
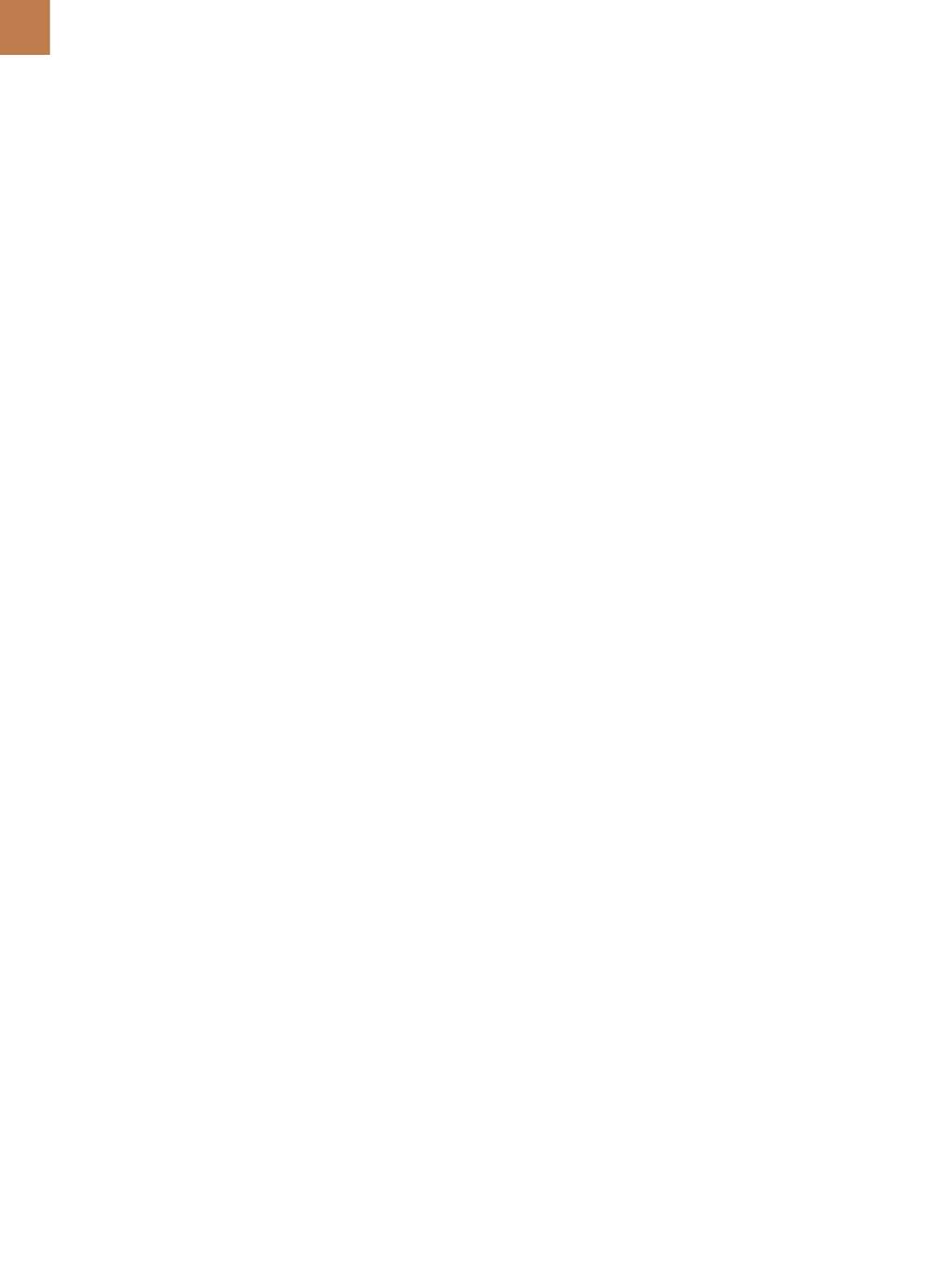
A D V A N C E D M A T E R I A L S & P R O C E S S E S | J A N U A R Y 2 0 1 6
3 0
NEWPROCESS JOINSNITINOL
TOSTAINLESS STEEL
A new solid-state joining process for medical guidewire applications
increases joint strength, provides superior bending properties,
and does not require tertiary metals or ferrules.
Pankaj Gupta,* Arne Rimmereide, and Roger Dickenson, Lake Region Medical, Chaska, Minn.
