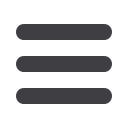
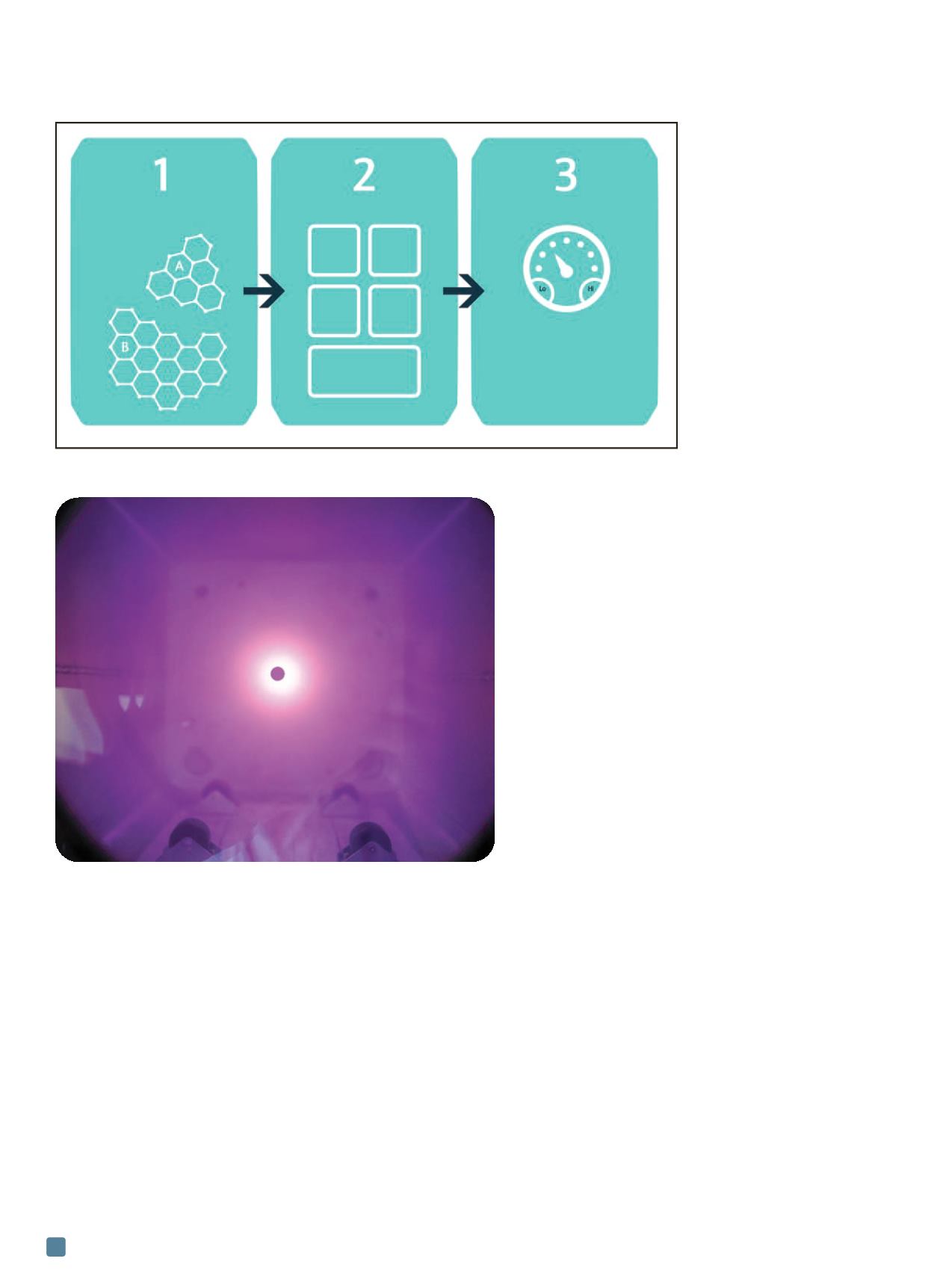
can be produced in large quantities in various thicknesses
.
Few-layer graphene
(FLG) has several atomic layers of car-
bon while
many-layer graphene
, or graphene nanoplatelets
(GNPs), typically has 5-50 layers. Another important fac-
tor is that graphene is effectively inert, meaning that the
surface chemistry can be a critical factor affecting process-
ability, and therefore its potential application.
Graphene challenges
Graphene technology has many different target mar-
kets, each requiring different material specifications, per-
formance, and cost targets, which further complicates the
path to commercialization. In addition, there are many
types of graphene, each with a different set of properties
depending on the form in
which it is produced. Average
flake size, number of graphene
layers, and the chemical
groups on the flake surfaces
can all vary.
The number of production
techniques further compli-
cates matters, with each tech-
nique delivering a different
material, cost structure, and
scalability. It is no surprise that
research departments struggle
to find a material that works
for their application yet meets
other requirements. While
there is a real need to stan-
dardize the growing number of
graphene variants—recogniz-
ing the cost benefits of each
family and establishing applications for which they are
most suitable—a one-size-fits-all approach will not work
for many potential applications (Fig. 2).
Chemical vs. plasma surface modification
Graphene supply is unlikely to be a problem, at least in
the case of GNPs due to the range of production methods
already discussed. However, surface chemistry was only re-
cently identified as a key factor in realizing the full poten-
tial of nanomaterials. Incorporating nanomaterials into
polymeric and liquid phase applications requires a homog-
enous dispersion within the secondary phase. This is not
an easy task as the natural tendency of nanomaterials to
agglomerate or separate out means that good dispersions
can only be attained by engineering the material’s surface
via a modification process.
Chemical treatments can effectively modify the surface
of graphene, but significant environmental and ecological
costs associated with their use can outweigh the benefits.
Although these processes are scalable, they use aggressive
chemicals and tend to create defects in the material struc-
ture and introduce impurities. Further, the surface chemi-
cal functional groups are limited to those inherent in the
available acids.
An alternative functionalization route via plasma
avoids environmental issues and can aid dispersion and
chemical bonding with a matrix. With the correct chem-
ical functionalization such as incorporating a compatible
chemical side group, there is a much greater possibility
of achieving homogeneous dispersion during processing
and chemical bonding (such as covalent bonding) with
the matrix.
Researchers discovered that graphene and graphene
oxide show promise as reinforcements in high-performance
nanocomposites and should have outstanding mechanical
properties
[3]
. In order to obtain the optimummechanical and
conductive properties, a strong interface between the rein-
forcement and the polymer matrix is required
[3]
.
ADVANCED MATERIALS & PROCESSES •
NOVEMBER-DECEMBER 2014
16
Fig. 2 —
Graphene is a complex picture and a one-size-fits-all approach is not suitable for the majority of
potential applications.
Material
Chemistry
Level
Degree of
functionalization
O
2
COOH
NH
3
F
Other
Fig. 3 —
By tailoring the degree of functionalization and achieving optimal
dispersion, the low temperature plasma process (>100°C) produces
graphene with specific properties and superior performance for
customization. Plasma is generated via the central electrode inside the
rotating drum.