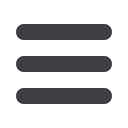
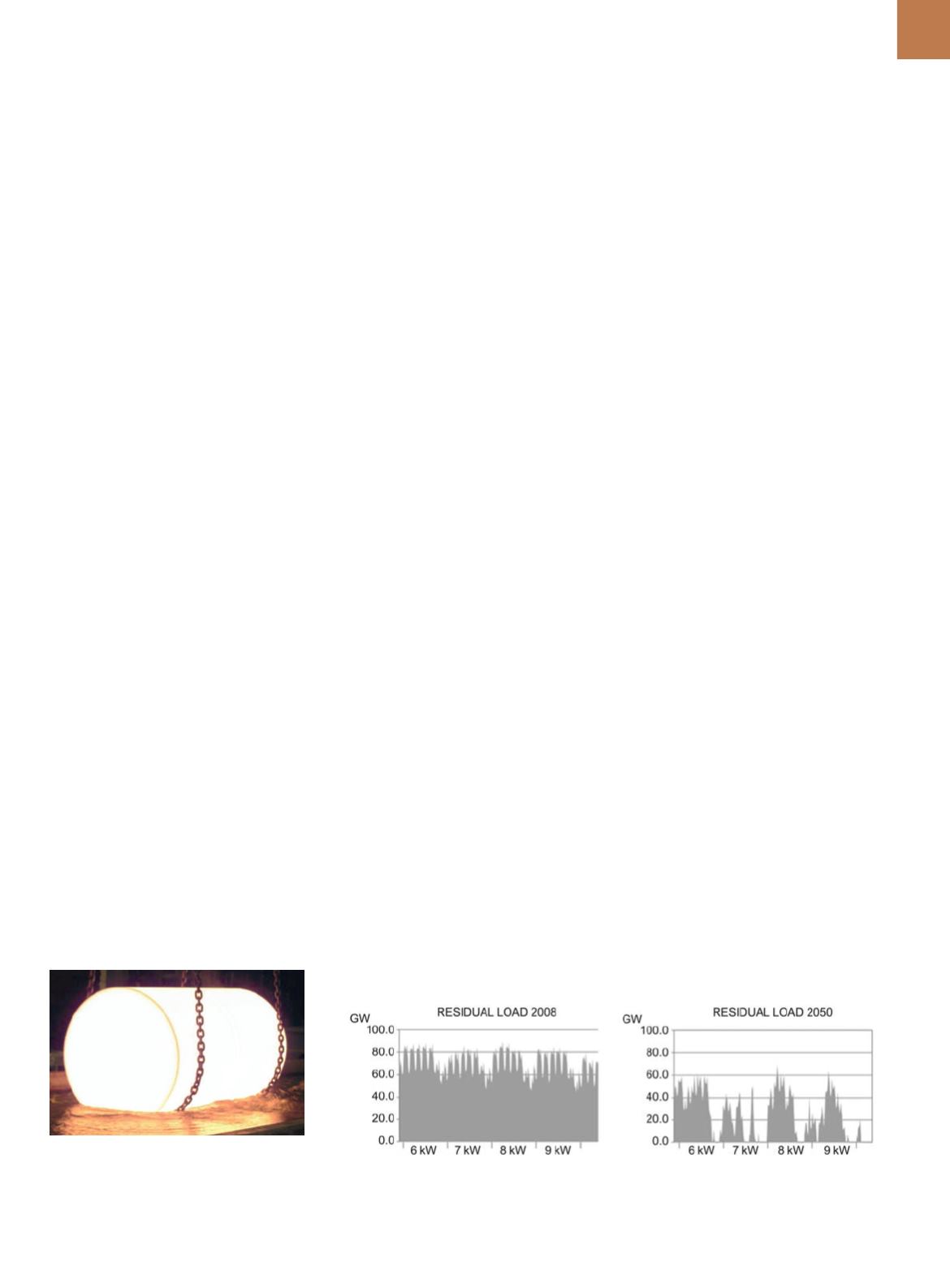
A D V A N C E D
M A T E R I A L S
&
P R O C E S S E S |
M A R C H
2 0 1 5
2 5
long-term creep testing of weldments
to confirm improved heat-affected zone
(HAZ) creep strength, while forging and
tubing production for in-plant testing
and cast MARBN steel and subsequent
testing are also being developed.
