
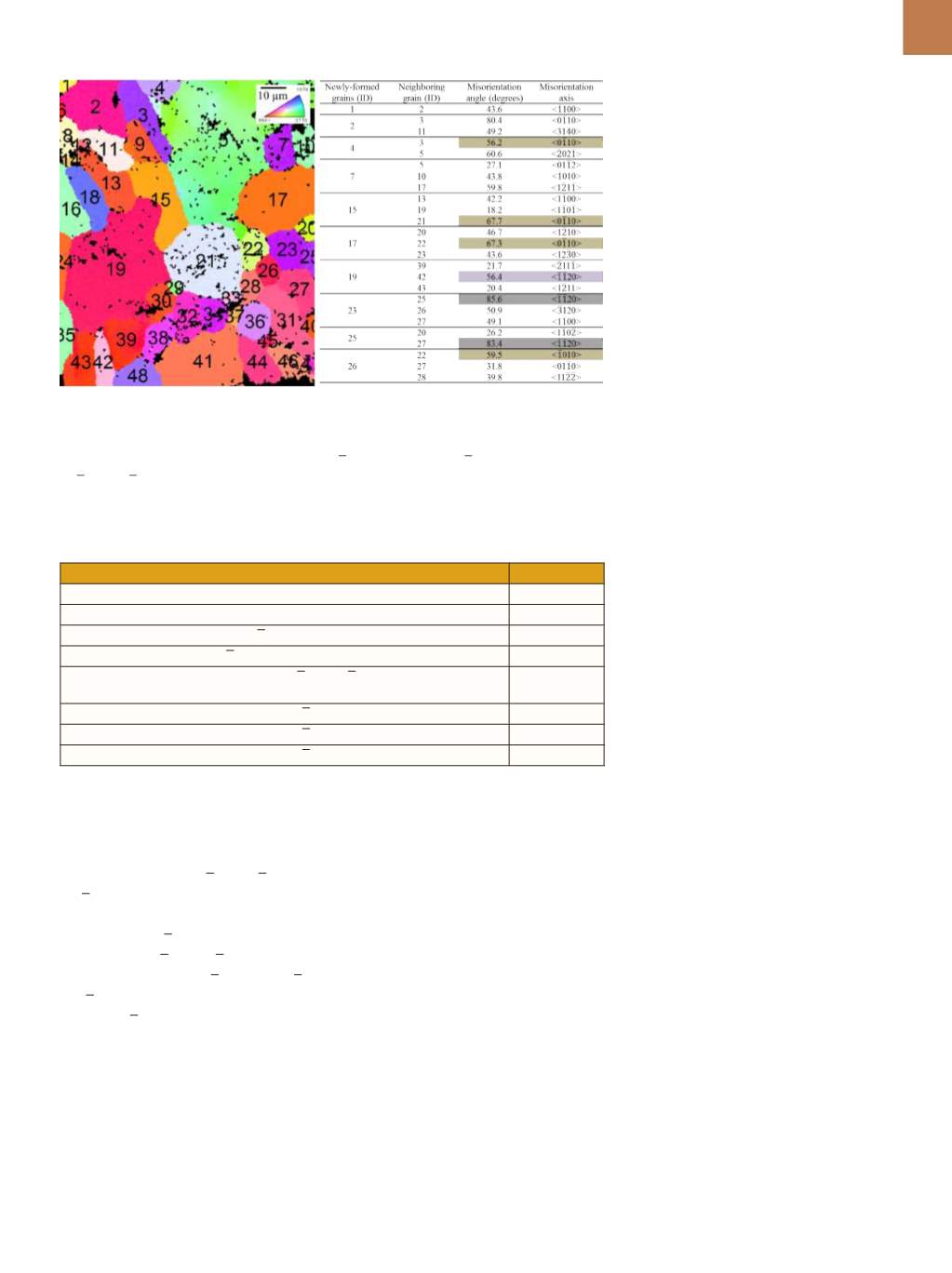
A D V A N C E D
M A T E R I A L S
&
P R O C E S S E S | J U N E
2 0 1 6
2 1
the heating process are listed in Table 1.
As shown in Table 1, among themisorien-
tation relationships observed between
the newly formed grain boundaries,
rotation axis about <1010>, <1120>, and
<1011> were prevalent. Grain boundar-
ies with orientation relationships corre-
sponding to {1012} extension twinning
(86° about <1120>), {1011} contraction
twinning (56° about <1120>), and (1012)
–(0112) extension double twinning (60°
about <1010>) were also commonly
observed. This was expected to be due to
the recovery and growth of twins formed
during the rolling process.
