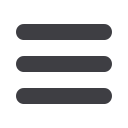
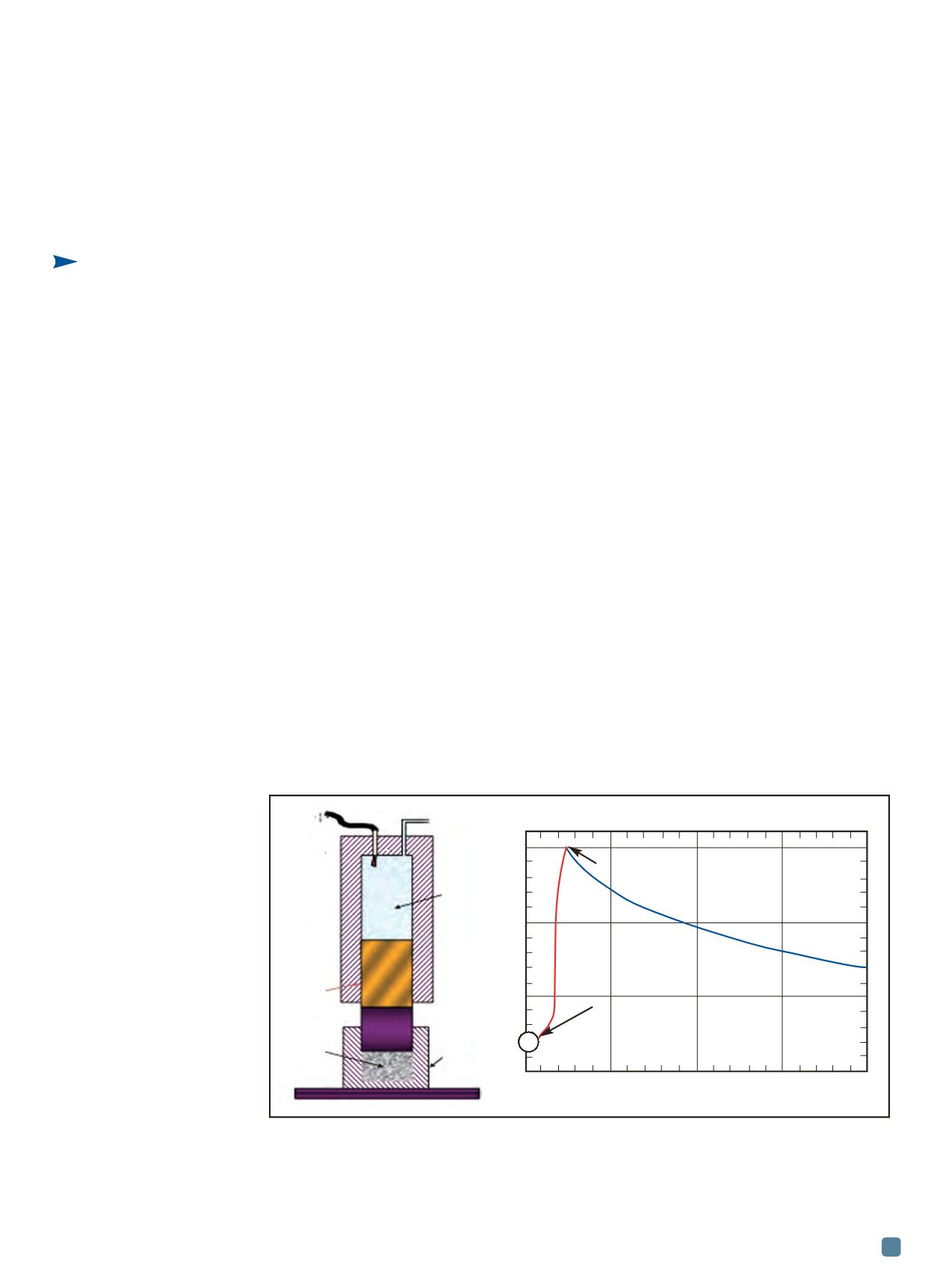
C
onventional manufacturing from
wrought bar stock typically involves
extensive machining, creates signifi-
cant material waste (scrap metal), and requires
numerous steps to obtain the final part geom-
etry. As a more efficient alternative, powder
metallurgical (PM) processes are now available
to cost effectively fabricate both simple and
complex shapes with minimal material waste.
Traditional PM methods involve pressing
powders at relatively low compaction pressures,
typically <50-55 tsi
[1-3]
. However, a new PM
method called
combustion driven higher pres-
sure powder compaction
(CDC) for near-net or
net shape manufacturing
[4-7]
was recently devel-
oped by Utron Kinetics. CDC offers a unique
way of forming near-net or net shape high-den-
sity powder metal components both cost effec-
tively and at relatively higher compaction
pressures (up to 150 tsi) using powders of var-
ious sizes and morphologies.
CDC also works with difficult-to-press
metallic powders, ceramics, and composites by
employing rapid high-pressure powder consol-
idation. Unique advantages of CDC include im-
proved densification in both as-pressed and
sintered conditions, reduced part shrinkages,
enhanced materials properties with wrought-
annealed equivalent behavior, improved
machinability and weldability, and the capacity
to fabricate both single and layered material
combinations. Other benefits include rapid
powder metal alloy development to improve
material properties and performance, minimal
need for post-process machining, and signifi-
cant potential for cost reduction in parts man-
ufacturing. Major progress has occurred during
the past several years in both R&D of unique
powder materials
[5-7]
and cost effective produc-
tion methods.
Advanced applications
Various powders have been compacted into
both simple and complex shapes and success-
fully processed. Powder materials include:
Ferrous (steels, stainless steels); nonferrous
(copper alloys, titanium and Ti alloys, alu-
minum alloys); superalloys such as Inconel 625;
refractory materials including Mo-Re, W-Re,
Re, Ta, Ta-W, TZM, Mo, Nb, and W-base com-
posites
[5,7]
; ceramics (e.g., silicon carbide, boron
carbide, tantalum carbide, hafnium carbides,
tungsten carbides); composites (carbides with
metal matrix composites); and various other
combinations depending on the application
(Figs. 4-7). Commercial high performance ap-
ADVANCED MATERIALS & PROCESSES •
SEPTEMBER 2014
27
Combustion Driven Powder Compaction
Green Manufacturing Enables
Higher Performance Parts
A new and
economical
method
produces
near-net and
net shape
high-density
powder metal
components
at higher
compaction
pressures than
traditional
processes.
Karthik
Nagarathnam
Dennis Massey
Utron Kinetics LLC
Manassas, Va.
Fig. 1 —
Combustion driven higher pressure powder compaction (CDC) process schematic and rapid
pressing cycle time for near-net or net shape CDC fabrication. CDC converts chemical energy directly to
mechanical energy for high efficiency. A pressurized mixture of natural gas and air is ignited to drive a
piston (ram). Fill gas creates preload and pushes the piston or ram down, pre-compressing and removing
entrapped air from the powder. An ignition stimulus is applied, causing combustion and rapid pressure
rise, further compressing the metal powder to its final net shape.
Laser
ignition
Piston
Powder
Gas inlet
Natural
gas or
hydrogen
and air at
high
pressure
Die
250
500
750
Time, ms
Load, tsi (tons/in
2
)
—
Significant preload from
gas fill, 15-20 tsi
Peak loads, 30-250 tsi