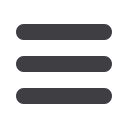
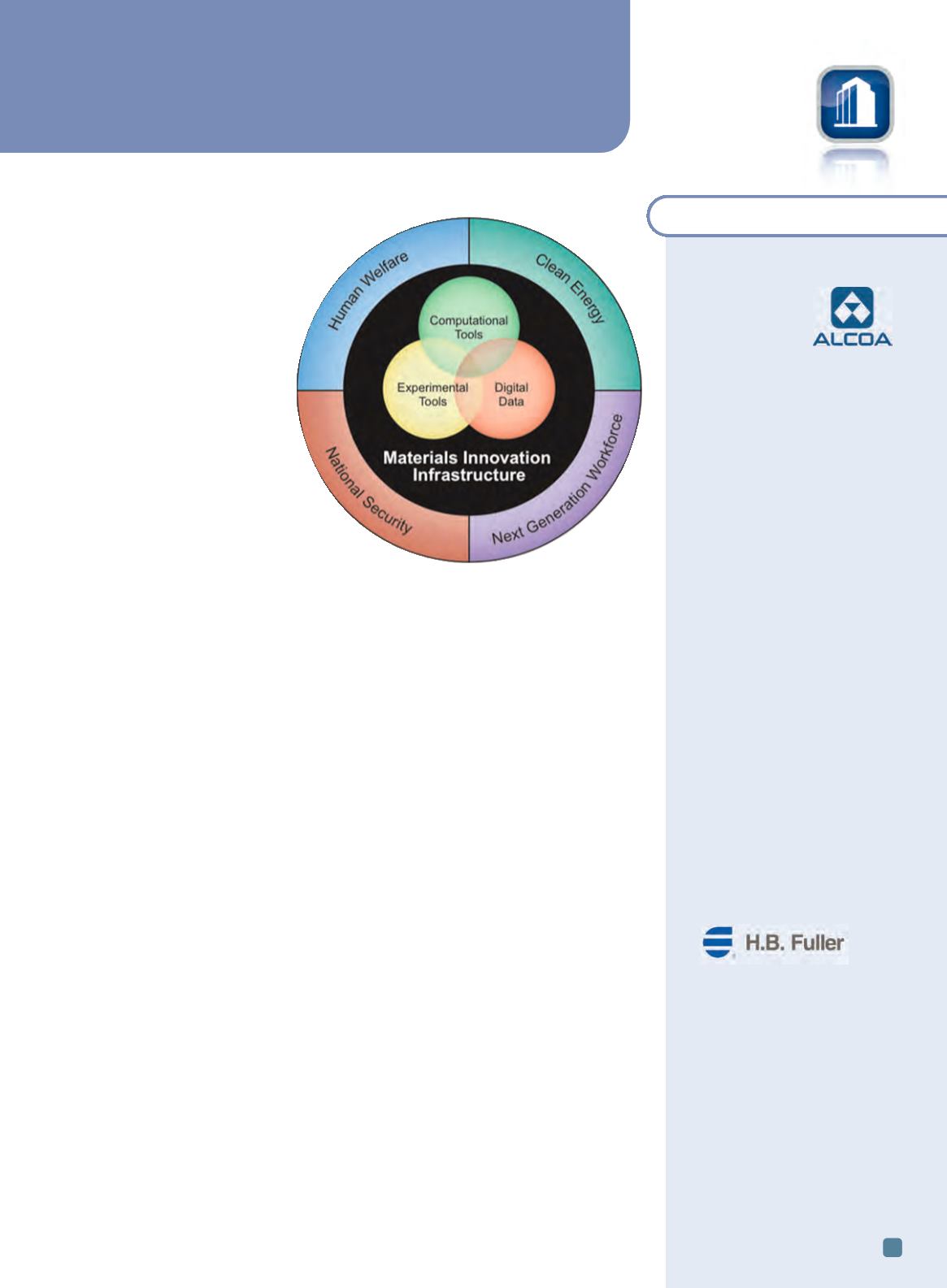
ADVANCED MATERIALS & PROCESSES •
OCTOBER 2014
13
news
industry
briefs
Alcoa Inc.,
Pittsburgh, will spend
roughly $3 billion to acquire
Firth
Rixson,
UK, a jet
engine component
company, in a deal
expected to close
later this year. Firth Rixson makes
rings, forgings, and other metal
products for aerospace and other
industries. The high cost of
producing aluminum and falling
prices have pushed Alcoa toward
more finished products that are
used in aircraft, autos, and other
goods. Aluminum prices have not
recovered since the recession, so
Alcoa has been idling smelters to
reduce capacity and cut costs. The
company also plans to spend $100
million to build a factory in Indiana
to make nickel-based engine parts
for commercial airliners.
alcoa.com.