SUMMARY
An in-situ experimental technique,
which involves annealing inside an SEM
combined with EBSD analysis, was devel-
oped to understand the microstructural
evolution and recrystallization behavior
of rolled ZE20. Recrystallization started
at 423-473 K. A completely recrystallized
microstructure with relatively equiaxed
and strain-free grains was observed at
548-573K,andgraingrowthwasobserved
afterward. Misorientation angle-axis rela-
tionship analysis for the newly formed
grains reveals grain boundary formations
with various twin relationships. The char-
acterization methodology developed in
this work sets the stage for future exper-
iments to understand and control the
recrystallization behavior of commercial
alloys. Future work is targeted at employ-
ing this technique to understand the
effect of RE content on the recrystalliza-
tion behavior of Mg alloys.
~AM&P
For more information:
Carl J. Boehlert
is professor, Department of Chemical
Engineering and Materials Science,
Michigan State University, 428 South
Shaw Ln., Room 2527, East Lansing, MI,
48824-4437,
boehlert@egr.msu.edu,
517.353.3703,
msu.edu.
Acknowledgments
Funding for this research was sup-
ported by National Science Foundation
Division of Material Research (Grant No.
DMR1107117) through the Materials
World Network program. Vahid Kha-
demi, a Ph.D. student at Michigan State
University, is acknowledged for assis-
tance in developing the in-situ heating
stage setup.
References
:
1. S. Wright and M. Nowell, A Review of
in situ EBSD Studies,
Electron Backscat-
ter Diffraction in Materials Science,
p 329-337, 2009.
2. A. Luo, R. Mishra, and A. Sachdev,
High-Ductility Magnesium–Zinc–
Cerium Extrusion Alloys,
Scripta Mate-
rialia,
V 64.5, p 410-413, 2011.
3. S. Yi, et al., Mechanical Anisotropy
and Deep Drawing Behaviour of AZ31
and ZE10 Magnesium Alloy Sheets,
Acta
Materialia
V 58.2, p 592-605, 2010.
4. M. Perez-Prado and O. Ruano, Tex-
ture Evolution During Annealing of
Magnesium AZ31 Alloy,
Scripta Mate-
rialia,
V 46.2, p 149-155, 2002.
5. C. Boehlert, et al., In Situ Analysis of
the Tensile and Tensile-Creep Deforma-
tion Mechanisms in Rolled AZ31,
Acta
Materialia
, V 60.4, p 1889-1904, 2012.
6. J. Bohlen et al., The Texture and
Anisotropy of Magnesium–Zinc–Rare
Earth Alloy Sheets,
Acta Materialia
,
V 55.6, p 2101-2112, 2007.
7. A. Chakkedath, et al., The Effect of Nd
on the Tension and Compression Defor-
mation Behavior of Extruded Mg-1Mn
(wt%) at Temperatures Between 298 K
and 523 K (25° C and 250° C),
Metallurgi-
cal and Materials Transactions A
, V 45.8,
p 3254-3274, 2014.
8. S. Mohapatra and J. Jain, Overview
of Static Recrystallization in Magne-
sium Alloys,
Advanced Materials &
Processes,
p 28-31, 2015.
9. L. Mackenzie and M. Pekguleryuz,
The Recrystallization and Texture of
Magnesium–Zinc–Cerium Alloys,
Scripta
Materialia
V 59.6, p 665-668, 2008.
Fig. 3 —
EBSD IPF map (along the normal direction of the sample) after achieving 548 K. The
ID for each grain is highlighted. Ten new grains were formed during this heating step, which
resulted in 44 unique grain boundaries. The misorientation angle-axis relationships highlighted
by grey, purple, and tan shades correspond to {1012} extension twin, {1011} contraction twin,
(1012) – (0112) and extension double twin boundaries, respectively.
TABLE 1
—
CHARACTERISTICS OF THE NEWLY FORMED
GRAINS IN ROLLED ZE20 DURING IN-SITU HEATING
Characteristic
New grains
Number of new grains formed
59
Number of resulting unique grain boundaries
159
Grain boundaries with {1012} extension twin relationship (%)
9
Grain boundaries with {1011} contraction twin relationship (%)
6
Grain boundaries with (1012) – (0112) extension
double twin relationship (%)
18
Grain boundaries with <1010> rotation axis (%)
41
Grain boundaries with <1120> rotation axis (%)
23
Grain boundaries with <1011> rotation axis (%)
12