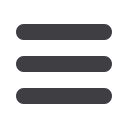
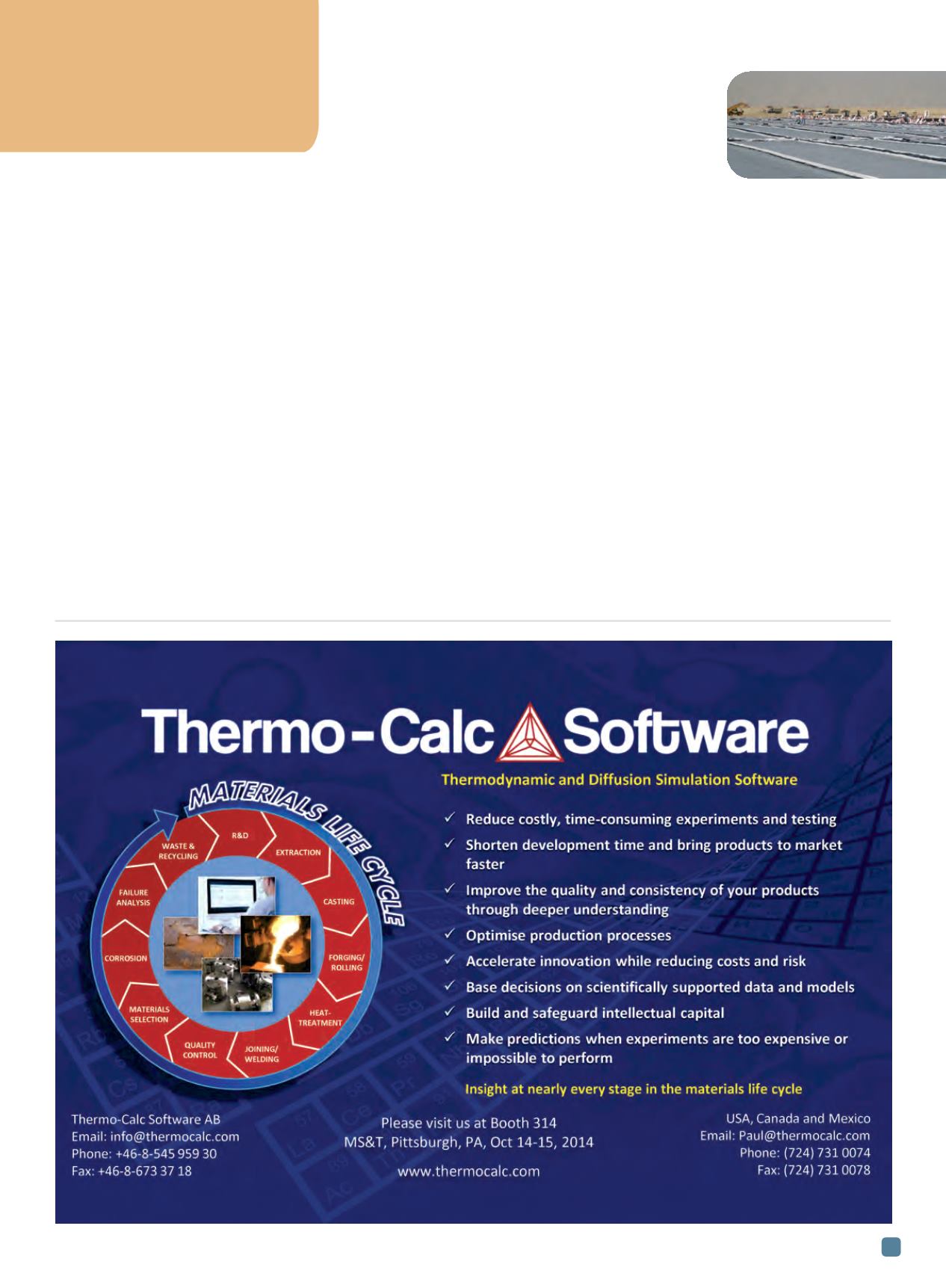
ADVANCED MATERIALS & PROCESSES •
OCTOBER 2014
9
produce these materials, which are then
exposed to heat and oxygen, allowing for
control of alloying and oxidation.
“Preliminary studies show that a
nanometer-thin layer of oxide can be
used to protect the nanoparticle, while
providing a new mechanism to control
nanoparticle structure and reactivity,” he
says. “As a result, we can make atomic to
nanoscale voids, which are holes in the
particle about the size of a molecule.
These voids can be used to trap and store
gas, such as carbon dioxide, and to serve
as electrodes in lithium-ion batteries.”
The goal of the NSF project is three-
fold: To develop “wet-chemical” synthe-
sis strategies to prepare the alloy
nanomaterials; to understand their oxida-
tion and phase behavior; and to use such
behavior to construct novel structures.
For more information: Mathew M. Maye,
315.443.2146,
mmmaye@syr.edu,
syr.edu.
Creating safer materials
to store industrial waste
University of Wisconsin-Madison researchers part-
nered with companies through the National Science
Foundation’s Grant Opportunities for Academic Liaison
with Industry program to reinforce materials that house
industrial waste by fusing them with polymers. Their
starting point is sodium bentonite clay, which has proven
reliable in a variety of environmental applications, essen-
tially swelling and forming a seal when exposed to water
or other liquids. But the clay sometimes fails to swell ad-
equately when subjected to harsh conditions, such as the
extreme pH levels of “red mud,” the alkaline residue pro-
duced by aluminum extraction.
“You have to be able to store the waste into perpetuity—hun-
dreds of acres of this liquid,” says Craig H. Benson, professor of civil
and environmental engineering. “Effective containment is part of
the social contract these companies have with their community.”
Benson and his colleagues spent the past five years experi-
menting with different ways to incorporate polymers into the
bentonite clay. They eventually discovered that the best method
was to let polymer molecules move around on the bentonite’s sur-
face, essentially finding a way into the flow path of the liquid as
the clay swells up. The resulting material can withstand pH lev-
els as low as 1 (highly acidic) and as high as 14 (highly basic)
depending on the concentration of the substances involved.
For more information: Craig H. Benson, 608.262.7242,
chbenson@wisc.edu,
wisc.edu.
A new material, being
installed at a site in the
Middle East, combines
sodium bentonite clay and
polymers to create a
substance that can with-
stand industrial waste.
Courtesy of CETCO.