
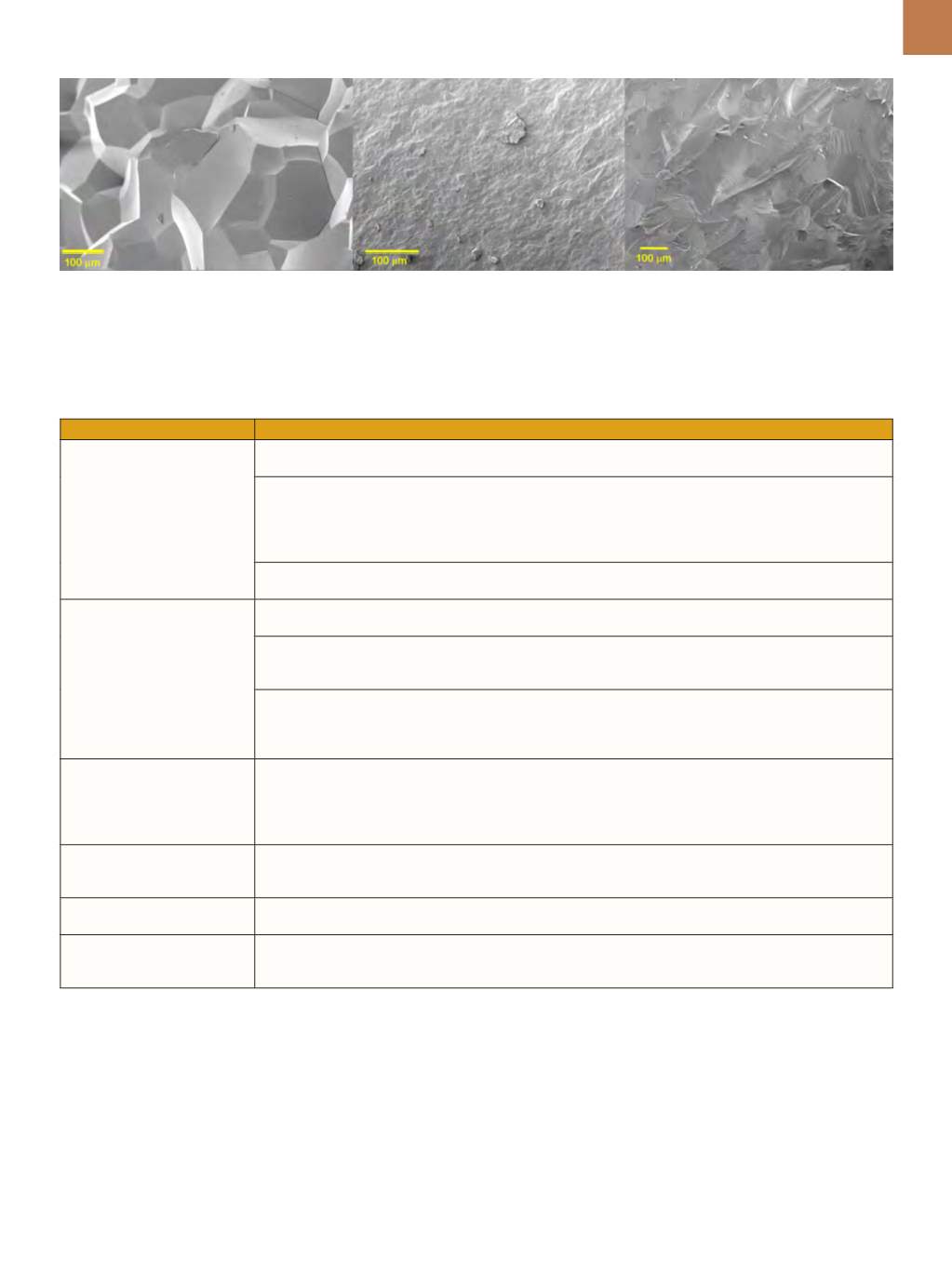
A D V A N C E D
M A T E R I A L S
&
P R O C E S S E S |
N O V E M B E R / D E C E M B E R
2 0 1 5
2 7
TABLE 2—PROPERTIES AND APPLICATIONS FOR ALON AND SPINEL
Featured Properties
Applications
Mechanical:
• Hardness
• Strength
• Durability
Transparent armor systems for ground vehicles and aircraft:
ALON provides superior ballistic
performance against multiple advanced threats such as 50-caliber armor-piercing bullets.
