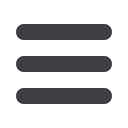
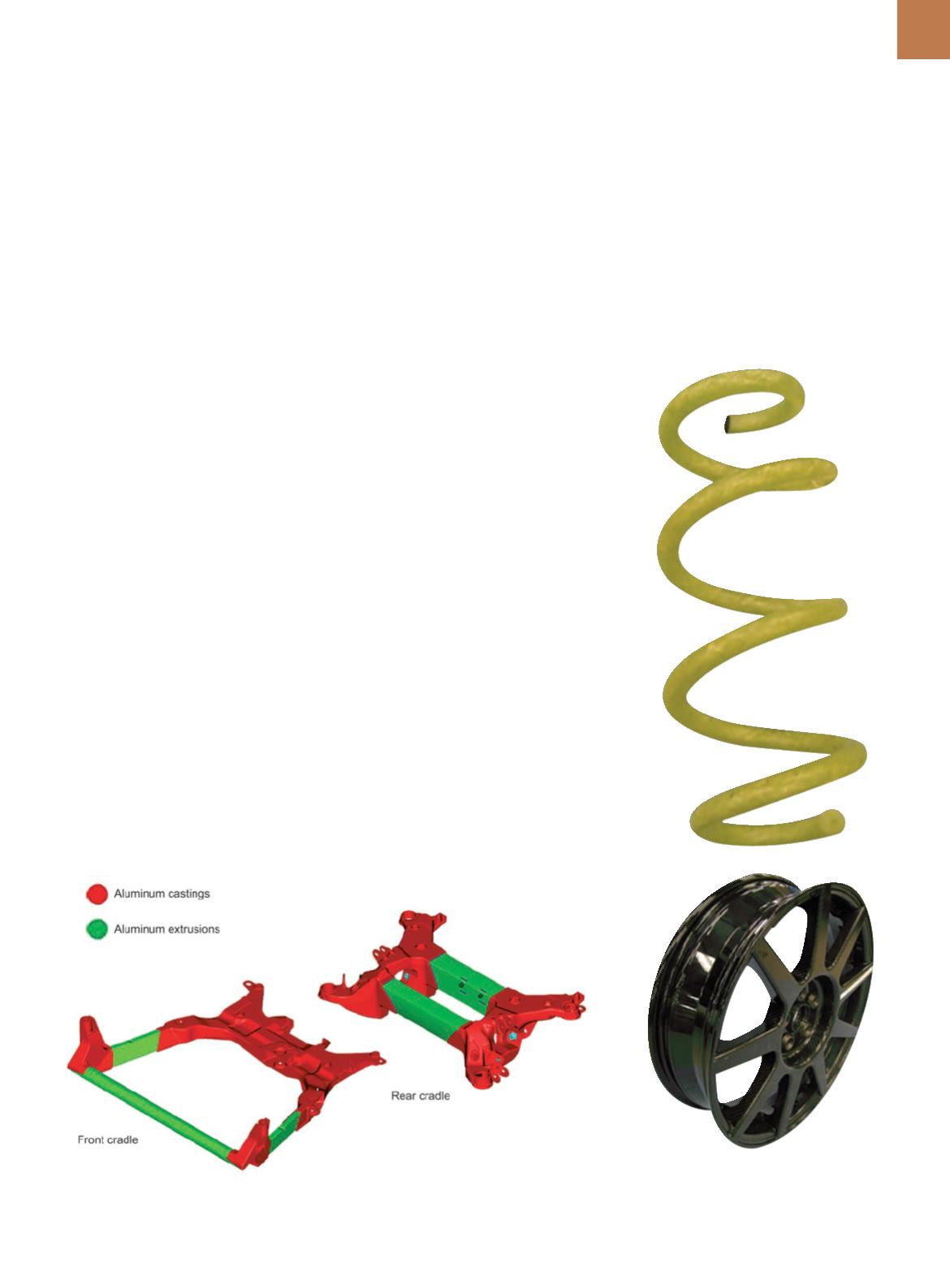
A D V A N C E D
M A T E R I A L S
&
P R O C E S S E S |
M A R C H
2 0 1 5
2 1
front seat weight by approximately 8 kg
(Fig. 3). TheMMLV design includes a 12 kg
(42%) reduction in the rear seat by use of
carbon fiber composite structures and
reduced weight foam and fabric trim.
