
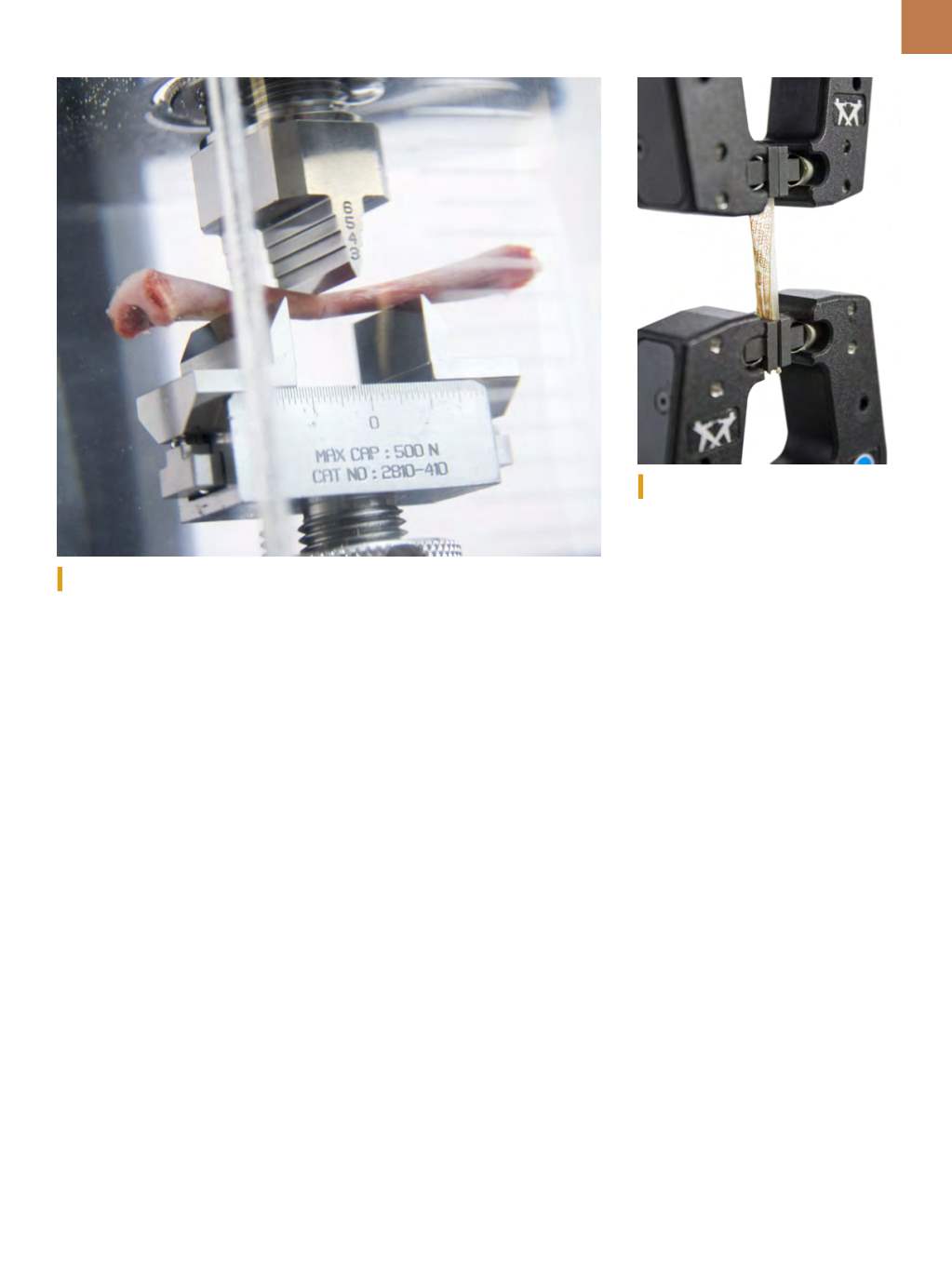
A D V A N C E D
M A T E R I A L S
&
P R O C E S S E S |
N O V E M B E R / D E C E M B E R
2 0 1 6
2 7
composed of smooth muscle, such as
the bladder, will exhibit a high level of
stress relaxation.
Fatigue testing,
also known as
dynamic testing, helps to character-
ize the lifetime properties of materials
that experience constant mechanical
loading. For example, a human heart
beats approximately 35 million times
per year. In order to ensure that an
engineered tissue material used in the
heart will last a minimum of 10 years,
the tissue needs to be subjected to at
least 350 million cycles of mechanical
loading. In order to complete this test-
ing in a reasonable amount of time, the
testing machine needs to run at a high
frequency. Using a dynamic testing
machine at 100 Hz, a researcher could
simulate 10 years of wear on a mate-
rial in just a few weeks. Fatigue testing
of biomaterials helps ensure that the
material will not yield, become dam-
aged, or fail within the required lifetime.
TESTING PARAMETERS
While mechanical testing of tis-
sues can range from a quick pull or
failure test to a months-long fatigue
test, all testing methods are critical to
understanding the bulk mechanical
properties of biomaterials and predict-
ing how those materials will behave
in the human body. In addition to the
variability inherent to biological mate-
rials, experimental setup for biomate-
rials testing also presents a challenge.
Testing biological materials can be
challenging due to the need for highly
sensitive force measurement, delicate
specimens that are difficult to grip, and
strainmeasurement that is often impos-
sible with traditional extensometers.
Highly sensitive force measure-
ment is needed for mechanical testing
of soft biomaterials. Soft tissue spec-
imens are usually small and the loads
required to pull these materials apart
are generally in the gram-force range.
With biological materials that require
pre-cycling before pull to failure, it
is important to ensure that the force
transducer is not only verified for accu-
racy in the load range for pre-cycling,
but also has the capacity to measure
force at specimen failure.
Determining the proper gripping
solution for testing biomaterials is
crucial to achieving consistent results.
The delicate nature of soft biomaterials
in combination with testing in physi-
ological conditions makes gripping a
challenge. Testing tissues in physio-
logical conditions to properly mimic
the environment inside the human
body is relatively easy to achieve using
a heated bath. However, consistently
inserting a specimen in a set of grips
while submerged in a bath can be diffi-
cult. To save time and make sure spec-
imen alignment is repeatable, using a
bath with a lifting mechanism is rec-
ommended so that the specimen can
be inserted into the grips and then sub-
mersed as the bath raises into place.
When choosing a gripping mechanism
for soft tissues, side-acting grips that
are manual, spring actuated, or pneu-
matically closed generally work well.
In addition, the gripping face should
feature a material with high friction to
avoid specimen slippage while mini-
mizing the necessary clamping force.
When tensile testing soft tissues
to failure to determine maximum force
or maximum strain at break, calculat-
ing strain from the machine’s extension
is widely accepted as suitable. This
method of measuring strain is calcu-
lated by taking the machine’s cross-
head extension data and dividing it by
the initial grip separation. However,
Flexural testing of rat bone.
Tensile testing of an insect wing.