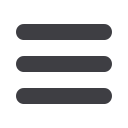
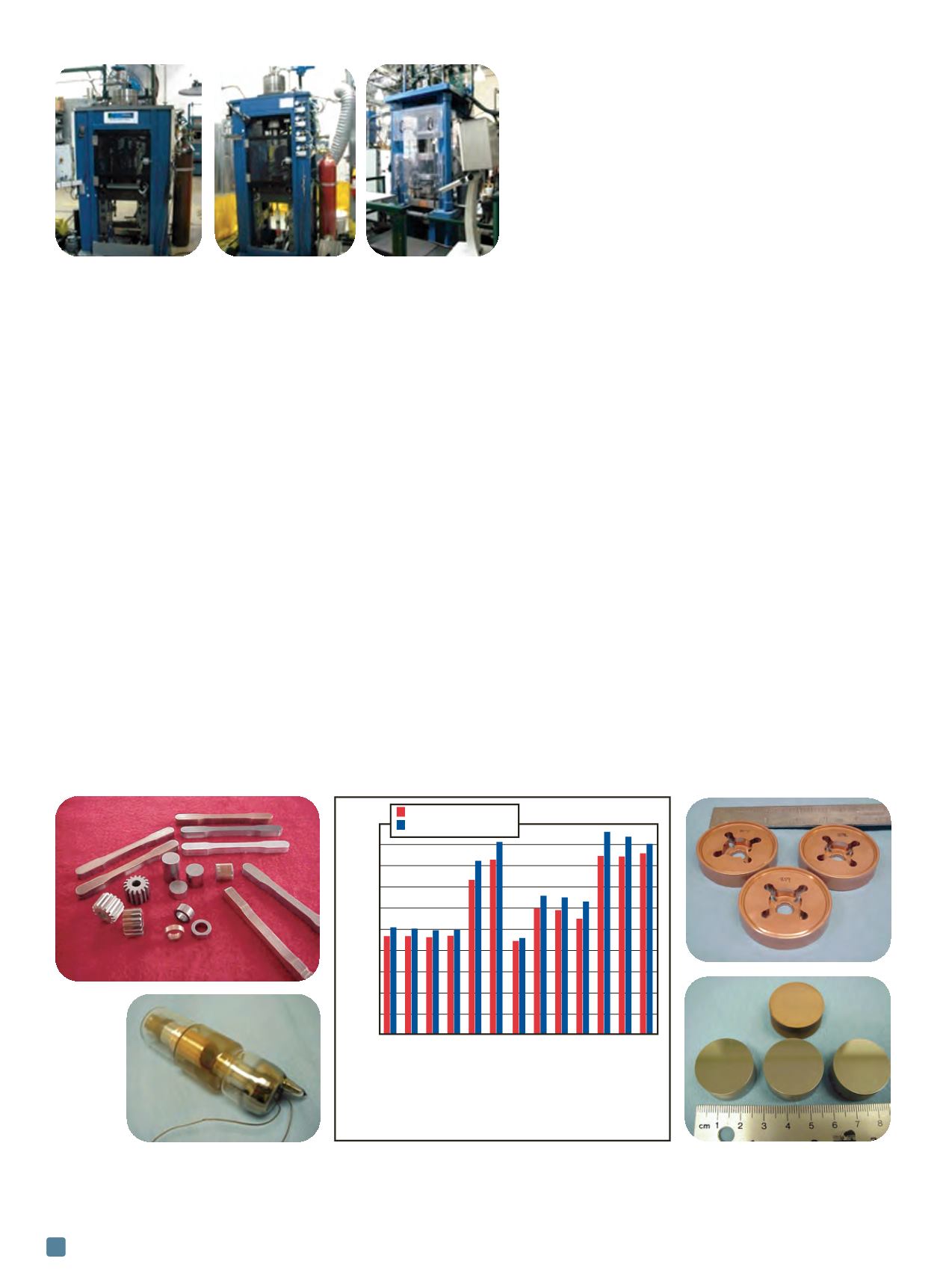
plications using CDC manufacturing include aerospace
and automotive parts, rocket motor components, x-ray tar-
gets, sputtering targets, and other high-density parts using
advanced refractory materials
[5]
. Other innovative applica-
tions involve high performance reactive materials and
components, power transmission parts (e.g., gears and
bearings), permanent and soft magnets with superior mag-
netic properties
[6]
, RF microwave components such as
flanges, seals, and windows, fuel cell electrodes/parts, op-
tical mirror and heat sink substrates, vacuum seals, armor
ceramics, and dissimilar powder pressed layered parts.
