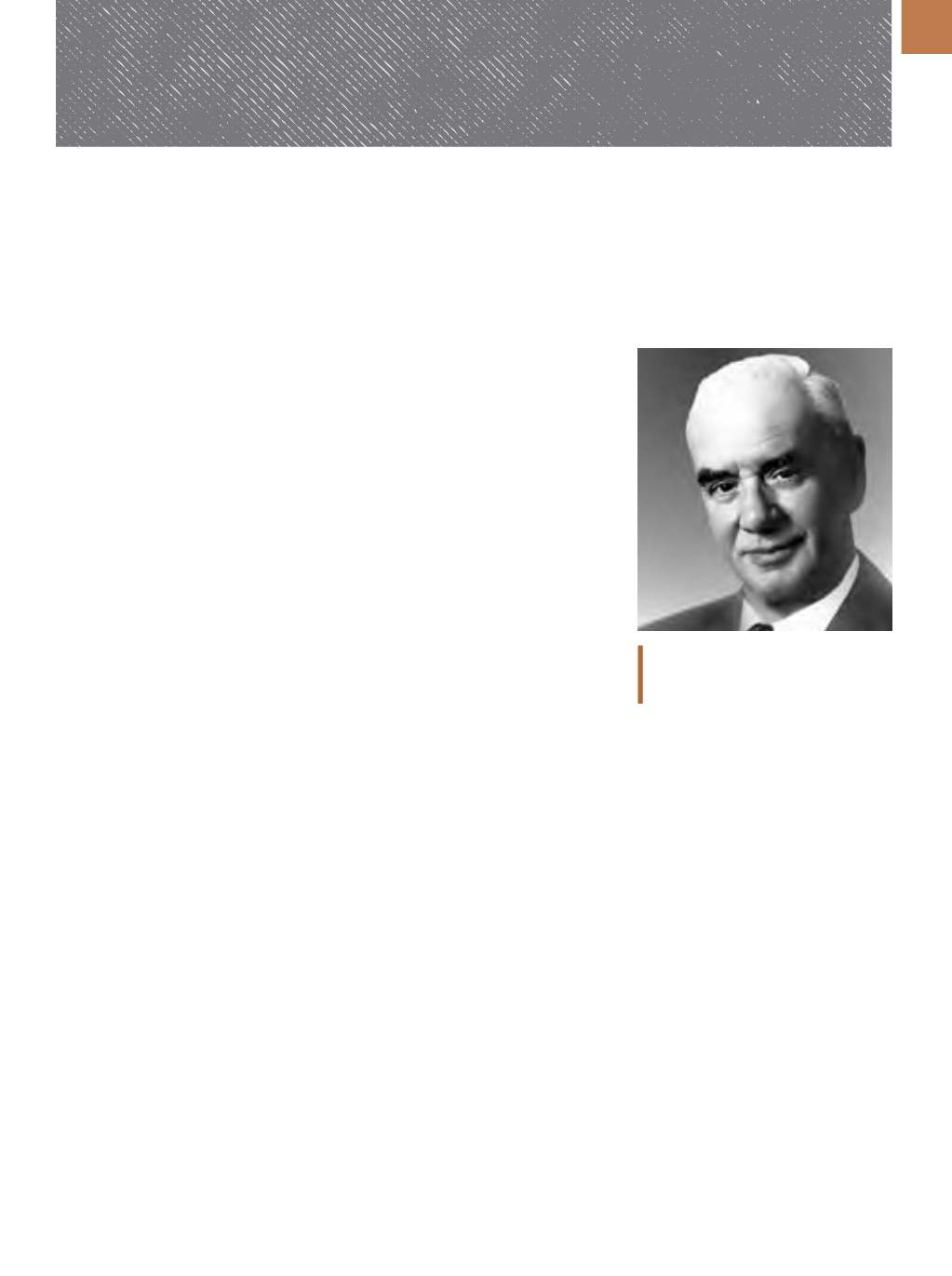
A D V A N C E D
M A T E R I A L S
&
P R O C E S S E S |
N O V E M B E R / D E C E M B E R
2 0 1 6
2 9
METALLURGY LANE
Metallurgy Lane, authored by ASM life member Charles R. Simcoe, is a yearlong series dedicated to the early history of the U.S. metals
and materials industries along with key milestones and developments.
