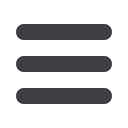
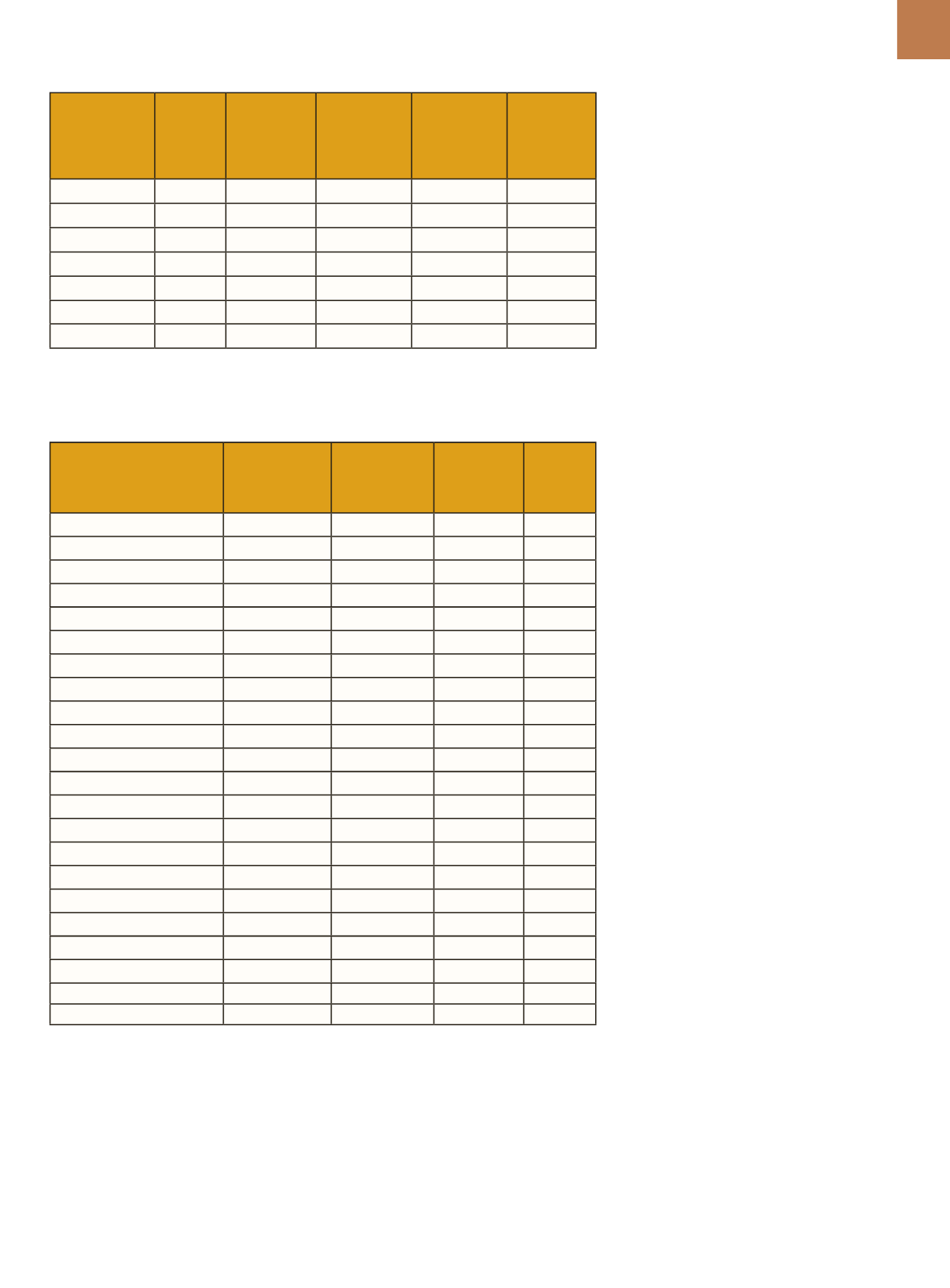
A D V A N C E D
M A T E R I A L S
&
P R O C E S S E S |
M A R C H
2 0 1 5
2 3
TABLE 2—MMLV WEIGHT REDUCTION ON A VEHICLE SUBSYSTEM BASIS
Vehicle
systems and
subsystems
2013
Ford
Fusion
weight,
kg
MMLV
weight,
kg
MMLV curb
weight, %
MMLV
weight
reduction,
kg
MMLV
weight
reduction,
%
1. Body
525.0
400.4
33.5% –124.6
–23.7%
2. Interior
260.4
202.7
17.0% –57.7
–22.2%
3. Chassis
355.0
260.0
21.8% –95.0
–26.8%
4. Powertrain 337.0
263.1
22.0% –73.9
–21.9%
5. Electrical
57.0
49.5
4.1%
–7.5
–13.1%
A. Assembly
25.0
19.5
1.6%
–5.5
–22.0%
Total vehicle
1559.4 1195.2
100% –364.2
–23.4%
Based on the system definition from the International Organization for Standardization
(ISO) standards.
