
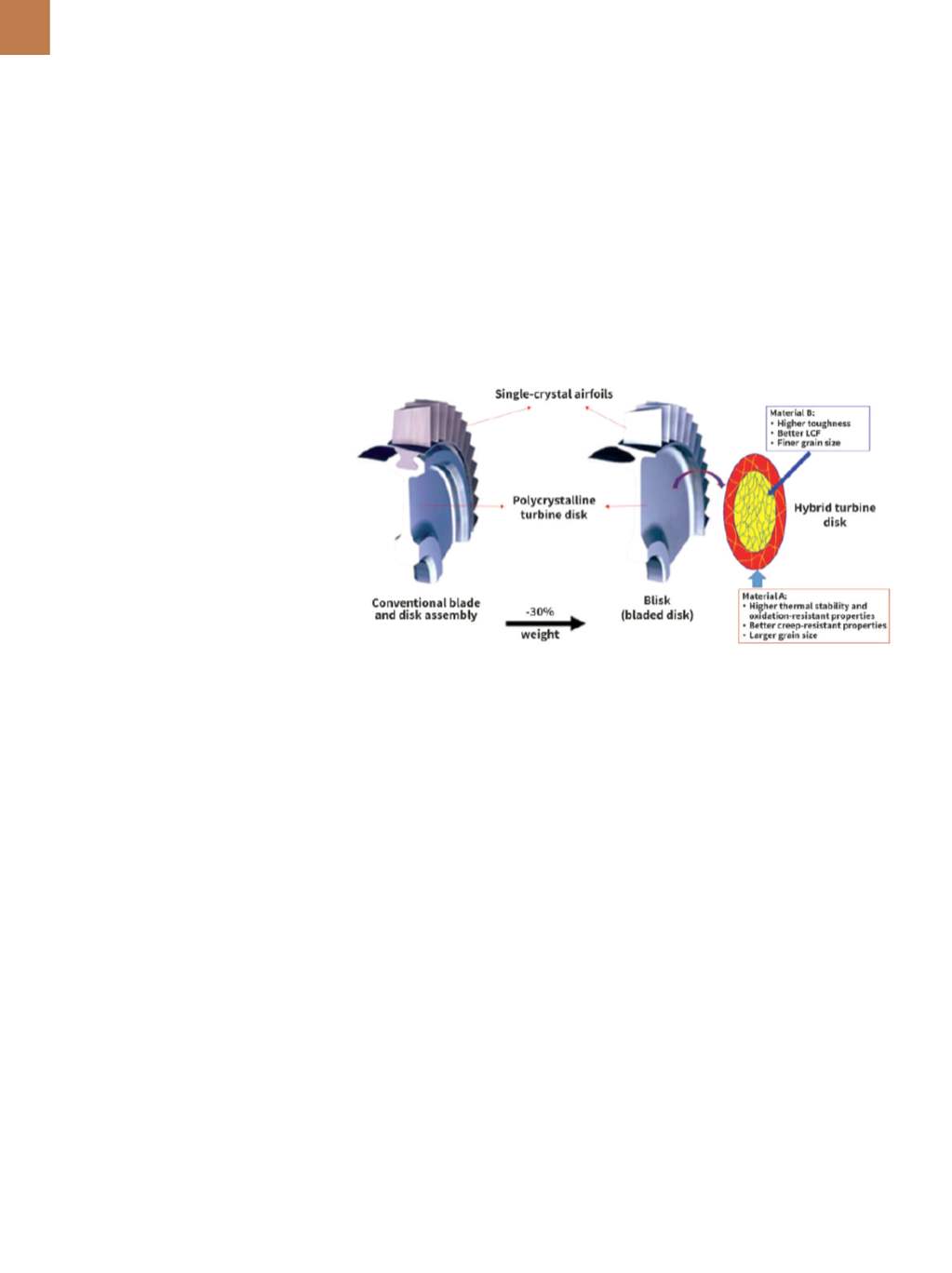
A D V A N C E D M A T E R I A L S & P R O C E S S E S | J U N E 2 0 1 6
2 2
FIELD ASSISTED SINTERING
TECHNOLOGY UPDATE—PART II
Field assisted sintering technology (FAST) enables hybrid components for aerospace
to be designed with reduced weight
—
without sacrificing performance.
Jogender Singh, FASM, Pennsylvania State University, University Park
Chris Haines, U.S. Army RDECOM-ARDEC, Picatinny Arsenal, N.J.
T
echnological benefits of field
assisted sintering technology
(FAST) compared with conven-
tional processes include: high flexibil-
ity; 100 to 1000 times faster processing
cycle, which significantly reduces man-
ufacturing costs; retention of a sub-
micron grain microstructure, which pro-
vides superior component properties;
achieving 100% density; and signifi-
cant energy savings of 60 to 70%. The
technology enables engineering of new
materials and designing and develop-
ing prototype components with salient
features not economically feasible using
conventional manufacturing methods.
Part I of this article (February 2016
AM&P
) discussed the use of FAST to pro-
duce thermally managed components
and net-shape Ti-alloy and refractory
material components. Part II discusses
using FAST to design lightweight hybrid
components for the aerospace industry
without sacrificing the performance of
traditional components.
LIGHTWEIGHTING
AEROENGINE COMPONENTS
A major goal in the manufacture of
modern aeroengine gas turbines is dou-
bling the thrust-to-weight ratio of the
engine, which is achievable by reduc-
ing the weight of turbine components
and increasing the speed of rotating
components. Single-crystal nickel-base
superalloy blades are attached to a
superalloy disk using a
fir-tree
blade-to-
disk arrangement—known convention-
allyasabladeanddiskassembly. Joining
single crystal blades to a polycrystalline
disk (called blisks) requires significantly
less material because the weight of
blade roots, disk lugs, and the disk struc-
ture required to support these features
is eliminated (Fig. 1). This results in a
weight savings of up to 30%, enabling
higher blade speeds, and thus a higher
pressure ratio per stage.
Linear friction welding (LFW) is
used to manufacture polycrystalline
titanium blisks, where the materials
are easily deformed. However, using
LFW to join single crystal blades and
polycrystalline Ni-base superalloys is
challenging because the single crystal
is difficult to deform. Also, some char-
acteristics of LFW including localized
melting, heat-affected zones, material
deformation, andmicro-cracks near the
interface can be problematic. In addi-
tion, residual stresses and large grain
size near the interface can contribute to
catastrophic failure.
NASA
developed
low-density,
single-crystal (LDS) nickel-base super-
alloys for turbine blade applications,
which offer significant improvements
in the thrust-to-weight ratio. To take
advantage of potential weight sav-
ings, researchers looked at joining LDS
Ni-base superalloys via FAST. Materials
were joined to each other at the Applied
Research Laboratory Penn State Uni-
versity. A cross section of the interface
(Fig. 2) shows what appears to be per-
fect bonding.
Nickel-base superalloys intended
for advanced disk applications require
high creep resistance and dwell crack
growth resistance in the rim region
to withstand temperatures exceeding
650°C and high strength and fatigue
resistance in the bore and web regions,
which operate at temperatures of 500°C
or less. Strength-dependent proper-
ties of a disk with a uniform coarse
Fig. 1 —
Bladed-disk (blisk) structure offers significantly reduced weight compared with a con-
ventional blade and disk assembly.