
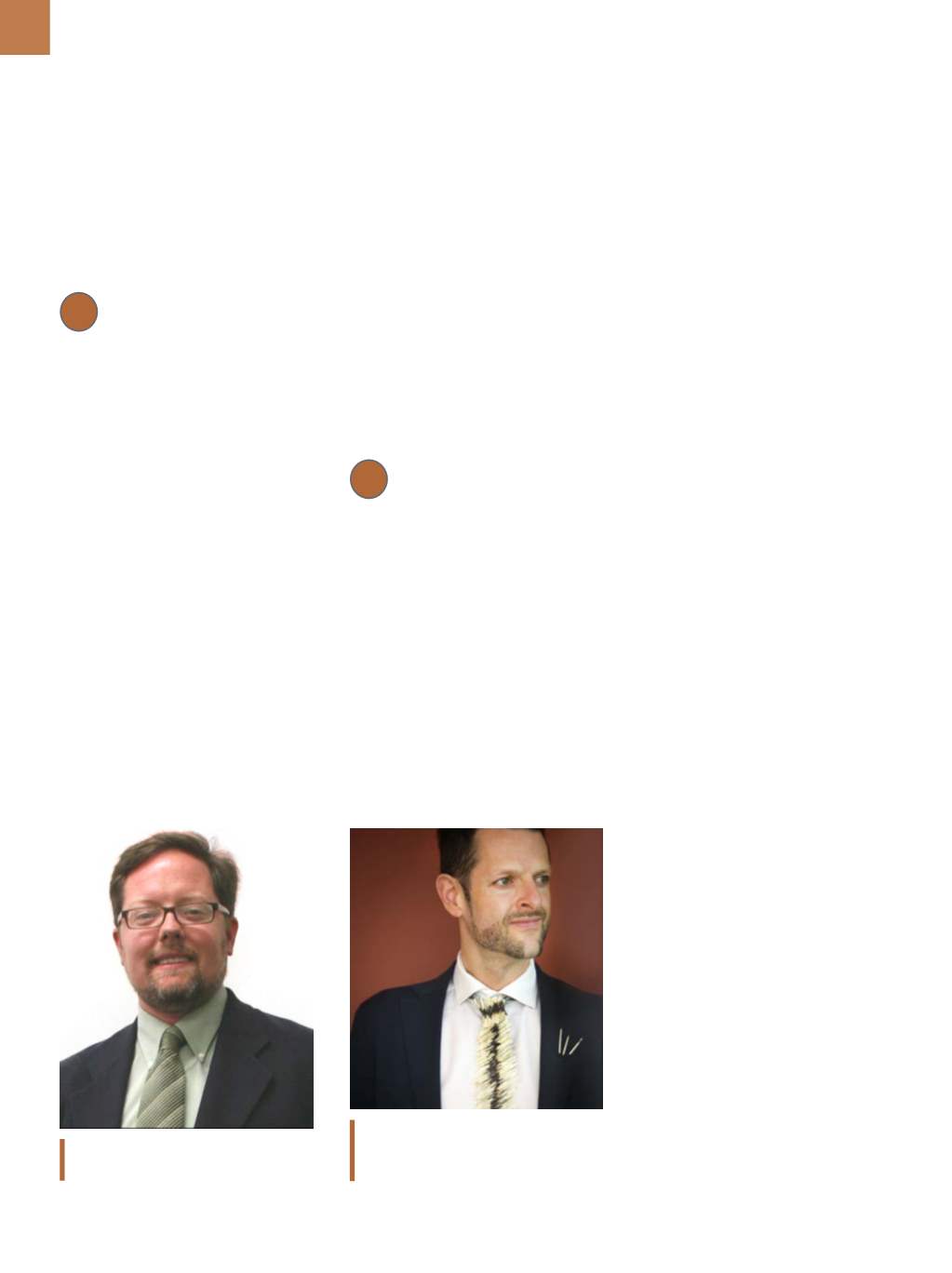
A D V A N C E D M A T E R I A L S & P R O C E S S E S | N O V E M B E R / D E C E M B E R 2 0 1 5
2 4
components, which he calls fuses, with-
in steel structures to absorb energy
caused by a major event in a way sim-
ilar to how shock absorbers prevent
damage in cars.