TABLE 3—MAIN MATERIAL COMPOSITION PER VEHICLE ARCHITECTURE
Material
2013 Ford
Fusion
weight, kg
2013 Ford
Fusion
weight, %
MMLV
weight,
kg
MMLV
weight,
%
AHSS
417.5
27%
66.9
6%
Conventional steel
413.7
27%
289.8
24%
Cast iron
50.0
3%
19.6
2%
Forged iron
16.0
1%
10.0
1%
Stainless steel
19.1
1%
9.7
1%
Die-cast aluminum
146.4
9%
147.7
12%
Cold-rolled aluminum 12.8
1%
143.8
12%
Extruded aluminum
15.6
1%
66.9
6%
Forged aluminum
0.0
0%
9.8
1%
Magnesium
2.3
0%
16.0
1%
Copper
33.7
2%
29.3
2%
Titanium
0.0
0%
3.3
0%
CFRP
0.0
0%
54.2
5%
GFRP
0.0
0%
3.4
0%
Plastic
235.4
15%
177.1
15%
Rubber
72.6
5%
52.0
4%
Glass
37.5
2%
26.4
2%
Ceramics
0.8
0%
0.8
0%
Batteries
14.0
1%
8.0
1%
Paint
8.0
1%
7.7
1%
Fluid, adhesive, and other
64.1
4%
52.8
4%
Total vehicle
1559.5
100% 1195.2
100%
design. Completed testing to date in-
cludes a 150-K mile equivalent durabil-
ity test with no major structural issues
in the body, closure, chassis, interior, or
electrical systems. Safety testing for the
new car assessment program (NCAP)
full frontal crash, Insurance Institute
for Highway Safety (IIHS) 40% offset
deformable barrier, side pole impact,
and rear impact testing evaluates the
joining and energy absorption of light-
weight architecture. Safety test results
are complete and under review.
Select NVH (noise, vibration, and
harshness) testing measures the typi-
cally deleterious effects of lightweight-
ing on these vehicle attributes. NVH
data are also under review. Full vehicle
accelerated corrosion tests are under-
way on two MMLV vehicles. Many of
the technologies incorporated into the
MMLV are near term, but not necessar-
ily cost effective. Ford, Magna, and the
automotive industry continue to inves-
tigate innovative ways to incorporate
lightweight materials that are both cost
effective and affordable. Overall, this
concept vehicle is one of the most com-
prehensive studies of a multi-material
lightweight vehicle using technologies
that in the near future will contribute to
lightweight vehicles, better fuel econo-
my, and lower emissions.
~AMP
Acknowledgment
The authors thank their colleagues
in Ford Research & Advanced Engineer-
ing who assisted with the design and
research for the MMLV. Additionally
they thank their Magna partners for de-
sign and engineering efforts. More than
100 research scientists and engineers
contributed to this project. Finally, the
authors thank the U.S. Department of
Energy, Vehicle Technologies Office for
support and ongoing guidance and re-
views. This material is based on work
supported by the DOE National Energy
Technology Laboratory under Award
No. DE-EE0005574.
For more information:
Matthew Zalu-
zec is senior technical advisor, Ford
Motor Co., 2101 Village Rd., Dearborn,
MI 48121-2053, 313.337.1098,
mzaluzec @ford.com, www.ford.com.SUMMARY
The multi-material lightweight ve-
hicle design reduces the weight of a CD
class five-passenger sedan by more than
350 kg—a savings of over 23%. By design-
ingmajor structural systems usingmixed
materials, incorporating aluminum as
well as steel, and using lightweight ma-
terials in all major vehicle systems and
components, the MMLV design sets a
mark for vehicle weight reduction.
Future efforts will build and
test physical prototypes of the MMLV