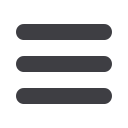
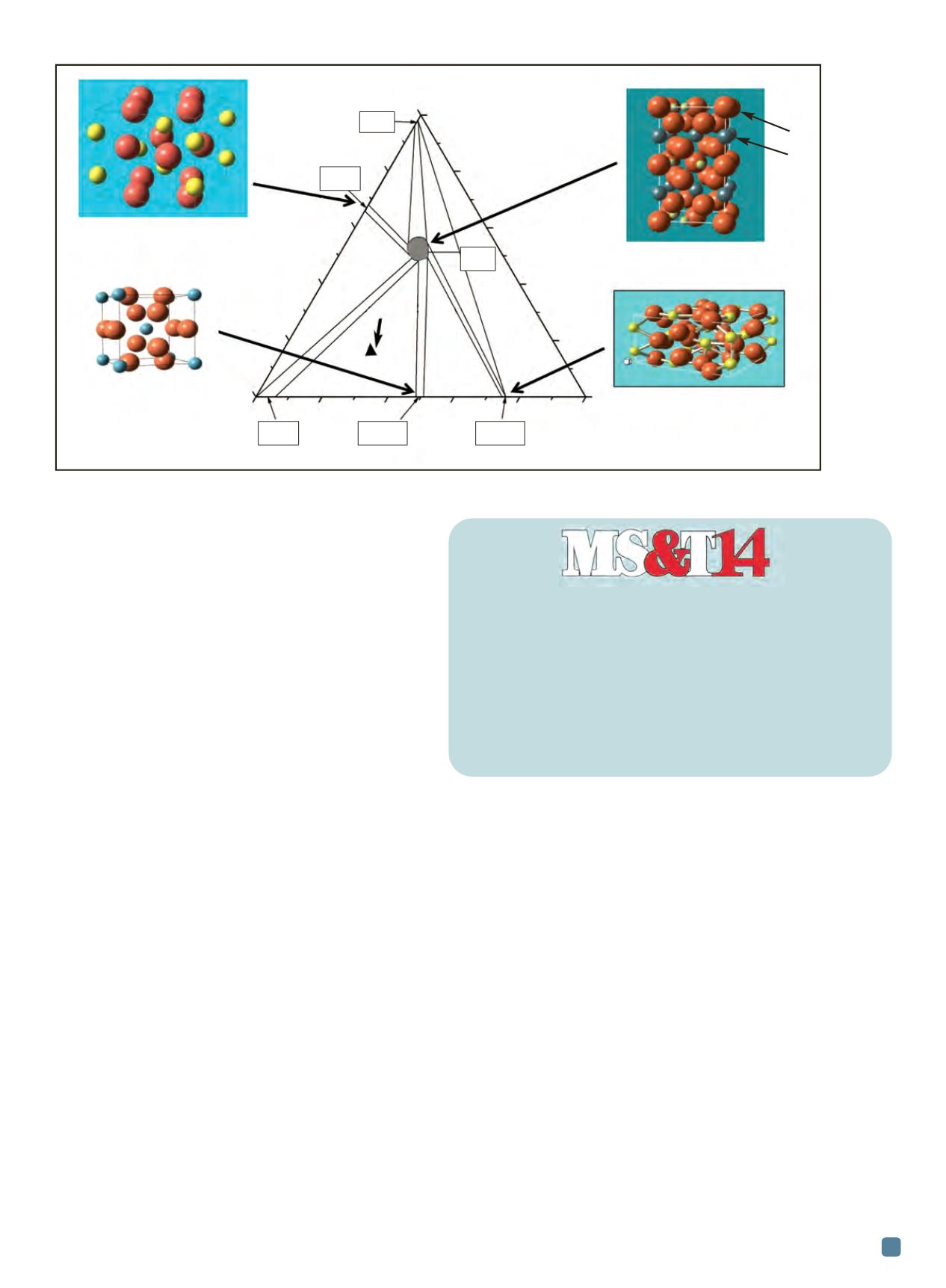
processing steel
[6]
. They demonstrated exceptional oxida-
tion lifetimes with oxide dispersion strengthened Fe
3
Al,
but the relatively high thermal expansion coefficient for
Fe
3
Al and FeAl makes system design a challenge
[7]
. A new
wave of research is now investigating new aspects of these
aluminides. For example, for Fe-Al alloys, a eutectoid reac-
tion from Fe
5
Al
8
to an ultrafine (<100 nm) lamellar struc-
ture of FeAl
2
and FeAl yields a microstructure that can
rapidly form a passivating α-Al
2
O
3
scale upon oxidation
without any internal oxidation.
