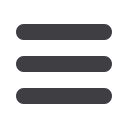
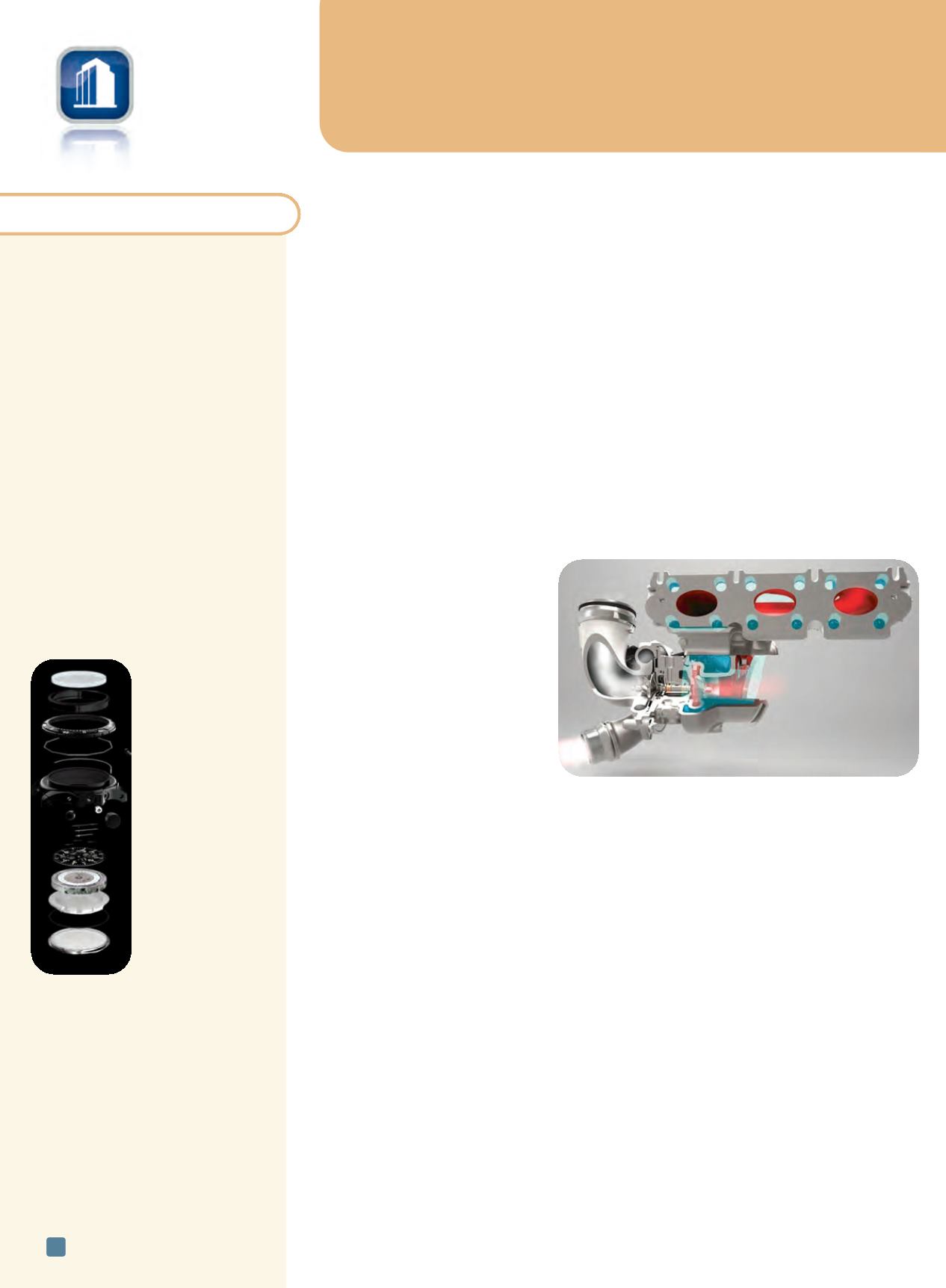
Overcoming magnesium barriers in aircraft interiors
For decades, magnesium has been banned from use on aircraft interiors due to the per-
ceived threat of intense fire producing high heat and bright light. Although Mg alloys could
reduce seat weight by 30%, this ban has hindered progress in designing lighter-weight struc-
tures. Bruce Gwynne, VP Divisional Strategic Development at Magnesium Elektron, UK,
began pursuing magnesium use inside aircraft in 2006. He worked with TimMarker of the
FAA’s William J. Hughes Technical Centre to undertake the many iterations of testing re-
quired to approve these new magnesium alloys. Initial tests compared the performance of
full-scale seat models made of traditional magnesium to those made of the new alloys.
