
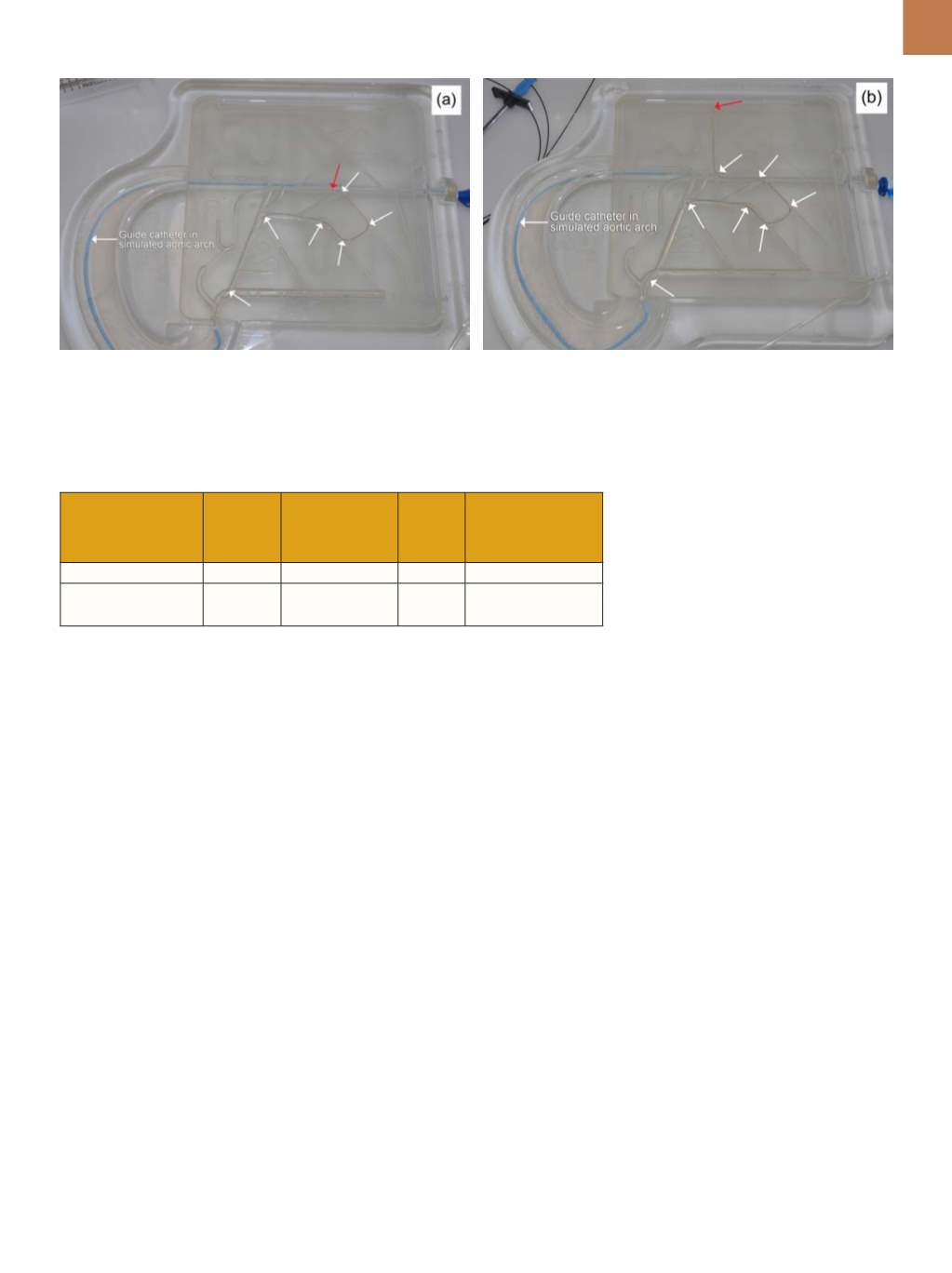
A D V A N C E D
M A T E R I A L S
&
P R O C E S S E S | J A N U A R Y
2 0 1 6
3 3
TABLE 1—TENSILE DATA SUMMARY FOR 0.014-IN. DIAMETER
SOLID-STATE WELDED GUIDEWIRES
Sample ID Sample
quantity
Break load
(Std. dev.), lb
% of
NiTi
break
load*
Failure location
LRM seamless joint
5
28.6 (0.72)
89
Joint interface
Hypotube joint
5
5.1 (0.35)
16
NiTi wire attached
to NiTi hypotube
*NiTi wire tensile strength for 0.014-in. NiTi wire was roughly 32 lb.