H.B. Fuller Co.,
St. Paul, Minn.,
signed an agreement to purchase
Tonsan Adhesive Inc.,
the largest
independent engineering
adhesives provider in China.
Tonsan produces silicone, epoxy,
anaerobic, and cyanoacrylate
technologies. It develops,
manufactures, and sells these
engineering adhesives to key
durable assembly markets, such
as transportation, machinery,
photovoltaic, electronics, and
electrical appliances. H.B. Fuller’s
global infrastructure will enable
the delivery of Tonsan’s products
around the world.
hbfuller.com.
Automotive components
manufacturer
Hatch Stamping
Co.,
Chelsea, Mich., is planning a
$17 million manufacturing facility
in Portland, Tenn. The company
will design and manufacture highly
engineered metal stampings and
assemblies in the 106,000-sq-ft
manufacturing facility, producing
auto parts for both the Southeast
market and worldwide distribution.
hatchstamping.com.
P
ROCESS
T
ECHNOLOGY
Strategic approach to MGI advances materials research
Through the Materials Genome Initiative for
Global Competitiveness (MGI), launched in
2011 under the U.S. Advanced Manufactur-
ing Partnership, the federal government
aims to double the pace of advanced
materials discovery, innovation, man-
ufacture, and commercialization. As
the initiative marks its third year, ex-
perts at three leading universities
are partnering on a unique effort to
create synergy among materials re-
searchers. The MGI Accelerator Net-
work unites a team of leading MGI
researchers at the Georgia Institute of
Technology, the University of Michigan,
and the University of Wisconsin-Madison.
One of the goals is to identify strategic
ways in which researchers across the country
might share resources, knowledge, and expertise to
develop new materials quickly and efficiently. To improve un-
derstanding of MGI challenges and to help focus MGI-related research—which centers
around building an innovation infrastructure of integrated experiments, computation, and
digital data—members of the Accelerator Network are engaging thought leaders and stake-
holders from academia, industry, and governmental agencies in the U.S. On June 5 and 6,
the team hosted a workshop at Georgia Tech that drew more than 150 of these represen-
tatives, as well as speakers who are leading MGI efforts within U.S. industry, academia,
and government. One of the workshop outcomes is a series of priorities that includes de-
veloping an inventory of MGI-related research and infrastructure.
“We want to get the most value out of what research is being planned and conducted,”
says John Allison, professor of materials science and engineering at the University of Michi-
gan. “A comprehensive picture of these efforts, as well as the physical and cyber infrastruc-
ture that exists around the country, will allow materials researchers to form collaborations,
identify fundamental engineering problems, share best practices and novel approaches,
and support interdisciplinary communication among industry, academia, and government
laboratories, and across geographical boundaries.”
For more information: John Allison,
734.615.5150,
johnea@umich.edu,
umich.edu.
3D printing project focuses on aerospace repairs
Optomec, Albuquerque, N.M., was awarded a major project from America Makes, the
National Additive Manufacturing Innovation Institute, Youngstown, Ohio. The “Re-Born
in the USA” project focuses on using additive manufacturing technology to repair aero-
space metal components for the U.S. Air Force. The team led by Optomec will leverage the
unique advantages of laser engineered net shaping (LENS) 3D metal printing technology,
plus the expertise of some of the world’s leading aerospace companies and industry organ-
izations, to advance a reliable, cost-effective approach to replace conventional repair
processes such as manual welding.
Optomec will lead a team of 23 partners, including GE Aviation, Lockheed Martin,
United Technologies Research Center, and Rolls-Royce, as well as a group of technical ex-
perts serving as lead contributors, including EWI, Connecticut Center for Advanced Tech-
nology, TechSolve, the Pennsylvania State University Applied Research Lab, and
Concurrent Technologies Corp. Unlike powder bed AM approaches, Optomec’s LENS
process can add metal onto an existing substrate of almost any 3D shape, making it well
suited for repair operations.
americamakes.us,
optomec.com.