Durable windows:
Because ALON is the hardest polycrystalline transparent material, it offers
significant environmental durability (rain and sand erosion resistance) and scratch resistance.
Common applications include windows for laser communications (airborne laser data links,
counter manpads, laser rangefinders, laser target designators, laser radars), protective
covers for sensors, pressure vessels, and laser igniter windows.
Windows/covers for harsh environments:
Oil and gas drilling, scratch-resistant
covers for electronic devices, and windows on chemical reactors.
Optical:
• Highly transparent
• Visible midwave infrared
transmission
• High Abbé number/
low dispersion
Domes for infrared optics:
Hemispherical and hyper-hemispherical domes for infrared guided
missile systems, reconnaissance and sensor windows, and lenses for targeting pods.
Reconnaissance and sensor windows:
ALON offers the highest refractive index
homogeneity over large areas, a key requirement for sensor and reconnaissance
applications. ALON windows are now in use on various helicopters and aircraft.
Night vision systems:
In addition to its mechanical performance, ALON’s higher transmittance in the
0.6 to 1 micron wavelength range offers significant night vision advantages over glass-based systems.
Gradient index optics (GRIN):
ALON GRIN optics have low chromatic aberrations (due to low
dispersion) and GRIN lenses are possible with
Δ
n of >0.05 (axially and radially).
Processability:
Powder processing allows
manufacturing of complex
geometries, embedded
features, and large sizes
Large monolithic transparent armor, large area optics, and curved/conformal optics:
Unlike single crystal, which is melt-based and grown as a boule and then fabricated into a shape,
ALON and Spinel are made from powder and hence can be made into very large sizes and
to near-net complex geometries. This enables applications such as large
monolithic transparent armor windows in flat as well as conformal shapes.
Chemical resistance (ALON):
• To acids and bases
• To halogen plasma
Tools and components for harsh environments:
Examples include semiconductor equipment,
plasma etching chambers, reaction chambers, chemical reactors, and reaction vessels.
High temperature
resistance
Windows for furnaces and other equipment operating at elevated temperatures:
ALON has a
melting point of >2000°C and can withstand temperatures of roughly 1500°C in inert atmospheres.
Biocompatibility
Bio-ceramics such as load-bearing prosthetic implants and components of diagnostic tools
and equipment:
ALON is nontoxic and has been shown to have both in-vitro and in-vivo
biocompatibility, as well as outstanding wear resistance and low coefficient of friction.
Fig. 4 —
Typical SEMmicrographs: (a) Spinel processed using the LiF-based hot pressing approach; (b) Surmet’s Spinel; and (c) Surmet’s ALON
produced via solid-state pressureless sinter followed by HIP.
yields. In addition to these powder
issues, densification of Spinel green
bodies is still plagued by unpredictable
chemistry and complex diffusion mech-
anisms and requires further lab studies.
Two main techniques exist for
making fully dense and transparent
Spinel. The most widely used approach
is vacuum hot pressing, where powder
is typically blended with lithium flu-
oride (LiF) as a liquid phase sintering
aid followed by uniaxial pressing at el-
evated temperatures. LiF melts at rel-
atively low temperatures and forms a
eutectic composition, which then wets
and reacts with Spinel grains, result-
ing in liquid-phase assisted densifica-
tion. LiF is highly volatile and ideally
should evaporate at or below the hot
pressing temperature regime of Spinel
(roughly 1600°–1700°C). However, a
sufficient amount of LiF remains at the
grain boundaries, resulting in severe
grain-boundary embrittlement and
intergranular weakness
[4]
. Weak grain
boundaries are depicted in Fig. 4(a),
a scanning electron micrograph of a
(a)
(b)
(c)