Fig. 6 —
Testing of LRM full guidewire 0.014-in. diameter in 2D plate model. Hypotube joint (a)
and LRM solid-state weld joint (b).
on the Nitinol wire, typical of a ductile
fracture mode, Fig. 5(d).
Figure 6 shows the two wires in
simulated performance testing using a
2D plate model, which features several
channels simulating tortuous vessels.
The wire is inserted through a guide
catheter (Vistabrite tip JL4 Fr manu-
factured by Cordis) into a predeter-
mined pathway to assess wire tracking
and torque response. The guidewire
with the LRM solid-state weld tracked
much further into the pathway than the
guidewire hypotube joint. Red arrows
indicate the distal-most position that
each wire navigated.
CONCLUSIONS
Nitinol wire was joined to stainless
steel wire via a proprietary solid-state
process without the use of filler materi-
al. This process proves to be a superior
method to create joints between dis-
similar metals such as stainless steel
and Nitinol. It offers significant perfor-
mance enhancements for guidewire
applications by merging a high-stiffness
stainless steel body for pushability with
a softer, more kink resistant Nitinol for
the distal section. The solid-state weld
process yields a fine-grained HAZ and
defect-free interface, resulting in excel-
lent bend and tensile properties at the
joint.
Initial performance testing using
a 2D plate model simulating vascula-
ture indicates that the LRM solid-state
weld offers superior performance in
clinical application compared to one
of the leading bimetal guidewires on
the market.
~AM&P
For more information:
Arne Rim-
mereide is manager of R&D, Lake Re-
gion Medical, 340 Lake Hazeltine Dr.,
Chaska, MN 55318, 952.641.8383,
arne. rimmereide@lakeregionmedical.com,
www.lakeregionmedical.com.
References
1. J. Pouquet, et al., Dissimilar Laser
Welding of NiTi to Stainless Steel,
Int. J.
Adv. Manuf. Technol.
, Vol 61, p 205-212,
2012.
2. P. Vondrous, L. Kolarik ,and M.
Kolarikova, Plasma Arc Welding of NiTi
and 304 Steel,
Annals of & Proceedings
of DAAAM Intl.
, Vol 23:1, p 2304-1382,
2012.
3. H.M. Li, et al., Laser Welding of TiNi
Shape Memory Alloy and Stainless
Steel Using Ni Interlayer,
Materials &
Design,
Vol 39, p 285-293, 2012.
4. S.D. Meshram, T. Mohandas, and G.M.
Reddy, Friction Welding of Dissimilar
Pure Metals,
J. Mat. Proc. Tech,
Vol 184,
p 330-337, 2007.
5. N. Kahraman, B. Gulenc, and F. Find-
ik, Joining of Titanium/Stainless Steel
by Explosive Welding and Effect on
Interface,
J. Mat. Processing Technol.,
Vol 169, p 127-133, 2005.
6. J. Tsujino, et al., Ultrasonic Butt
Welding of Aluminum, Aluminum Alloy
and Stainless Steel Plate Specimens,
Ultrasonics,
Vol 40, p 371-374, 2002.
7. A. Rajasekhar, Effect of Welding Pro-
cess and Post Weld Heat Treatments on
Microstructure and Mechanical Prop-
erties of AISI 431 Martensitic Stainless
Steel,
Int. J. Tech. Research and Appl.,
Vol 3, p 280-285, 2015.