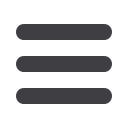
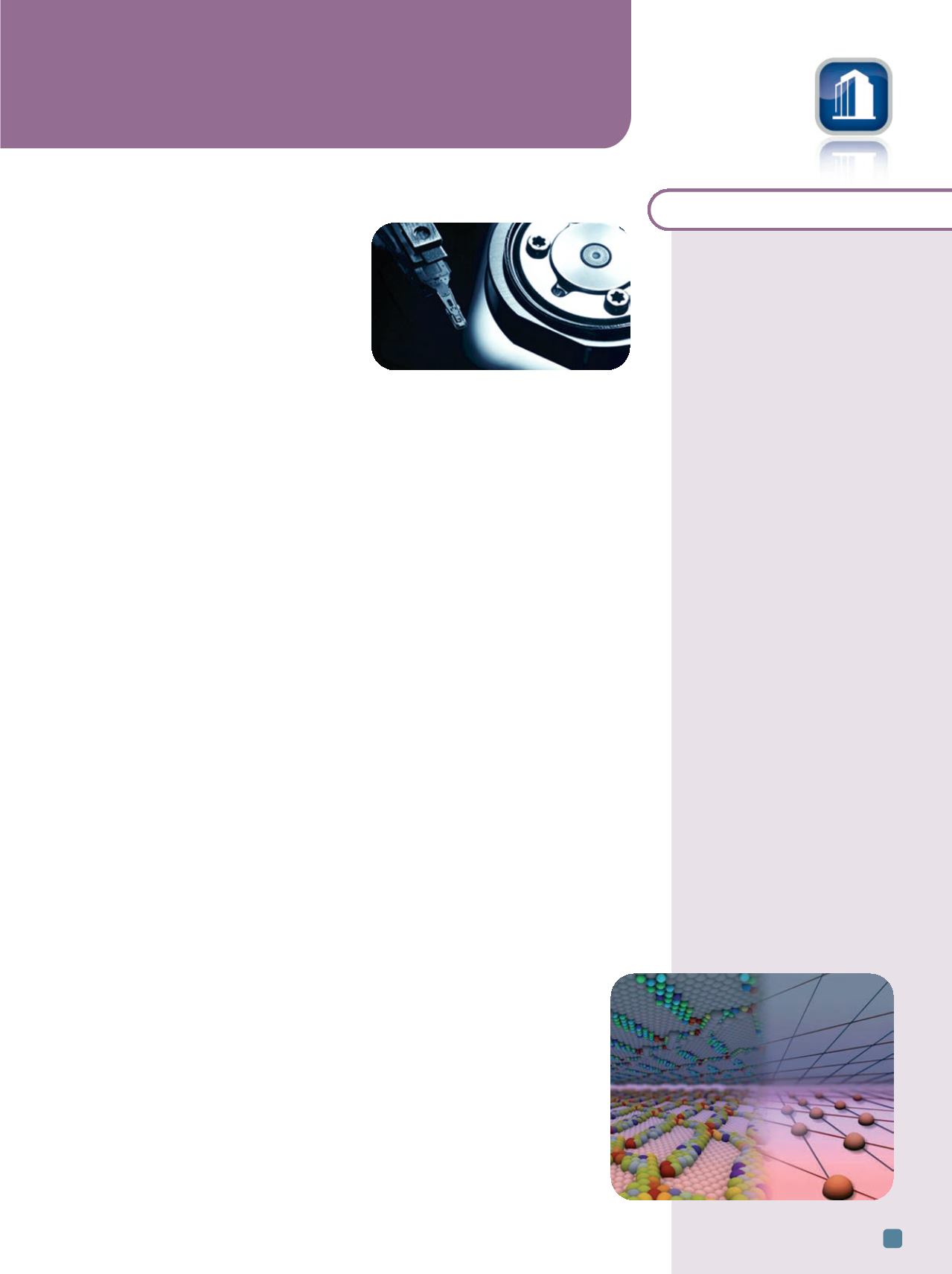
Simulations reveal how to better protect DLC coatings
By performing atom-level simulations of
nanoscale friction, Ling Dai and coworkers
from the A*STAR Institute of High Perform-
ance Computing, Singapore, uncovered critical
clues for designing better systems to lubricate
and protect diamond-like-carbon (DLC) coat-
ings. Perfluoropolyether (PFPE) is a Teflon-like
polymer commonly sandwiched betweenDLC-
coated substrates to reduce friction and protect
against damage. Understanding the friction
mechanisms between these ultrathin films is
tricky; the materials have contrasting hard and
soft mechanical properties, and the sandwich
arrangement obscures any direct observation of atomic structure and activity.