After the new materials (including Elektron43) passed burn tests, the alloy structures were
substantiated—including critical extra time before incapacitation on the survivability
model—and the material was ready for the next phase.
The FAA has now released a report required to allow the new magnesium in the cabin
under special condition approvals. A change to TSO C127a, which references SAE AS-
8049 (the standard banning magnesium), will take more time, although the TSO modifi-
cation is not required to move forward.
For more information: Steve Montisci
+440.161.911.1220,
magnesium-elektron.com.
Aluminum turbochargers reduce vehicle weight
A modern turbocharged sys-
tem is necessary to lower fuel con-
sumption without sacrificing
performance. Continental Auto-
motive Systems, Germany, is pio-
neering innovative turbocharger
technology. Developers have
launched series production of the
first car turbocharger with an alu-
minum turbine housing. The new
turbocharger is making its debut
in a demanding downsized appli-
cation—a turbocharged three-
cylinder engine with 1.5 l of cubic
capacity and 100 kW of power.
“The double-walled aluminum housing surrounds the hottest area with a cooling water
jacket,” says Wolfgang Breuer, head of the engine systems business unit. The coolant flow-
ing through this jacket ensures that the external housing surface does not get hotter than
248°F and that the internal temperature does not exceed 662°F. At the same time, the dy-
namic response of the electric actuator at the wastegate ensures that the catalytic converter
heats up quickly,” adds Breuer.
continental-corporation.com.
Studying nanoparticles that resemble stainless steel
Mathew M. Maye, associate professor of chemistry at Syracuse University, N.Y., was
awarded a three-year, $360,000 grant from the National Science Foundation (NSF),
Arlington, Va., supporting his ongoing work with metal stainless alloy nanostructures. The
results of his work may impact gas storage, heterogeneous catalysis, and rechargeable
lithium-ion batteries. Maye’s approach is novel, in that he is attempting to chemically syn-
thesize nanoparticle alloys that resemble steel and stainless steel.
“We’re all aware of the basic properties of stainless steel,” says Maye, citing shiny, rust-
resistant kitchen metal surfaces as an example. “At the nanoscale, this rusting, or oxidation,
is difficult to stop. By synthesizing stainless interfaces, we hope to better protect nanopar-
ticles from oxidation.”
Nanoparticles that contain iron cores and thin shells are used, the latter of which are
made up of chromium, nickel, aluminum, or titanium. Maye developed the chemistry to
news
industry
briefs
A
QuesTek Innovations LLC
Materials by Design,
Evanston,
Ill., team accelerated the material
development of M54 steel from a
clean sheet design to a fully
qualified, commercially available
alloy in just six years, under a U.S.
Navy Naval Air Systems Command
(NAVAIR) Small Business
Innovation Research funded
project. Late last year, the Navy
tested and qualified hook shank
arresting gear components made
from Ferrium M54 steel for the T-
45 aircraft, in part because it
provided more than twice the
component life over the incumbent
Hy-Tuf steel. Ferrium M54 benefits
include superior strength and
toughness, and resistance to
fatigue and stress corrosion
cracking.
questek.com.
Armourglass, created by the
ArmourLite Watch Co.,
North
Miami Beach, Fla.,
is a revolutionary
shatterproof
crystal that far
surpasses the
durability of
traditional
crystals, according
to company
sources. Most
watch crystals
have a glass
strength of 700
Vickers while
Armourglass has
been tested to a
hardness of 6000
Vickers. To match
the Armourglass
strength, the
company developed special 316L
stainless steel housings and mated
the two with a custom rubber
retaining ring that ensures superior
shock resistance and watertight
construction.
armourlite.com.
M
ETALS
P
OLYMERS
C
ERAMICS
ADVANCED MATERIALS & PROCESSES •
OCTOBER 2014
8
The new turbocharger with aluminum housing by
Continental is lighter and more economical than previous
models. Courtesy of PRNewsFoto/Continental.