Advances in strengthening phases
Another advance for intermetallics involves applying
a wider range of strengthening phases for Fe- and Ni-base
alloys. In Ni-base superalloys, the principal strengthening
phase has always been γ’ (Ni
3
Al). However, in a number
of alloy compositions such as alloy 263, the η (Ni
3
Ti)
phase also develops after long-term exposure. Based on a
thermodynamic modeling analysis, composition modifi-
cations involving small additions of V and Ta yield an
increase in the η phase volume fraction above 750°C from
5% up to 15%, which is expected to increase the high tem-
perature strength.
Application of
s
phase in new steels for ultra-super-
critical steam power generation is another surprising de-
velopment. Usually,
s
phase formation is very sluggish so
that it only develops in a microstructure after hundreds of
hours of high temperature exposure and coincides with a
shortening of the rupture life. However, with cleverly de-
signed alloys and annealing processes, when
s
phase is dis-
persed along grain boundaries, it can serve as a valuable
microstructural component to enable a significant en-
hancement of creep resistance.
In a similar manner, austenitic steels strengthened with
Heusler phases, Fe
2
Nb laves phase, NiAl, and Ni
3
Al pre-
cipitates are potential candidates to economically provide
high strength and corrosion resistance for service above
700°C
[8]
. In this case, thermomechanical treatments are
used to produce a refined and uniformly dispersed precip-
itate nanostructure in order to achieve enhanced perform-
ance. Further chemistry changes are being investigated in
some high Mn compositions in order to avoid environ-
mental embrittlement. In addition, nanostructured steels
are being developed with high levels of P-group elements.
In order to achieve ultrahigh temperature capability well
beyond the limit of current Ni-base superalloys, refractory
metal silicide intermetallics offer a number of attractive
characteristics. Yet they also present challenges with re-
gard to developing robust environmental resistance and
innovative processing to achieve multiphase microstruc-
ture designs and morphologies with both high tempera-
ture strength and room temperature toughness
[9-13]
.
Processing is an important component in alloy synthesis
because the requirement for high temperature stability
means that microstructure modification following the ini-
tial alloy synthesis is difficult.
For Mo-Si-B alloys, microstructure designs involving a
continuous molybdenum solid solution, Mo(ss) matrix with
dispersions of Mo
3
Si andMo
5
SiB
2
intermetallics can achieve
ADVANCED MATERIALS & PROCESSES •
SEPTEMBER 2014
23
Fig. 2 —
Mo-rich portion of the Mo-Si-B ternary system featuring the Mo bcc (matrix) phase in equilibrium with the borosilicide (T
2
)
and silicide (Mo
3
Si) phase.
Structural Intermetallics Symposium
Structural Intermetallics in Superalloys,
Monday, Oct. 13, 10:20 a.m.
Silicide Intermetallic Systems,
Monday, Oct. 13, 2:00 p.m.
Heat Treatment, Processing, and Characterization
of Intermetallics,
Tuesday, Oct. 14, 8:00 a.m.
Design Approaches for Structural Intermetallics,
Tuesday, Oct. 14, 2:00 p.m.
Poster Session,
Wednesday, Oct. 15, 11:00 a.m.
Mo
2
B (cubic)
Mo
3
Si (A15) (cubic)
T
2
(tetragonal)
Mo
5
Si
3
(T
1
) (tetragonal)
Mo
Si
1600°C
X Mo
X
B
0.0
0.1
0.2
0.3
0.4
0.5
X Si
Mo-14.2Si-9.6B
0.5
0.6
0.7
0.8
0.9
1.0
0.5
0.4
0.3
0.2
0.1
0.0
MoB
T
2
Mo
2
B
Mo
ss
Mo
3
Si
Mo
5
Si
3