Overall, efforts were impressively
coordinated among the various par-
ties involved, including partners from
academia, research institutions, manu-
facturers, and utilities. From the stand-
point of steam power plant technology,
Europeans were the first to develop
and demonstrate materials for a 700°C
power plant, with U.S. and Japanese
programs developing materials for tem-
peratures up to 760°C later. EU efforts
in both >750°C steam operation and
incremental improvements to steels
for operation at 650°C, presented at the
conference, demonstrate broad global
competitiveness in this technology area.
CREEP-FATIGUE
One key development discussed
extensively is the need for flexible op-
eration of conventional power plants.
This recent flexibility requirement is
largely due to the mandate to supply a
larger fraction of power from renewable
sources. For example, the total pow-
er generated from renewable sources
in Germany increased threefold over
the past 10 years, and is expected to
continue. The residual load character-
istic (difference between total electric
energy consumption and supply by
renewable sources) of a time period in
2008 compared to the same projected
time period in 2050 is shown in Fig. 2.
The loading spectrum of power plants
will change dramatically in the coming
years, a process that has already begun.
The changing operation mode of
conventional power plants has created
the need for improved tools that can
predict creep-fatigue damage interac-
tion in materials. Organizations such
as the Electric Power Research Institute
(U.S.) and VGB (Germany) have formed
working groups to standardize testing,
analysis, and design procedures associ-
ated with creep-fatigue damage. A sim-
ple example illustrating these changing
requirements is one associated with
thick-walled components—going to
thicker sections to alleviate creep dam-
age can have a negative influence on
the component’s thermal fatigue life-
time. At least two analysis procedures
to quantify creep-fatigue damage were
presented at the conference, one in-
volving creep-fatigue damage summa-
tion diagrams and the other focused on
fracture-mechanics-based cyclic crack
tip opening displacement parameters.
Creep-fatigue damage assessment
tools must be developed in parallel
with higher performance materials with
improved creep-fatigue resistance. For
power plant steels, creep-fatigue dam-
age development is reported to be in-
fluenced by the temperature and strain
range, strain rate, hold time, creep
strength, and creep ductility of the ma-
terial. The traditional understanding of
creep-fatigue interactions is based on
studies of low alloy ferritic and austen-
itic steels. However, this understanding
may not translate well to new advanced
materials with significantly different
deformation and oxidation responses.
For example, for 9% to 11% Cr
steels at temperatures above 525°C, the
dominant source of damage accumula-
tion comes from fatigue-oxidation rather
turbine rotors, and steam turbine cas-
ing, with a focus on nickel-base alloy
263. The project is coordinated by DNV-
GL, with Doosan Babcock leading the
boiler effort, Skoda Power leading the
steam turbine work, and DNV-GL inte-
grating the practical results with mod-
eling efforts. Major activities include
fireside corrosion testing using boiler
probes; laboratory work to understand
and model fireside corrosion and steam
oxidation; optimization of nickel-base
alloy 263; forging trials up to 1000 mm
in diameter on alloy 263 (Fig. 1); demon-
stration of rotor welding; and casting
development, including development
of a new nickel-base casting (G130 by
Goodwin) for heavy sections.
To improve coordinationof the var-
ious multinational programs funded by
the European Union (EU) with national
government programs, a special Ener-
gy Materials working group (WG2) was
formed as part of the Knowledge-Based
Multifunctional Materials Virtual Insti-
tute in 2012. One goal of this program is
addressing the materials gap between
the current 600°C steel technologies for
fossil power plants and the extensive
research taking place in Europe, the
U.S., and Japan on >700°C materials
technology. The group is currently co-
ordinating efforts for industrial scale
demonstrations using the Japanese
originated MARBN (martensitic micro-
structure with boron and nitrogen con-
trol) steel concept. MARBN steels con-
tain highly controlled levels of boron and
nitrogen, which are reported to increase
high-temperature long-term (>100,000
hours) creep strength of steels up to
650°C while helping retain good weld
strength. These steels are undergoing
Fig. 1 —
Full scale, 1000-mm-diameter alloy
263 rotor forging during solution annealing
and quenching. Courtesy of Saarschmiede,
Germany.
Fig. 2 —
Comparison of the residual load characteristic between 2008 and 2050 (projected),
illustrating the growing need for predictive tools in the creep-fatigue interaction regime and
higher performance materials with better creep-fatigue resistance
[1]
.