THE DECLINE OF THE INTEGRATED STEEL INDUSTRY—PART I
FROM POOR LABOR RELATIONS AND DELAYED MODERNIZATION TO AN UNBALANCED PRODUCT MIX AND
INCONVENIENT MILL LOCATIONS, THE U.S. STEEL INDUSTRY BEGAN ITS STEADY DECLINE IN THE LATE 1950s.
T
he strike of 1959 was a watershed
moment in the history of the U.S.
integrated steel industry. The
strike itself was not the main event,
but it exposed industrywide problems
and failures that had existed for many
years. Among them were poor labor
relations, delayed modernization, an
unbalanced product mix, and inconve-
nient mill locations in relation to the
market. Other factors included steady
price increases to cover union contracts
rather than productivity improvements,
pollution that had to be controlled by
EPA rulings, andmanagement staff who
were paid the highest incomes of any
industry.
In the early 1950s, David J. McDon-
ald replaced Philip Murray, longtime
president of the steelworkers union.
McDonald was expected to be a moder-
ate negotiator due to his limited expe-
rience in the steel union. However, he
had a bitter rivalry with Walter Reuther
of the auto union who had been elected
head of the Congress of Industrial Orga-
nizations (CIO) after Murray. In subse-
quent negotiations, McDonald tried
to keep the steelworkers ahead of the
autoworkers: By 1959, steelworkers
were earning roughly 38 cents per hour
more than autoworkers (15%more).
Even so, McDonald never had the
same support of union members as
Murray did, so he always overreached in
his attempt to keep them loyal. A seri-
ous strike took place in 1956 with work-
ers out for 35 days. The final settlement
included Clause 2b—for Bethlehem
only—that gave the union a guarantee
that new technology would not reduce
the number of employees. This would
be the source of labor problems at
Bethlehem for years to come.
STRIKE OF 1959 AND LAGGING
TECHNOLOGY ADOPTION
The 1959 strike was the longest
in steel history at 116 days. Grievances
included wages, pensions, and paid
holidays. Bethlehem fought unsuccess-
fully to remove Clause 2b, and the strike
became a pivotal point in the history
of the U.S. steel industry. As the strike
continued, customers became seri-
ously concerned about supply sources
and their only recourse was imported
steel. The U.S. had been a net exporter
of steel during the 20th century, but in
1959 imports exceeded exports for the
first time with total imports reaching
4.7 million tons.
From1957-1962, steel use declined
8%per capita although the total market
was still growing slowly. At the same
time, the steel industry was trying to
upgrade and expand capacity. The lack
of modern technology adoption was
evident when Bethlehem built a new
open hearth shop in 1958 at Sparrows
Point for $200 million. Four years ear-
lier, a small steel company in Michigan
had installed the first basic oxygen fur-
nace (BOF) and Jones & Laughlin Steel
Corp. (J&L) installed these furnaces in
1959. The BOF process was invented in
Austria after World War II. BOF vessels
were similar to the earlier Bessemer
converters, except they used oxygen
instead of air to remove carbon from
cast iron. A heat of steel could be pro-
cessed in less than an hour compared
to six or eight hours for open hearth fur-
naces. Importantly, BOFs accomplished
this with fewer workers and produced
a superior product. New plants built
in Europe and Japan to replace those
destroyed in the war implemented new
BOFs.
There were 21 BOFs in operation
before United States Steel Corp. (USS)
built its first two at the Duquesne plant
in Pittsburgh in 1963, and 29 units when
Bethlehem Steel installed its first two
at Sparrows Point in 1964, replacing
40-year-old open hearths. That same
year, the company built two BOFs at
Lackawanna, which produced 2.5 mil-
lion tons per year. The U.S. produced
only 17% of its steel using BOFs in 1965,
while Japan produced 55%. As late as
1970, this ratio was 48% for the U.S. and
79% for Japan.
Reluctance to accept new technol-
ogy extended to the continuous casting
process—another European develop-
ment made after WWII. Molten metal
delivered from the blast furnace was
Philip Murray, first president of United
Steelworkers of America. Courtesy of
usw.org.