To better understand how nanoscale lubrication works in microdevices, researchers
constructed an atomic DLC–PFPE–DLC triple layer using a 3D computer modeling pro-
gram. They set one DLC slab as a substrate and the other as a “slider.” Molecular dynam-
ics techniques simulate how the lube film responds when the slider moves. Simulating
frictional motions at different speeds and PFPE film thicknesses reveals that the lubricat-
ing film behaves as a solid—the polymer retains its shape without deforming from inter-
nal shearing.
www.ihpc.a-star.edu.sg.
Carbon nanotubes turn resin coatings into conductors
Resin coatings are widely used in various industries, such as aerospace and automotive, par-
ticularly for protecting structural components. Research by the UPV/EHU-University of the
Basque Country, Spain, uses carbon nanotubes (CNTs) to improve the properties of these coat-
ings. The research was conducted within the POCO European project and seeks to develop
strategies to spread CNTs properly throughout different polymers. CNTs improve coating con-
ductivity, repair scratches, and feature excellent mechanical properties. They are also tough,
rigid, and electrically conductive. Epoxy resins, by contrast, are insulating materials. By adding
nanotubes, the resin coatings are also turned into conductors.
www.ehu.es/p200-shenhm/en.Material interfaces can be patterned to control properties
Scientists at Massachusetts Institute of Technology, Cambridge, added a new wrinkle
to research on the patterning of surfaces. While most research focuses on patterns on the
outer surfaces of materials, associate professor Michael Demkowicz and his team are ex-
ploring the effects of patterned surfaces deep within materials—specifically, at the inter-
faces between layers of crystalline materials. Demkowicz explains that much research aims
to create layered composites with desired strength, flexibility, or resistance to vibrations,
temperature changes, or radiation. But actually controlling the surfaces where two mate-
rials meet within a composite is a tricky process.
“People don’t think of them as surfaces,” says Demkowicz. “If they do, they think
of it as a uniform surface, but as it turns out, most interfaces are not uniform.” To
control the properties of these materials, it is essential to understand and direct
these nonuniform interfaces. The team took classical equations used to describe
average surface properties and adapted them to instead describe variations in these
surfaces location by location. “That’s not easy to do experimentally, but we can do
that directly in our computer simulations,” says Demkowicz.
For more information:
Michael Demkowicz, 617.324.6563,
demkowicz@mit.edu,
web.mit.edu.
Interfaces between solid materials are surfaces with an intricate, internal structure (left). To
control that structure, and use it for specific applications, researchers model it in a
simplified way (right). Courtesy of Niaz Abdolrahim and Jose-Luis Olivares/MIT.
ADVANCED MATERIALS & PROCESSES •
NOVEMBER-DECEMBER 2014
13
S
URFACE
E
NGINEERING
news
industry
briefs
Abakan Inc.,
Miami, completed
initial field testing on full-sized
production equipment of its
nanocomposite liquid metal
corrosion-resistant coating,
PComP M, with a leading steel
producer. Abakan is also working
with several other steel companies
to validate component life
extension on zinc pot rolls used
extensively in the continuous hot
dip galvanizing process, as well as
other components used to handle
and process molten metals.
PComP M demonstrates improved
molten metal corrosion resistance,
combined with increased durability
and reliability in the rapidly
changing temperature
environment encountered in
molten metal contact, compared to
conventional materials.
abakaninc.com.
Sematech,
Austin, Texas, and the
newly merged
SUNY College of
Nanoscale Science and
Engineering/SUNY Institute of
Technology,
N.Y., launched their
joint
Patterning Center of
Excellence (CoE).
The CoE will
enable lithography equipment and
lithographic materials
manufacturing companies access
to a vertically integrated
semiconductor processing facility.
The new center aims to reduce the
costs of developing critical
lithography materials for individual
semiconductor companies.
kevin.cummings@sematech.org,
public.sematech.org,
sunycnse.com.
Device longevity can be improved by using
computer models that optimize the friction
properties of diamond-like coatings used in
hard disk drives. Courtesy of Janka
Dharmasena/iStock/Thinkstock.