
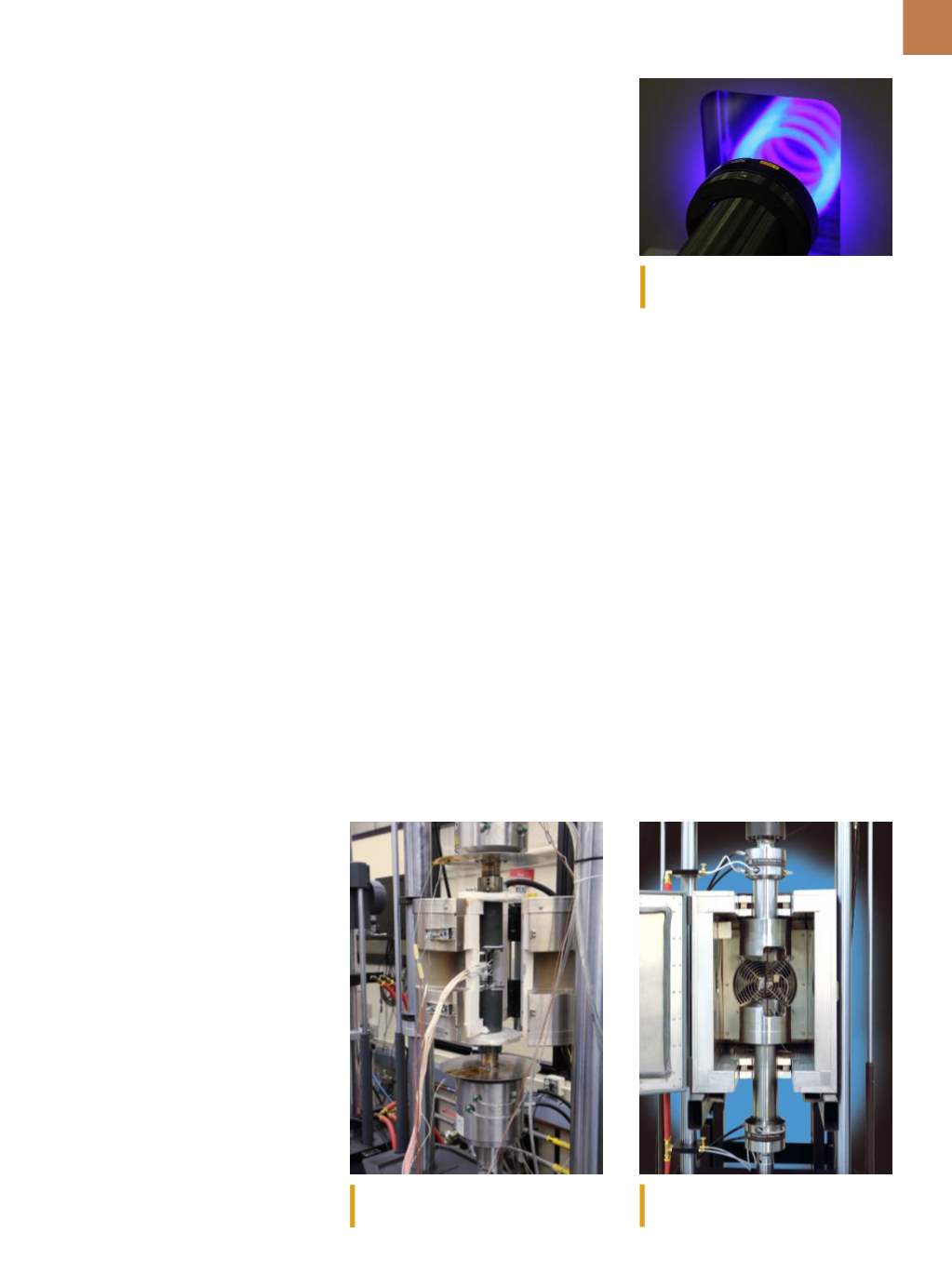
A D V A N C E D
M A T E R I A L S
&
P R O C E S S E S | J U N E
2 0 1 6
1 7
D
esigners of ultra-efficient aircraft,
automobiles, and power genera-
tion systems need materials with
high strength-to-weight ratios as well
as those that can withstand high oper-
ating temperatures for extended time
periods. In both cases, fuel efficiency
is the goal. To achieve this, researchers
must accurately and precisely mea-
sure material properties at elevated
temperatures.