High performance PM parts often require demanding
material properties, in addition to reliable performance,
cost effectiveness, and tight tolerances for geometry, di-
mensions, and surface finishes. Some of these include high
vacuum leak resistance, erosion resistance, electron emis-
sion attributes, RF voltage hold-off, high temperature en-
durance, and high electrical and thermal conductivity
attributes. Low alloy steels such as FLN2-4405 are popular
rotorcraft transmission materials, while stainless steels are
useful for corrosion resistance. Popular candidate materi-
als for RF applications include copper-base alloys, stainless
steels, and microwave absorbing ceramics such as SiC,
moly-rhenium, tungsten with barium and other electron-
emitting compounds in the structure, ceramics such as
beryllium oxide (e.g., waveguide windows), OFHC copper,
niobium, aluminum, magnesium diboride, and Nb
3
Sn or
(Nb,Ta)
3
Sn.
Refractory materials such as W, Mo, Ta, Ta-W, and Nb
are useful for various high temperature applications. Ex-
amples include advanced superconducting cryogenic com-
ponents (e.g., Nb in superconducting accelerator
structures), optical mirror substrates and heat sinks (e.g.,
Cu, Mo, Mo/Cu), x-ray targets (W), erosion-resistant, high
temperature rocket motor components, electrode compo-
nents (Mo/Re, W, W/Re, Mo, or Re-base materials), Ta and
Ta-W alloys for advanced defense parts and capacitors, and
high performance fuel cell electrodes made of stainless
steels and other corrosion-resistant materials.
CDC fundamentals
Combustion driven compaction (CDC) converts
chemical to mechanical energy during the controlled
combustion of natural gas or hydrogen and air. The
process then uses this energy to compact powders at
higher compaction pressures than traditional PM meth-
ods, up to 150 tsi. Such controlled combustion reactions
that combine natural gas or hydrogen with environmen-
tally friendly end products using the CDC method result
in a “green” manufacturing technology. In operation, the
following steps occur: The chamber is filled to high pres-
sure with a mixture of natural gas and air; as the chamber
is being filled, the piston or ram is allowed to move down,
precompressing and removing entrapped air from the
powder; the gas supply is closed and an ignition stimulus
is applied, causing the pressure in the chamber to rise
dramatically, further compressing the metal powder to its
final net shape (Fig. 1).
The CDC process is unique in that chemical energy is
directly converted to mechanical energy for rapid powder
ADVANCED MATERIALS & PROCESSES •
SEPTEMBER 2014
28
Fig. 2 —
Various CDC presses. Left to right: 300-ton manual press, 400-ton
manual press, 400-ton automated press.
Fig. 3 —
Examples of CDC geometries using Cu-base alloys for linear collider accelerator applications, and refractory materials
such as Mo for disks and W for x-ray tubes. CDC near-net shape copper has wrought-equivalent properties including high density,
excellent thermal and electrical conductivity, mechanical strength of 32,000 psi, and higher ductility of 45-48% (3a). Improved
densification of CDC refractory metals (3b).
TZM
TZM (fine)
Mo (-325)
Mo (fine)
W M17
W Hi green str.
MoCu 70/30
MoRe 47.5
ReMo47.5 +3%Hf
+2%HfC
MoRe 41
WRe 25
WRe 17
WRe 4
20
18
16
14
12
10
8
6
4
2
0
Density, g/cm
3
As-pressed density
Sintered density
(a) (b) (a)
(a)
(a)