The instrument panel beam uses
carbon fiber composites with integrat-
ed HVAC ducts and chemically foamed
nonstructural parts to reduce weight by
8 kg (36%) from the 2013 Fusion instru-
ment panel beam. Figure 4 shows the
Fusion and instrument panel designs
and materials.
CHASSIS
The MMLV design chassis system
boasts an overall 98 kg (28%) weight re-
duction from the 350 kg Fusion chassis.
The wheels and tires subsystem is 39 kg
(38%) lighter than the 103 kg Fusion.
This is achieved by eliminating the spare
wheel and tire, plus reducing the road
wheels and tire weight. The MMLV design
incorporates 5J×19 wheels and a tire de-
signandmaterial change from225/50R17
to 155/70R19. The wheel weight was set
at 7.5 kg per wheel, which is achieved
with efficient cast aluminum or carbon
fiber designs. The Fusion 7.5J×17 cast
aluminum wheels weigh 10.74 kg each.
(Note: The MMLV prototype includes car-
bon fiber 5J×19 wheels at 6.15 kg each,
Fig. 6.) The tire size change saves 3.35 kg
(29%) per tire from the Fusion—down to
8.25 kg for the MMLV tires.
The subframe designs reduce
weight by 27 kg (47%) by using cast and
extruded aluminum instead of stamped
Fig. 5 —
MMLV front and rear aluminum subframes.
Fig. 6 —
MMLV glass fiber composite spring
and carbon fiber wheel.
steel. The front subframe castings are
high-pressure die castings, while the rear
subframe side castings are low-pressure
hollow castings. The aluminum extru-
sions are MIG (metal inert gas) weld-
ed to the castings. Figure 5 shows the
MMLV subframe designs and materials.
The front and rear suspensions
for the MMLV design include hollow
steel stabilizer bars that save 1.7 kg
(39%) in the front and 2.9 kg (59%) in
the rear, reduced weight knuckles and
shocks from material substitutions of
aluminum for steel, and lightweight
coil springs. Glass fiber-epoxy compos-
ite springs are used in the front while
hollow steel springs are used in the
rear. The composite front spring weighs
1.2 kg vs 2.8 kg—a 57% savings. The hol-
low steel rear spring reduces the weight
by 1.6 kg and results in a 37% savings
(from 2.7 kg vs 4.3 kg).
An 11 kg weight savings in the
brake systems comes from materials
substitution. Traditional cast iron brake
rotors were replaced with cast alumi-
num rotors with a 1-mm-thick, thermal-
ly sprayed two-wire arc stainless steel
alloy coating to provide a durable and
wear resistant surface. Figure 7 shows
the aluminum cast front rotor and the
prototype thermal spray process.
Other weight savings in the chas-
sis system include reductions in the ca-
pacity for the steering system, replacing
the jack systemwith a flat tire repair kit,
and anticipated reductions in fasteners
due to use of lighter components.
POWERTRAIN
The MMLV design powertrain saves
73 kg (21%) over the current production
engine used in the 2013
Ford Fusion.
The Fusion control model has a 1.6-liter
four-cylinder gasoline turbocharged
direct injection (EcoBoost) engine and
6F35 six-speed automatic transmission.
The new MMLV design incorporates a
1.0-liter three-cylinder gasoline turbo-
charged direct injection (Fox EcoBoost)
engine with a lightweight design and
a lighter 6F15 six-speed automatic