However,
elevated temperature
means different things to different
researchers. In general, there are three
distinct temperature ranges for materi-
als with the highest strength-to-weight
ratios. The first range, 200°-425°C,
applies to polymer matrix composites
(PMCs). The second range, 800°-1200°C,
is used for metals. The third range is
suitable for ceramic matrix composites
(CMCs), which are tested to 1500°C. For
PMCs, traditional use temperature is lim-
ited by the glass transition temperature
(T
g
) of the matrix resin, where the matrix
becomes soft and rubbery. Aerospace
materials generally use epoxy resinswith
a T
g
of approximately 200°C or lower.
Composites that use polyimide
resins with much higher T
g
values report
use at temperatures as high as 371°C.
For metals, many mechanisms can
define high temperature because the
traditional use temperature is limited by
loss of strength, onset of creep deforma-
tion, change in material microstructure,
or the appearance of high temperature
corrosion. Single crystal Ni-base alloys
and some refractory alloys are used in
the air to roughly 1200°C. For the most
advanced CMC applications, associ-
ated testing requirements reach nearly
1500°C, with even higher temperatures
envisioned for the future. In each range,
there are tradeoffs that test engineers
need to carefully consider in order to run
effective tests, measure material prop-
erties at elevated temperatures, and
acquire high-quality results.
These tradeoffs directly affect the
accuracy and precision of mechani-
cal test data, because any object that
needs to hold, touch, or be placed near
the specimenmay increase data scatter.
In other words, grips, extensometers,
furnaces, and environmental chambers
are potential sources of experimental
error. Variability that arises from these
components tends to be systemic, so
solving an issue with one tends to raise
issues with another.
HIGH-TEMPERATURE
SPECIMEN EXAMINATION
To understand how these inter-
related issues manifest during test
setup, consider a typical specimen.
PMC and CMC specimens are flat and
cannot be gripped in the same way as
round, threaded, or button-head metal-
lic specimens. For PMCs, cost effective
and easy-to-use hydraulic wedge grips
are usually appropriate. PMC speci-
mens often lack compressive strength
across their thinnest cross section, and
the evenly applied pressure from the
hydraulic wedges protects the fibers
in the polymer matrix. These hydraulic
grips not only prevent the fibers from
being crushed, but also help maintain
correct pressure as the chamber and
grip wedge head heat up.
The tradeoff is that grip wedge
heads are relatively large, and for best
results, must fit inside an environmen-
tal chamber. The chamber for these
lower temperature PMC tests is often
larger than the furnaces required for
higher temperature metal or CMC tests.
Although larger equipment usually is
less efficient, the thermal mass of the
grips and chamber leads to very stable
test environments.
On the other hand, the larger
chamber makes using inexpensive
contact extensometers difficult. With a
smaller furnace, extensometers can be
situated outside the chamber, allow-
ing them to translate motion from the
contact arm to the capacitor plates or
strain-gaged beam. But with a larger
chamber, the motion is not effectively
translated because the arms become
too long and cause additional measure-
ment variability. A short arm extensom-
eter needs to be positioned inside the
chamber, but the elevated temperature
would damage its sensitive electronics.
One way to solve this problem is
with video extensometry and digital
image correlation, which can be situated
outside the chamber. A chamber with
a window lets these technologies look
inside and measure specimen motion
Blue LEDs illuminate chamber during
PMC test.
Temperature profiling of a button-head
metallic specimen in 1200°C grips.
Remotely actuated hydraulic grips for
PMC specimen at temperatures to 425°C