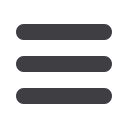
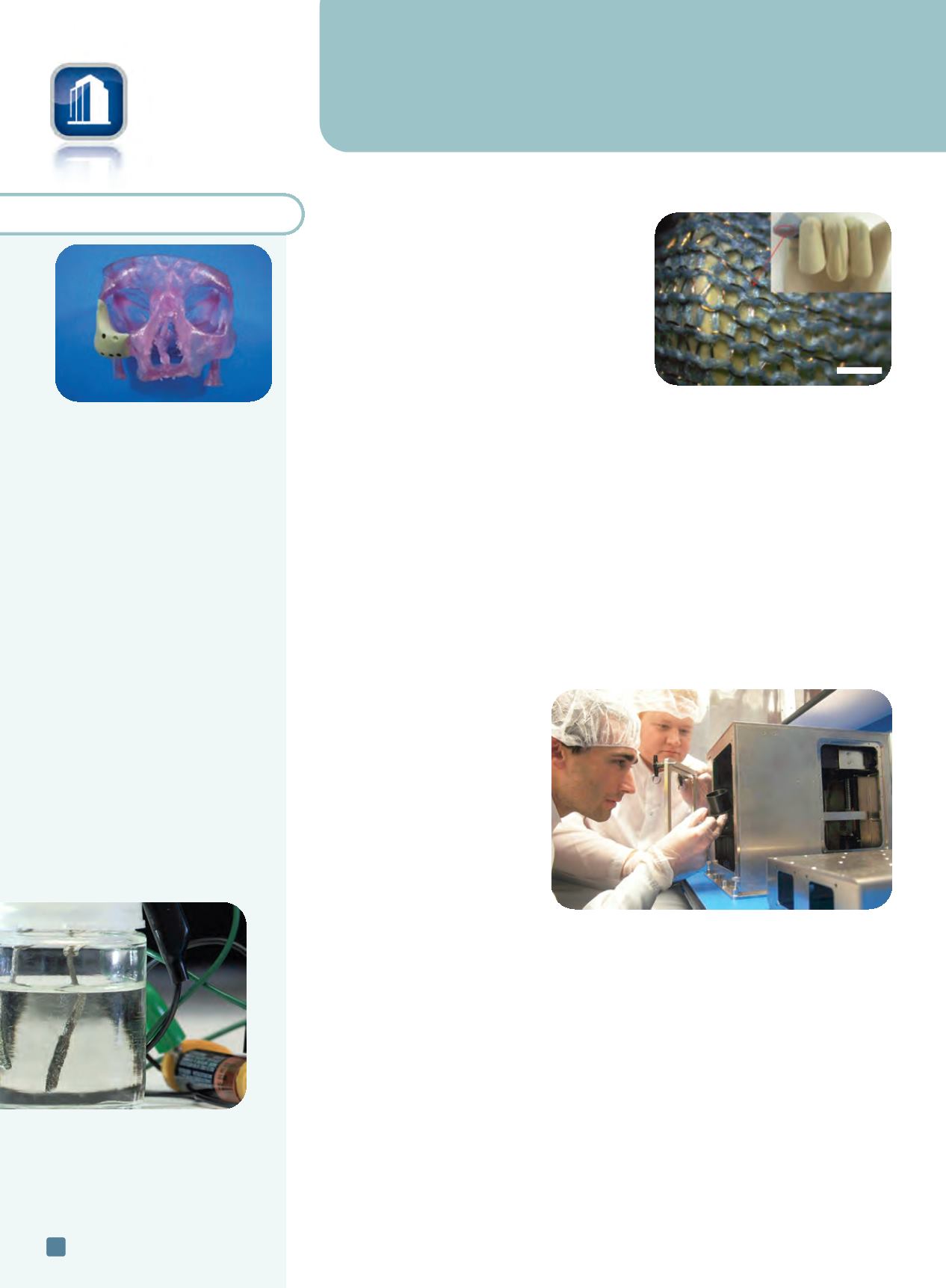
news
industry
briefs
Oxford Performance Materials,
South Windsor, Conn., received the
first FDA clearance for a 3D
printed polymeric implant for facial
reconstruction. The OsteoFab
Patient-Specific Facial Device is
manufactured for individual patient
anatomies using MRI or CT scans
as templates. Implants are
biocompatible, radiolucent, and
similar to bone, including the
ability to support bone
attachments.
oxfordpm.com.