A
guidewire isamedical deviceused
in various minimally invasive vas-
cular applications. Its foundation
is a metal core wire, typically constructed
of stainless steel or Nitinol. A metal coil,
polymer jacket, or combination of the
two covers the core wire on the distal end
in order to make the tip atraumatic, kink
resistant, and flexible.
Designing a guidewire is an in-
tricate exercise in balancing strength
and flexibility. For example, a guide-
wire with a spring-tempered stainless
steel core has good pushability and
torque transmission due to its high yield
strength and Young’s modulus. These
properties are important in order to nav-
igate to the desired treatment sites and
deliver the desired clinical therapy. How-
ever, exceeding the yield strength of the
material in a bending mode results in
permanent bends and kinks, which se-
verely reduces guidewire performance.
Nitinol is a superelastic material pro-
viding great kink resistance, but it lacks
pushability due to an inherently lower
Young’s modulus, which results in less
support in delivering therapies or devic-
es. Ideally, a guidewire core combines
the excellent mechanical properties of
stainless steel in the main body, with the
kink resistance of Nitinol at the distal tip.
A bimetal medical guidewire with
a stainless steel proximal section and
Nitinol distal section enhances perfor-
mance compared to guidewires made
of either alloy alone. However, standard
fusion welding of Nitinol (NiTi) to stain-
less steel (SS) is challenging because it
causes brittle intermetallic Fe-Ti to form,
leading to unpredictable brittle joints. To
avoid this, current joining methods use
either a transition section made of a ter-
tiary metal or a ferrule joining process.
JOINING OPTIONS
Metallurgically, joining Nitinol
to stainless steel via fusion welding is
problematic due to the formation of
brittle Fe-Ti intermetallics
[1,2]
, as pre-
viously mentioned. One method of
avoiding brittle intermetallics is to use
a tertiary metal, such as Nickel, when
joining the stainless steel to Nitinol
[3]
,
but this adds cost and complexity to the
design and can degrade performance.
Solid-state processes such as fric-
tion welding
[4]
, explosive welding
[5]
, and
ultrasonic welding
[6]
can also be used
to join dissimilar metals while avoiding
the formation of brittle intermetallics
in the joint. Another method used in
guidewire applications is to insert the
ends of the stainless steel and Nitinol
into a ferrule (a section of hypotube)
and then secure both ends using ad-
hesive or solder. This method requires
preprocessing to reduce the diameter
at the ends of each core in order to fit
the parts together, which adds cost
and complexity. Further, this decrease
in core diameter, along with the stiffer
section of hypotube, and the addition
of joint material, creates a kink point
and reduces clinical performance.
An alternative proprietary solid-
state butt joining process for Nitinol and
stainless steel wires ranging in diame-
ter from 0.013 to 0.020 in. that does not
require tertiary metals or ferrules was
developed by researchers at Lake Re-
gion Medical (LRM). The resulting joint
strength is approximately 80%of the ten-
sile strength of the raw Nitinol wire with
excellent bending properties. Complete
0.014-in. outer diameter guidewires were
built using solid-state weld technology,
tested, and compared to a competitor’s
product with a hypotube joint design.
The solid-state weld joint’s metallurgical
characteristics aswell as data fromguide-
wire functional tests are presented here.
EXPERIMENTAL PROCEDURES
Solid-state weld joints were creat-
ed using pre-straightened superelastic
binaryNitinol (54.5%-57.0%Ni) and 304v
spring-tempered stainless steel wires
with subsequent evaluation of joint
strength, durability, and microstructure.
Parts went through preconditioning
by cycling the joint 10 times through a
U-bend fixture with a 0.10-in. radius, pri-
or to obtaining tensile strength data by
pulling the joint to failure using an MTS
testing system. Joint microstructures
were examined using standard metallo-
graphic methods of polishing and etch-
ing the longitudinal joint sections. In
addition, optical microscopy and scan-
ning electron microscopy (SEM) con-
firmed overall joint quality. Energy dis-
persive spectroscopy (EDS) analysis on
the cross-section determined the weld
zone length with intermixed Nitinol and
stainless steel.
A grinding study was conduct-
ed on the solid-state welded bimetal
joints using 0.018-in. stainless steel to
0.020-in. Nitinol wires. This allowed
*Member of ASM International; now at St. Jude Medical