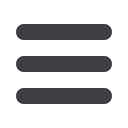
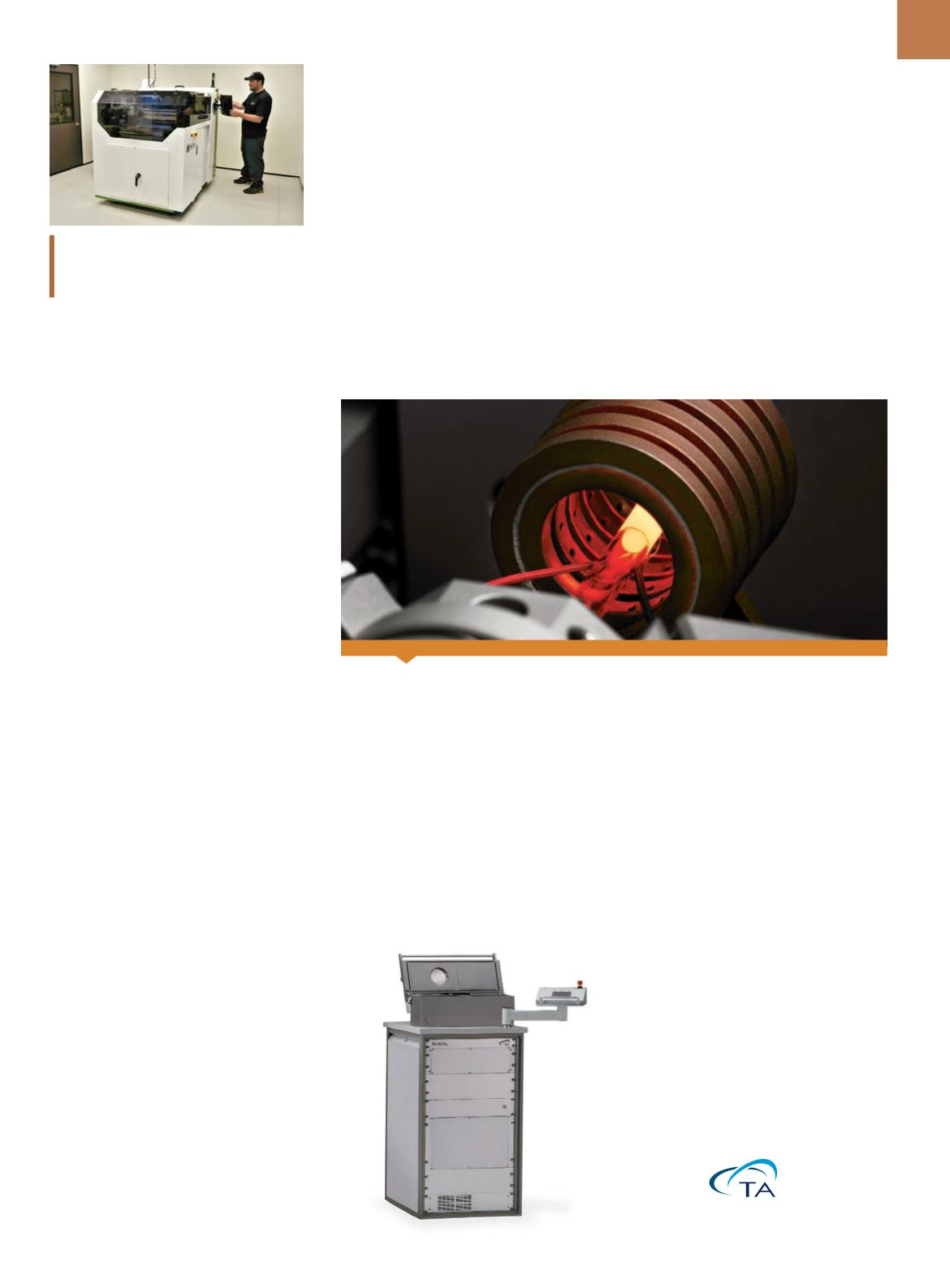
A D V A N C E D
M A T E R I A L S
&
P R O C E S S E S |
M A R C H
2 0 1 5
2 9
Finally, the heat source used to
melt the powder in order to fuse respec-
tive layers may transform the desirable
microstructure of the raw powder into
a less desirable, coarse microstructure.
Ongoing studies seek to understand
the extent of microstructure change in
various systems and its impact on final
component properties. The patented
family of eTi alloys from Puris, for ex-
ample, was developed to alleviate this
issue. Precipitates formed in-situ during
powder manufacturing pin grain bound-
aries and retard grain growth during all
subsequent processing. These alloys en-
able forged-quality microstructures and
properties in AM-produced parts, regard-
less of the process used. At the produc-
tion level, solutions vary by technology:
•
Laser-based and electron-beam
systems rely on processing param-
eters to facilitate rapid cooling and
minimize detrimental microstruc-
ture changes.
•
Binder-jet systems process at room
temperature with the option of not
reaching the material’s liquidus
during subsequent processing.
This preserves the desirable
microstructure.
INNOVATIVE MATERIALS
HOLD PROMISE
While titanium powder materials
are not new, the advent of additive man-
ufacturing presents new and exciting
applications. AM allows components to
be designed more purely to maximize
structural integrity and performance,
with less consideration given to manu-
facturability. The result is that a higher
percent of the material is used for the
part, significantly reducing waste. While
still more expensive than steel as a raw
material, titanium powders are finding
their way into these newly simplified
parts when they would not be viable us-
ing traditional processes.
Among the newmaterial systems in
development, two show promise based
on unique properties well suited to AM.
The eTi powders are modified titani-
um alloys that offer a 30% increase in
strength and stiffness over their wrought
counterparts. Another new base alloy
gaining acceptance in AM applications
is SM-100, with a base chemistry of Ni-
40Ti. SM-100 offers excellent corrosion
and wear properties. It is difficult to
process with conventional machining
and processing, but is well suited for AM.
Among the recent uses for SM-100 are
bearing and valve components for off-
shore oil and gas production. With these
and other recent advances taking place
in the AM field, additional applications
and alloy development efforts will con-
tinue to make strides.
For more information:
Eric Bono is
vice president of sales and marketing,
Puris LLC, 78 Northpointe Dr., Bruceton
Mills, WV 26525, 412.260.8048,
ebono@ purisllc.com, www.purisllc.com.
Each printer is housed in separate clean
rooms to further ensure part cleanliness
and integrity.
Discover More Steel Research Capability www.tainstruments.com DIL 805 Quenching and Deformation Dilatometer The DIL 805-series quenching and deformation dilatometers provide the most accurate measurements over the widest range of heating, cooling,anddeformationconditions,allowingforthemostsophisticated characterization and optimization of steel processing conditions. The DIL 805 provides critical data for the construction of time-temperature- transformation (TTT) , continuous-cooling-transformation (CCT) , and time-temperature-transformation after deformation (DTTT) diagrams as well as stress-strain curves. Powerful inductive heating and an innovative helium quench system enable heating rates up to 4000 K/s and quenching rates as high as 2500 K/s to capture the extremes of modern processing conditions.