Scientists at
Stanford University,
Calif., developed a low cost,
emissions-free device that uses an
ordinary AAA battery to produce
hydrogen by water electrolysis.
The hydrogen gas could be used to
power fuel cells in zero-emissions
vehicles, say researchers. The
battery sends an electric current
through two electrodes that split
water into hydrogen and oxygen.
Unlike other water splitters that
use precious-metal catalysts,
electrodes in the Stanford device
are made of abundant nickel and
iron.
stanford.edu.
In the Stanford device, gas
bubbles are produced by
electrodes made of nickel and
iron. Courtesy of Mark Shwartz.
Fabric circuit boards ready for wash and wear
Researchers at The Hong Kong Polytechnic
University developed a computerized knitting
technology that enables manufacturing of fabric
circuit boards (FCBs), materials that can with-
stand harsh environments and keep performing.
Making circuit boards that can handle more pun-
ishment than those currently available would
allow for entirely new products such as shatter-
proof phones, wearable devices embedded in
clothing, and tougher police and military gear.
The team combined electrically conductive fi-
brous metal materials with traditional fabric ma-
terials using the computer-based knitting technology. The result is a 3D material that can
withstand stretching, being laundered in a washer and dryer, assault by a bullet (when
under a bulletproof vest), and twisting over many cycles and for long time periods.
FCBs work by directing electricity from one part of the garment to another, offering
mechanical support as they electrically connect discrete electronic components. They can
also be designed as single, double, or multi-layered structures, mimicking traditional fab-
rics. To be used as wearable devices, they must offer low resistance to allow for reasonable
comfort and be washable to allow for stain and odor removal. The Hong Kong team says
their FCBs are ready for use in clothing items such as shirts and vests, which could be used
as solar collectors or as multiple sensory devices to record the wearer’s temperature, per-
spiration, and heart rate, for example.
www.polyu.edu.hk.
3D printing enters the cosmos
A custom 3D printer that en-
ables fabrication of all the neces-
sary tools and components
required for a space mission will
be sent to the International
Space Station (ISS) aboard the
SpaceX-4 resupply mission
slated for late September. The
printer was developed by Made
In Space, Mountain View, Calif.,
which received a Small Business
Innovation Research award
as part of the 3D Printing In
Zero-G Technology Demonstra-
tion program at NASA’s Mar-
shall Space Flight Center to develop the first 3D printer capable of working in microgravity.
The new printer successfully completed all flight certification and acceptance testing in
April 2014 at Marshall.
NASA engineers are hoping to demonstrate that a 3D printer can function as expected
in space and print components with similar quality to those fabricated on earth. If suc-
cessful, the achievement will be the first step toward establishing a working machine shop
in space. The goal is to pave the way toward lower cost, lower risk, and more efficient mis-
sions on the ISS by creating tools and replacement parts on demand. Onboard manufac-
turing capabilities would be highly beneficial to long-term missions. The program is
supported by the International Space Station Technology Development Office in Hous-
ton, as well as the Game Changing Development Program and the Advanced Human Ex-
ploration and Operations Mission Directorate at NASA headquarters in Washington.
madeinspace.us,
nasa.gov.ADVANCED MATERIALS & PROCESSES •
OCTOBER 2014
12
E
MERGING
T
ECHNOLOGY
Structure of a knitted fabric circuit
board. Courtesy of
Proceedings of the
Royal Society.
200 mm
Mike Snyder and Jason Dunn of Made In Space assemble
the 3D printer that will fly to the International Space
Station. Courtesy of Made in Space.