
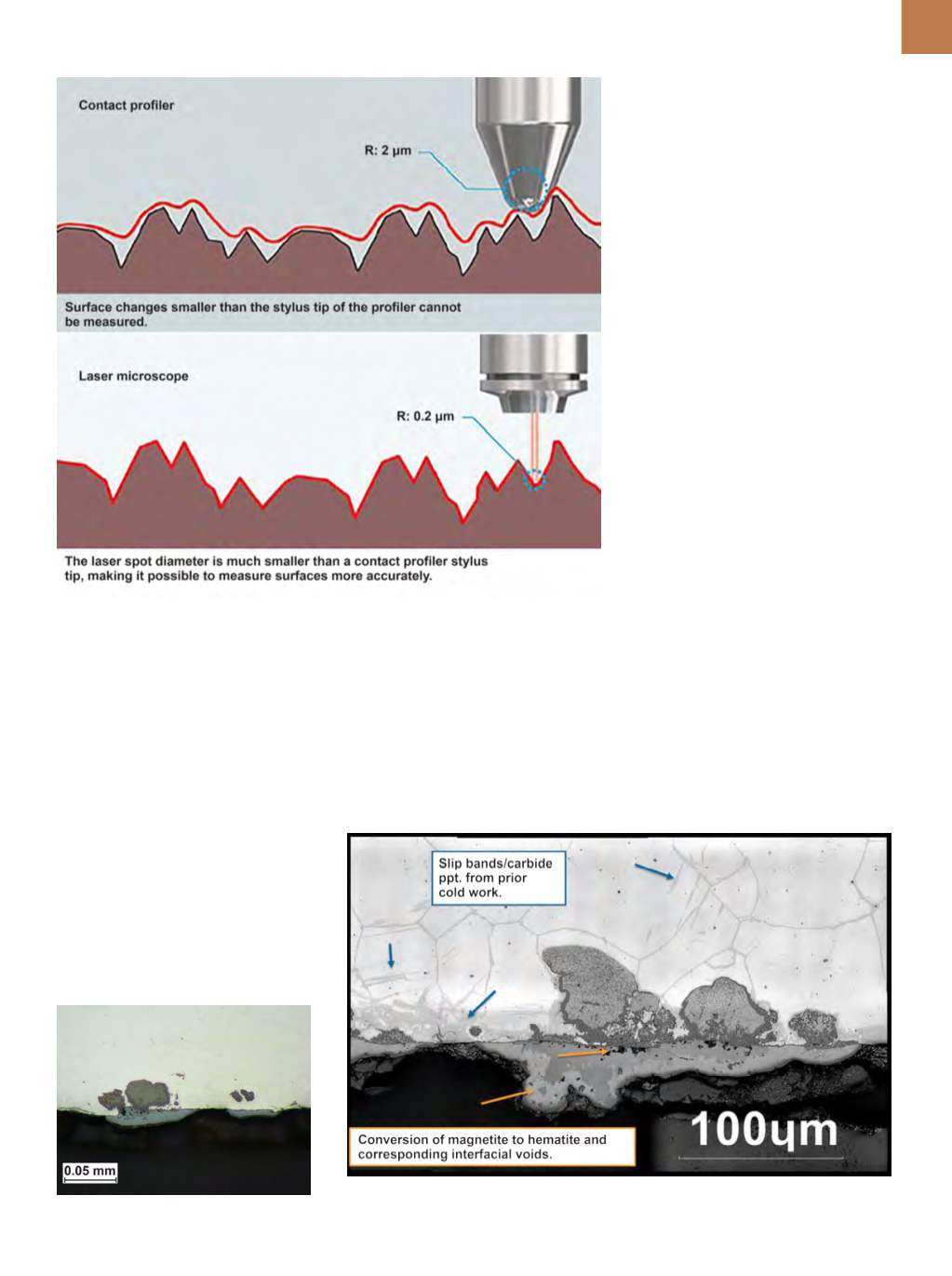
A D V A N C E D
M A T E R I A L S
&
P R O C E S S E S |
N O V E M B E R / D E C E M B E R
2 0 1 6
2 3
for ~24,500 hours. Using careful sample
preparation including a final ~20 hour
vibratory polishing step, the optical
image of the ID oxide scale was pro-
duced in Fig. 3a.
Internal and external oxidation
in the form of nodules is clearly evi-
dent. However, little information about
grain structure and oxide morphology
is revealed, which is critical to under-
standing material behavior. Chemical
etching could be used to evaluate such
features, but experience shows this
leads to artifacts in the oxide scales.
Using the same as-polished sample and
the laser microscope, large area and
small area high-resolution images were
obtained including detailed charac-
terization of nodule regions. Figure 3b
shows results at approximately 2000×.
On the as-polished material, the grain
structure of steel is observed.
Furthermore, slip bands are evi-
dent from the original SP process as
well as clear evidence of multiple oxide
scale morphologies and voids form-
ing at the inner and outer oxide sur-
face. Comparing Figs. 3a and 3b clearly
shows that the laser microscope offers
enhanced possibilities for detailed
understanding of materials without
the need for surface etching, which can
damage scales and potentially lead to
erroneous results.
Fig. 3a —
Optical image of steam-side scale.
Fig. 3b —
Unetched (as-polished) laser image of the inner diameter surface of a shot-peened
304 H stainless steel superheater tube after ~24,500 hours of service.
Fig. 2 —
Comparison between contact profiler and laser microscope.
lotte, N.C., a Keyence VK-X160K has
augmented, and in some cases re-
placed, metallic alloy characterization
traditionally done using either opti-
cal microscopy or scanning electron
microscopy. The VK-X160K uses a red
semiconductor laser (658 nm wave-
length) with maximum z-axis (depth)
display resolution of 5 nm, maximum
magnification of 19,200×, and motor-
ized x-y stage with a range of 100 × 100
mm. The microscope’s ability to show
subtle differences in surface relief, de-
velop high-resolution large area met-
allurgical maps, and quantify surfaces
through non-contact profilometry has
opened up new avenues in research.
Inner diameter (ID) shot-peening
(SP) of austenitic stainless steel boiler
superheater (SH) tubing has been used
to manage short-term (<10,000 hour)
steam-side oxidation and exfoliation
in utility boilers
[1]
. To improve under-
standing of long-term behavior of this
technique, EPRI received SP-304H SH
tubing after exposure in a utility boiler