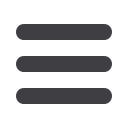
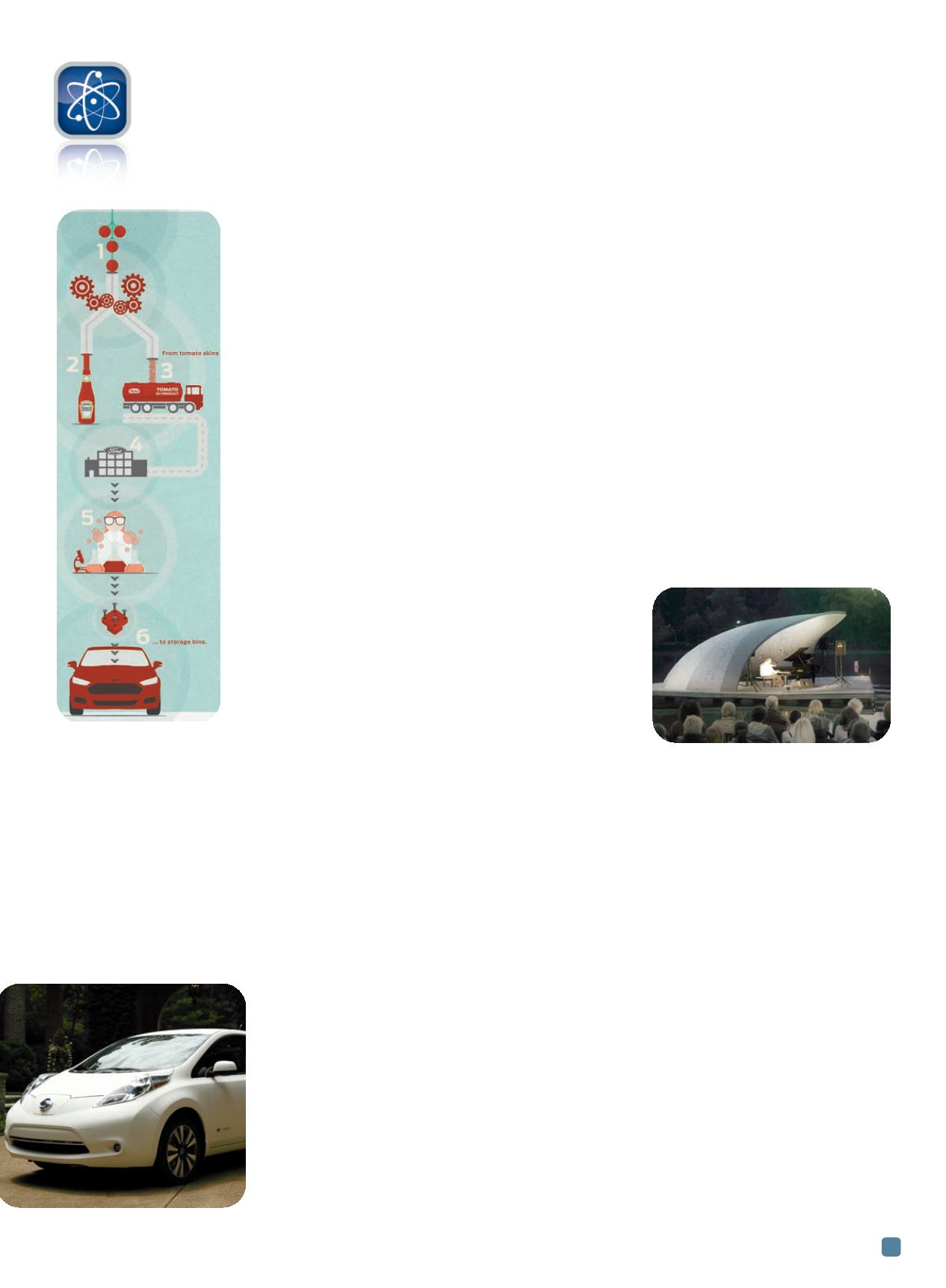
Tom-auto: Car-ketchup collaboration
enables plant-based plastic
Researchers at Ford Motor Co., Dearborn, Mich., and H.J. Heinz Co., Pittsburgh, are inves-
tigating the use of tomato fibers in developing sustainable composite materials for use in ve-
hicle manufacturing. Specifically, dried tomato skins could become vehicle wiring brackets or
the storage bin a driver uses to hold coins and other small objects.
