
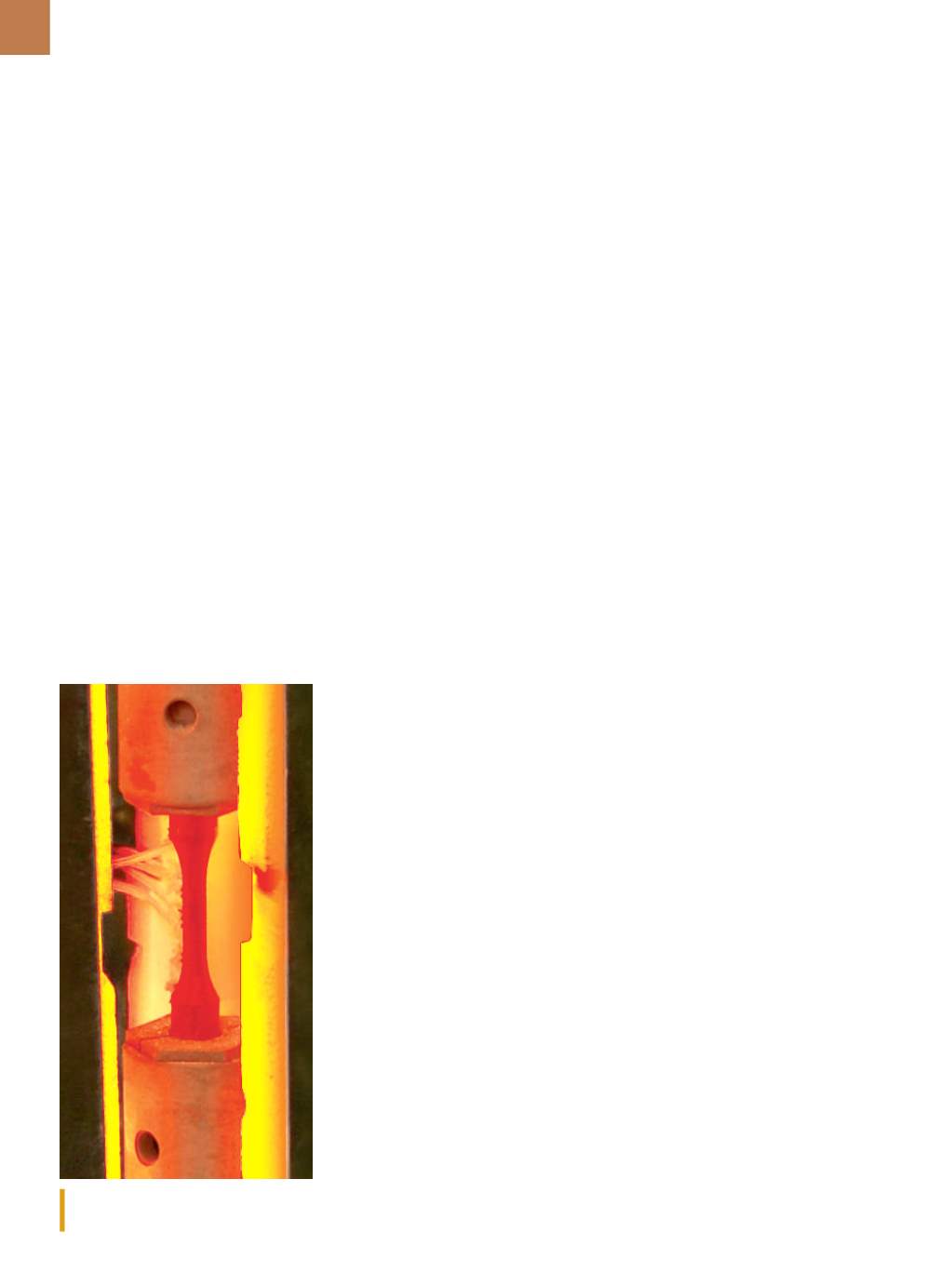
A D V A N C E D M A T E R I A L S & P R O C E S S E S | J U N E 2 0 1 6
1 8
in real-time. But this approach also has
challenges. A light inside the chamber
is necessary to illuminate the specimen
for the camera. At some temperatures,
the specimen’s illumination (or black-
body radiation) reduces the contrast and
accuracy of the video extensometry. To
address this, a method was developed
that uses blue LEDs to illuminate the
chamber in concert with optical filtering,
which minimizes blackbody effects and
enhances contrast.
