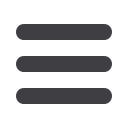
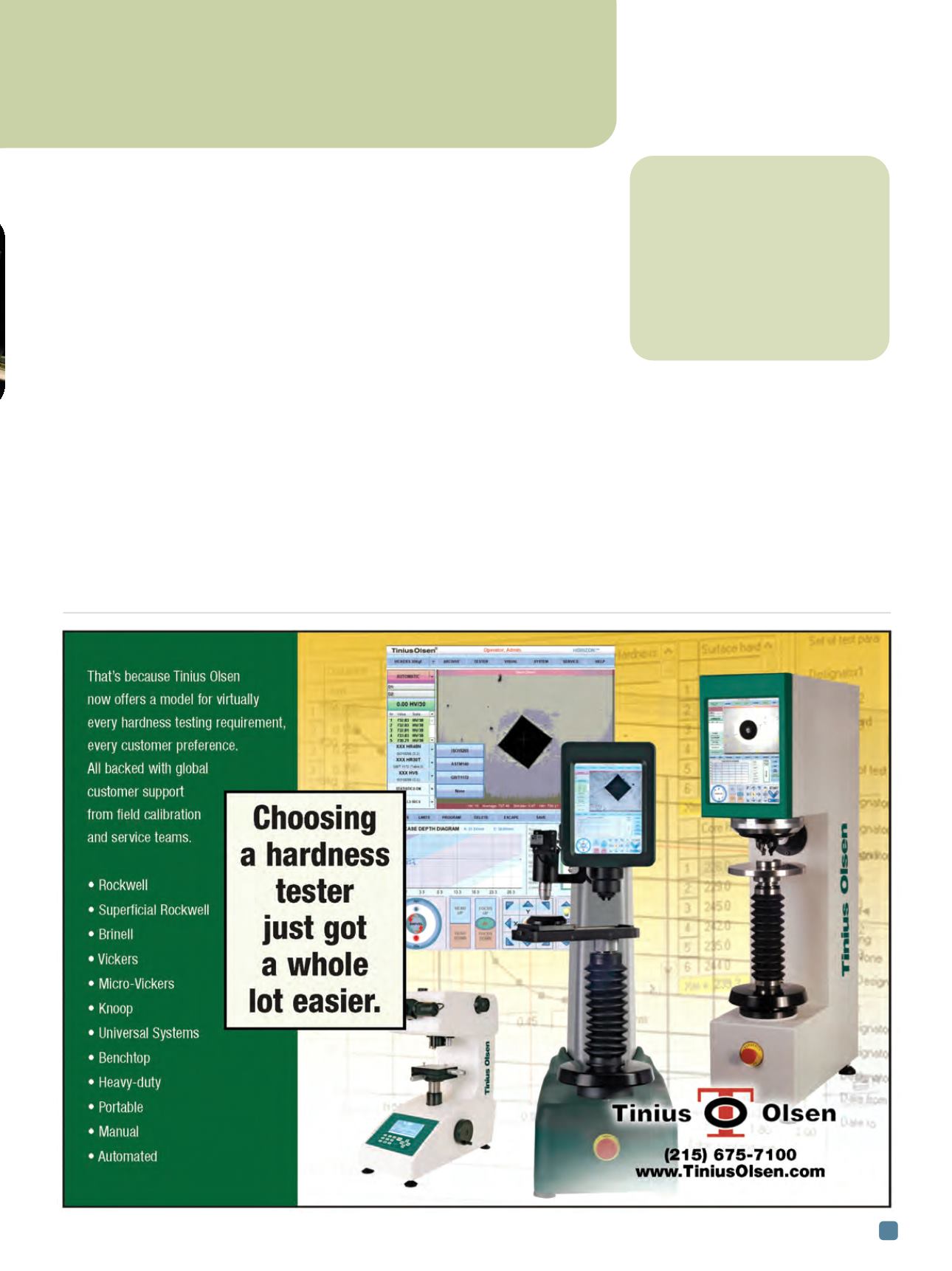
ADVANCED MATERIALS & PROCESSES •
NOVEMBER-DECEMBER 2014
9
tions, where nanotubes are always subjected to external perturbations that potentially
may lead to the creation of these traps,” he explains.
Research is conducted with an ultrahigh vacuum scanning tunneling microscope cou-
pled to a closed-cycle cryostat, built for use in Nazin’s lab. The cryostat allows the team
to lower the temperature to 20 K to freeze all nanoscale motion and visualize the inter-
nal structures of nanoscale objects. The device captures the internal structure of elec-
tronic waves trapped in short sections, just several nm long, of nanotubes partially
suspended above an atomically flat gold surface.
uoregon.edu.
Research grants focus on aerospace metal fatigue
University of Texas at Arlington engineering professors received a $451,781 Air Force Office of Scientific Research
grant to examine the material surface at the micro and nano-scale level that will provide clues for predicting fatigue in
aircraft parts. Haiying Huang, professor of Mechanical and Aerospace Engineering, says the new technology and process
will be better and more efficient than taking x-rays of an aircraft’s wing.
“We’ll be able to determine metal fatigue at very early stages when we look at it on this scale,” explains Huang. “Cer-
tain patterns of surface roughness changes will tell us how the material will behave when put under the fatigue of flying.”
In addition, the team received a $348,385 grant from the Defense University Research Instrumentation Program
(DURIP) of the Air Force Office of Scientific Research to purchase two pieces of equipment that will help gauge the wear
on these aircraft parts. The grant allows Huang to purchase a scanning whitelight interferometric surface profiler inte-
grated with a compact mechanical tester and an electron backscatter diffraction module. The surface profiler provides
researchers with in-situ 3D surface profiling of fatigued specimens. The diffraction module will be retrofitted with a
scanning electron microscope to allow researchers to measure dislocation patterns in the fatigued material.
uta.edu.
Phoenix Nuclear Labs
(PNL), Monona, Wis.,
received a one-year, $3 million contract by
the
U.S. Army
to build an advanced neutron
radiography unit. The imaging system will be
used for nondestructive inspection of muni-
tions, pyrotechnics, and other critical de-
fense components. The new system is
expected to generate 10 times the amount
of neutrons, enabling faster performance,
and will produce digital images that will im-
prove the unit’s ability to analyze and store
data.
phoenixnuclearlabs.com.