Nearly two years ago, Ford began collaborating with Heinz, The Coca-Cola Co., Nike Inc., and
Procter & Gamble to accelerate development of a 100% plant-based plastic to be used to make
everything from fabric to packaging and with a lower environmental impact than petroleum-
based packaging materials. At Heinz, researchers were looking for ways to repurpose peels, stems,
and seeds from the more than two million tons of tomatoes the company uses annually to pro-
duce its best-selling product: Heinz Ketchup. Company leaders contacted Ford.
“We are delighted that the technology has been validated,” says Vidhu Nagpal, associate di-
rector, packaging R&D for Heinz. “Although we are in the early stages of research and many
questions remain, we are excited about the possibilities for both Heinz and Ford, and the ad-
vancement of sustainable 100% plant-based plastics.”
ford.com,
heinz.com.
Inflatable concrete holds promise for large structures
Large shell structures made of concrete or stone are rarely
built today because construction requires large and expen-
sive supporting assemblies. A new technique for creating
concrete shells developed at the Vienna University of Tech-
nology, Austria, uses inflatable air cushions instead. A flat
concrete slab hardens on the ground while an air cushion
below the plate is inflated, bending the concrete and quickly
forming a sustainable shell.
“It is similar to an orange peel, which is regularly cut and
then flattened out on the table,” says professor Johann Kolleg-
ger. “We do it the other way around, starting with a flat surface
and then bending it to a shell.” Kollegger and Benjamin Kromoser, also of TU Vienna, developed the new tech-
nique, which was successfully tested on the Aspang Grounds in Vienna.
A flat slab is first created using standard concrete and it is crucial to get the geometric shape exactly right. The
slab consists of several segments. Wedge-shaped spaces are left between these segments, so they fit together per-
fectly when the structure is bent. Once the slab is hardened, an air cushion below is inflated. The cushion consists
of two plastic sheets welded together. At the same time, a steel cable is tightened around the concrete segments,
so that the concrete is lifted up at the center and pushed together from outside. To ensure that all the concrete seg-
ments move in perfect synchronicity, they are connected with metal beams. In the experiment, the entire process
was finished after about two hours and the final height was 2.9 m.
www.tuwien.ac.at.
Self-cleaning nanopaint promises pristine vehicles
The Nissan LEAF electric vehicle might just be the most pristine car on the planet. It
uses a new self-cleaning paint called Ultra-Ever Dry that repels mud, rain, and dirt. The
nanopaint creates a protective layer of air between the paint and environment, effectively
stopping standing water and road spray from creating dirty marks on the car’s surface. Nis-
san is one of the first automakers to apply this technology to a vehicle. The coating, which
is being marketed and sold by UltraTech International Inc., is undergoing testing by engi-
neers at Nissan Technical Center Europe. So far, it has responded well to common condi-
tions including rain, spray, frost, sleet, and standing water.
nissanusa.com.
Created to demonstrate potential use in future production vehicles, this Nissan LEAF’s exterior
was treated with a specially engineered superhydrophobic and oleophobic paint designed to repel
water and oils. Courtesy of Business Wire.
ADVANCED MATERIALS & PROCESSES •
NOVEMBER-DECEMBER 2014
5
interest
of material
A concert pavilion is one potential
application for a new concrete dome
construction method.
Tomato fibers could be
used to develop plant-
based composite materials
for use in automobiles.