IN-SERVICE MATERIALS
CHALLENGES
Testing a material that has been
in service adds even more complexity
because it is often impossible to obtain
a large enough portion of the material
to make a round metallic specimen.
These
sub-sized
specimens challenge
gripping technologies as well as heat-
ing and sensing technologies.
Sometimes
researchers
must
extract a small specimen from a larger
component—specifically, turbine blades
from jet engines. The blades that see
the hottest application temperatures
are grown from single crystal seeds with
cooling holes to let air through. These
intricately shaped blades do not have
enough bulk to create a round speci-
men. When the interdendritic spacing of
a single crystal is similar to the specimen
dimensions, the specimen might act
quite differently than a bulk, round sam-
ple, and hence the sub-sized specimen
may better represent service reality.
TRADEOFFS VARY WITH
TEMPERATURE
These tradeoffs change consid-
erably within each of the three tem-
perature ranges for PMCs, metals,
and CMCs. For example, grips that are
the same temperature as the speci-
men are recommended for most high-
temperature applications. But the CMC
range exceeds 1000°C—the upper limit
for traditional metal grips—and would
cause the grips to lose strength. Ideally,
researchers want the grip to be as close
as possible to the specimen temperature
to minimize the specimen’s thermal gra-
dient, but not so hot that the grip itself
starts to get soft and lose strength.
If a specimen is long enough, cold
grips at ambient temperature could be
usedoutside the furnace. But some spec-
imens cannot be made long enough, for
the same reasons that they cannot be
made round. Even if cold grips could be
used, they would introduce temperature
gradients in the specimen, making more
tests necessary due to test data varia-
tions caused by the gradients. This adds
considerable expense to the process.
Dealing with the hottest tempera-
ture range presents some of the most
complex tradeoffs, because testing
is often done at temperatures hotter
than gripping materials can withstand.
For these applications, a grip that is
actively cooled in two different ways,
depending on the required tempera-
ture range, was developed.
Both kinds of grip cooling tech-
niques work according to the same con-
cept, in which the grip is positioned in
an area of the furnace that is relatively
less hot than the center zone where the
specimen resides. Multi-zone furnaces,
while slightly less cost effective, achieve
better results because gradients in the
specimen are minimized. If the center
zone is 1200°C, for example, the top and
bottom zones are closer to 1000°C. With
active, localized cooling, the grip can stay
in the less-hot part of the furnace and still
hold the specimen in place while mini-
mizing thermal gradient. For testingmet-
als up to 1200°C, a grip that ismoderately
cooledwas developedwhile a grip that is
more aggressively cooled was developed
for testing CMCs up to 1500°C.
INTEGRATION IMPORTANCE
These examples illustrate the
importance of understanding the entire
test system (heating, gripping, and
sensing) and its interdependencies
fromback to front. Today, very few com-
mercial off-the-shelf solutions exist for
high-temperature materials testing. As
a result, many test labs attempt to build
these solutions in-house by assembling
components from different providers.
But as illustrated, the challenge is that
the tradeoffs require a system-level
approach for best results.
In other words, even a contact
extensometry expert may not under-
stand how to make their product work
through a window or inside a chamber.
Grip experts may be able to make cold
grips work in a cost-effective manner,
but the specimen gradient becomes
so large that it calls the test results
into question and conversely, hot grips
might work well for one type of test (i.e.,
tensile) but might be unusable or fail
prematurely for different loading condi-
tions (i.e., fatigue).
When grips are the same tem-
perature as the specimen, the result-
ing environmental chamber might
require unique solutions for sensing
specimen deformation. The ability to
integrate the entire solution is vital.
Systems integration expertise is valu-
able for innovative high-temperature
testing because it reduces data vari-
ability and allows researchers to run
fewer tests in order to achieve accu-
rate results.
~AM&P
For more information:
Erik Schwarz-
kopf is staff scientist, MTS Systems
Corp., 14000 Technology Dr., Eden Prai-
rie, MN, 55344,
erik.schwarzkopf@mts.
com, www.mts.com.
Thermocouples bonded to the specimen
are used to measure thermal gradients.