“In civil engineering research, the
whole realmof newmaterials is some of
the most important and exciting work
ever experienced in the field, and will
be for many years to come,” says Hajjar.
4
LIGAMENT REPAIR
At Northeastern University’s de-
partment of chemical engineering,
mechanical testing is essential in
developing better materials for liga-
ment repair. In biomedical polymer
research, this typically involves simu-
lating conditions in the human body
such as the real-life movement of ten-
dons and tissues in a wet test environ-
ment. For example, the department
uses a micro-test system to measure
mechanical properties of miniature
samples and is able to measure very
low forces and small displacements.
The system also records microscopic
material behavior while the sample is
subjected to forces such as in charac-
terizing viscoelasticity properties.
In addition to ligament repair re-
search, faculty and students also focus
on hydrogels development, a material
popular in tissue engineering given its
potential to mimic the body. “We use
our test system to pretend we are in-
jecting the hydrogel into bone or oth-
er tissues,” says Tom Webster, chair of
the chemical engineering department.
“Once the hydrogel solidifies, we test
the interface between it and the natural
tissue.”
If the interface is bad, a crack will
begin and failure will occur. If the inter-
face is good, it will withstand a lot of
force. The university is testing applica-
tions including injecting into bone, lig-
aments, and the heart to heal damaged
tissue and rebuild healthy heart tissue.
“The future of mechanical testing is
to tell us how new materials behave,”
says Webster. “The world needs better
materials.”
5
IMPROVED MEDICAL
ADHESIVES
Researchers at the Harvard-MIT
Laboratory of AcceleratedMedical Inno-
vation at Brigham and Women’s Hospi-
tal believe that innovation occurs at the
interface of disciplines. “The constant is
that we focus on solving medical prob-
lems and we constantly test our solu-
tions in multiple models,” says director
Jeffrey Karp. Getting every solution to a
human testing phase as efficiently and
quickly as possible is what gives the lab
its sense of urgency.
The lab is working on how to
reduce injuries to the fragile skin of
premature newborn babies when the
adhesives holding the medical mon-
itoring devices are removed. Lab re-
searchers designed an adhesive with
a middle thin layer of silicone etched
in spider web inspired patterns that
enables quick and painless release. To
conduct proof of concept tests, Karp
used an adhesive testing system for
standard peel and shear tests, and
added an innovative non-machine
approach: Researchers tested the ad-
hesive on origami paper to simulate
fragile skin.
The first priority of testing is to
understand the most critical point of
failure. “If we use mechanical testers
in labs, we can fail fast,” Karp explains.
He adds that testing can help acceler-
ate the iterative process of innovation.
With regard to the lab’s work on devel-
oping adhesive tissue that will attach
to the heart, Karp explains the testing
challenges. “We need to understand
this environment and the extension,
compression, and force that our mate-
rial will be up against. How often will
it be extending? How does the mate-
rial change as it degrades?” he asks.
The liquid adhesive is known as HLAA
(hydrophobic light-activated adhe-
sive), which features a combination
of qualities that enable it to adhere to
a constantly beating—and therefore
moving—heart in the body’s wet envi-
ronment, and to biodegrade during the
healing process.
Other innovations the lab has
developed using its accelerated pro-
cesses include a micro-needle based
adhesive that results in minimal tissue
damage. The needle’s cone-like struc-
ture enables easy insertion into skin
and locks into place as the tip swells
from absorbing water in the body. Re-
searchers in the lab tested the adhe-
sive properties of the micro-needles
and conducted tensile and force pull-
out tests.
~AM&P
For more information:
Rich Gedney is
CEO of Admet Inc., 51 Morgan Dr., Nor-
wood, MA 02062, 781.769.0850,
sales@ admet.com,
www.admet.com.
TomWebster, chemical engineering de-
partment chair, Northeastern University.
Jeffrey Karp, director, Harvard-MIT Labo-
ratory of Accelerated Medical Innovation
at Brigham and Women’s Hospital.