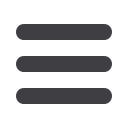
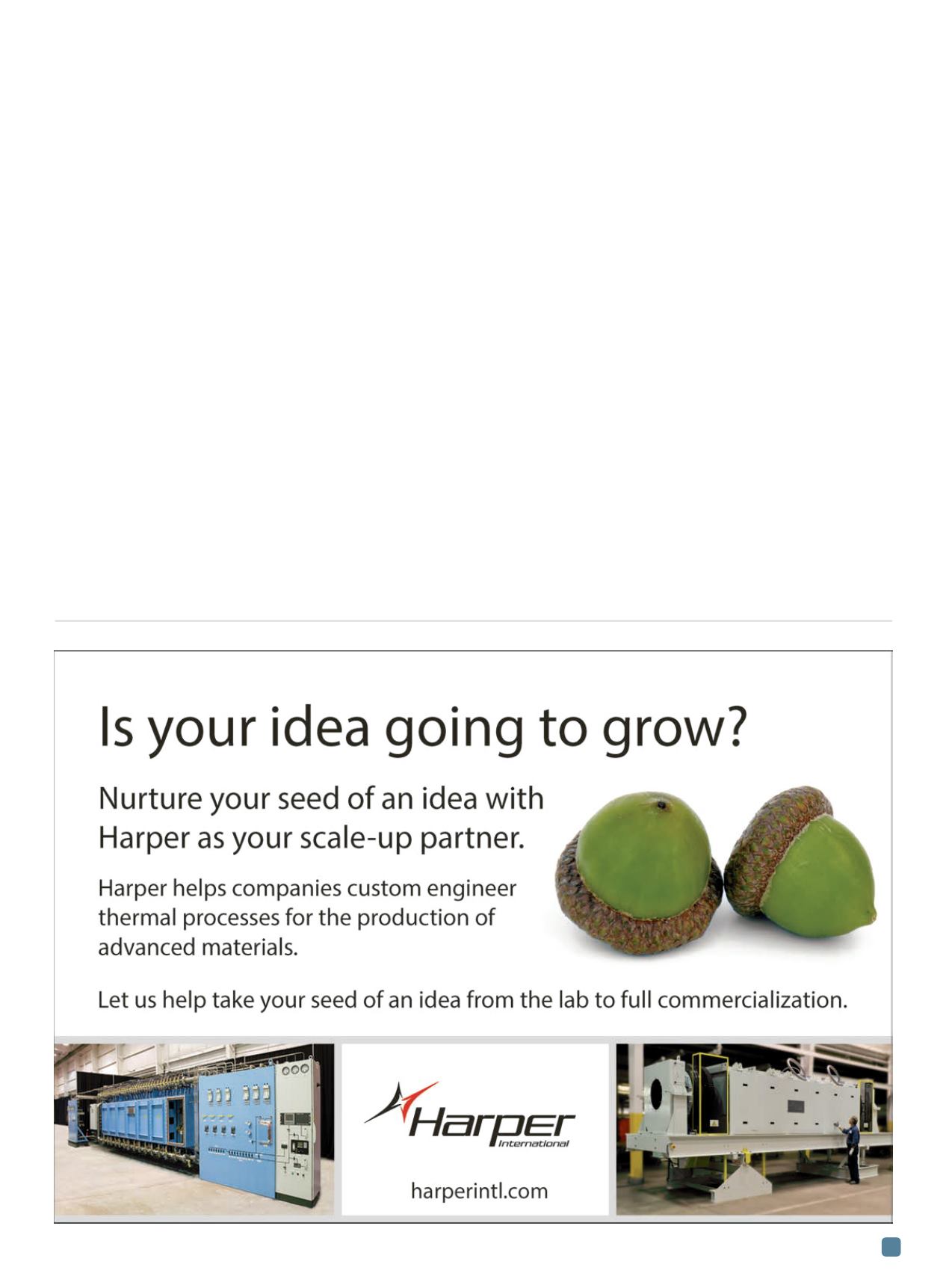
Plasma process offers
tailored surface modification
An alternative surface modification route, which
avoids wet chemistry while providing a highly tailored
material for both raw material producers and applica-
tion manufacturers, uses a plasma-based processing
route (Fig. 3).
A low temperature plasma (>100°C) patent-pending
process was developed that overcomes this key barrier.
Costs are significantly reduced due to low energy input
requirements, while modifying the surface of a target
material with a wide range of chemical groups such as
O
2
, COOH, NH
3
, and F is also possible. By tailoring the
degree of functionalization (surface modification) and
achieving optimal dispersion, it is possible to produce
graphene with specific properties and superior perform-
ance.
Non-aggressive plasma surface modification effec-
tively eliminates the risk of damage to the material being
processed and is potentially capable of actually remov-
ing impurities inherent in the raw material while also re-
pairing lattice defects. From an environmental
perspective, the process is characterized by low energy
consumption and avoids unnecessary disposal of haz-
ardous waste chemicals.
Case study: Improving
mechanical properties of composites
The mechanical performance of graphene is of par-
ticular interest as a filler for composites in industrial ap-
plications. For 50 years, carbon fiber reinforced
polymers (CFRP) have been increasingly used in high
performance applications such as passenger aircraft and
wind turbine blades, and their use is a testament to the
high performance levels that can be achieved.
Recently, Aerospace Corp., El Segundo, Calif.,
demonstrated significant steps toward the manufacture
of hierarchical or multiscale composites. It must now be
determined if these materials can be used commercially
to achieve performance benefits resulting in lighter
weight and more damage tolerant materials.
The study details the nanoreinforcement of resin
by GNPs functionalized via plasma. The epoxy
material reinforced by GNPs exhibits unprecedented
performance levels, with a 200% increase in tensile
strength and modulus over the original resin, and an
increase in toughness of more than 125%
[4]
. Due to the
promotion of dispersion and chemical bonding with
the epoxy matrix, results point to surface functional-
ization as the key parameter influencing the effective-
ness of nanoreinforcement.
ADVANCED MATERIALS & PROCESSES •
NOVEMBER-DECEMBER 2014
17